Die casting is a vital manufacturing process that finds its application in producing intricate metal parts with stunning precision. This process, often chosen for its ability to produce large volumes of small to medium-sized parts, requires meticulous planning and expert knowledge for optimal results. Drawing from rich experience, expertise, and authoritative insights, let's delve into the essential design considerations that enhance the efficacy of die casting.
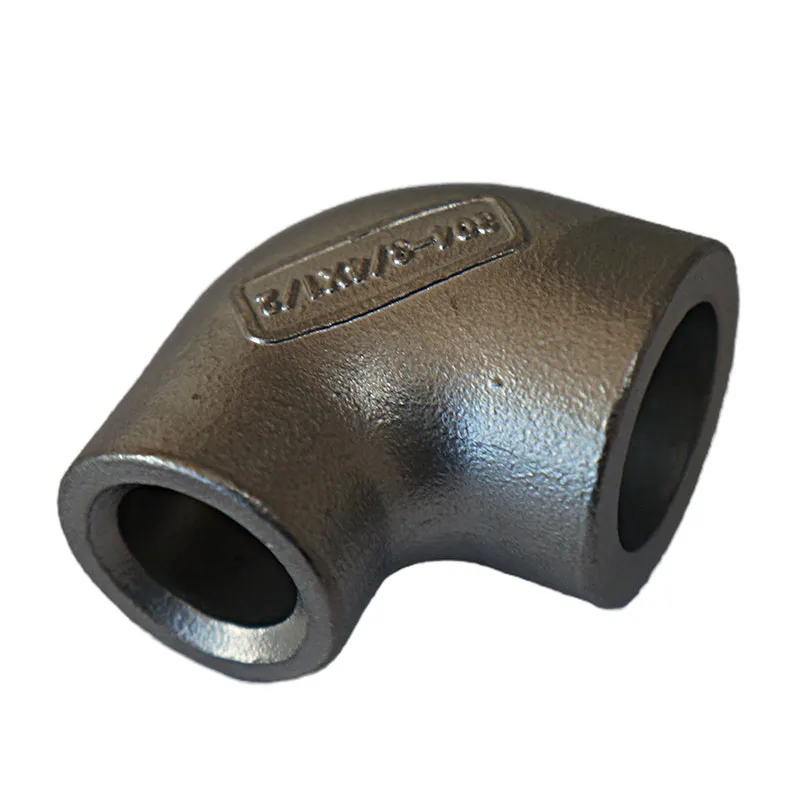
Understanding the Die Casting Process Die casting involves injecting molten metal into a mold cavity under high pressure. This technique delivers products with remarkable dimensional accuracy and an exceptional surface finish. Materials commonly used in die casting include aluminum, magnesium, and zinc. The choice of material will influence the product's mechanical properties, thermal conductivity, and corrosion resistance. A nuanced understanding of material properties and behavior under high temperatures and pressures is critical for effective design and production.
Importance of Tolerances in Design Tolerances play a pivotal role in die casting design. Overly tight tolerances may result in increased production cost and complexity, while excessively loose tolerances can lead to poor fit and function. Designing for manufacturability involves understanding the tight balance between engineering requirements and production capabilities. This balance ensures not only the part's functionality but also its cost-effectiveness and manufacturability.
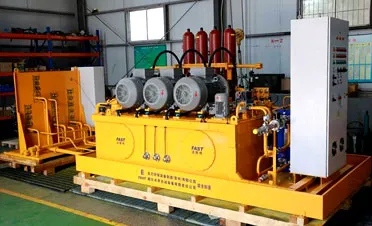
Wall Thickness and Uniformity One of the most significant considerations in die casting design is wall thickness. Uniform wall thickness helps prevent issues such as porosity and undesired stresses from occurring. Optimal wall thickness ensures suitable material flow and cooling, reducing the likelihood of defects. Expertise in wall thickness design is crucial for maintaining product integrity and performance.
Draft Angles An often overlooked but critical factor is the application's draft angles. These are slight angles incorporated into the design to aid in the ejection of the part from the mold. Without adequate draft angles, the part may experience unnecessary friction, leading to damage or deformation during release.
Incorporating Ribs and Fillets Adding ribs and fillets into the design can significantly enhance the structural strength without adding substantial weight or material costs. Ribs can increase stiffness while maintaining lighter profiles, while fillets reduce stress concentrations that can lead to cracking or failure under load.
die casting design considerations
Complexity and Lifecycle Costs While complexity in die casting can allow for component integration, potentially reducing the need for additional assembly, it can also escalate the overall lifecycle cost. Thorough expertise in the cost implications of design choices enables manufacturers to optimize for durability, performance, and price – essential factors for long-term profitability and competitiveness.
Modern Technological Integration Leveraging modern technologies like Computational Fluid Dynamics (CFD) and Finite Element Analysis (FEA) significantly enhances the design process. These tools allow for detailed simulations and analyses, enabling the prediction and reduction of potential defects before physical prototypes are created. Integration of these technologies signals authority and forward-thinking in die casting design.
Sustainability Considerations As environmental consciousness becomes integral to manufacturing, adopting sustainable design approaches in die casting is crucial.
Efficient design can minimize waste material and energy consumption. Expertise in implementing sustainable practices not only boosts a company’s reputation but also its compliance with an increasingly eco-aware marketplace.
Trust and Collaboration with Stakeholders Developing trust with clients and suppliers through open communication and a collaborative design approach can translate into success for die casting projects. Engaging with stakeholders from the initial stages enhances trust, ensuring that the delivered product meets or exceeds expectations.
By considering these intricate details in die casting design, manufacturers can not only optimize their processes but also foster greater innovation and sustainability in manufacturing. The ability to consistently balance experience, expertise, authority, and trustworthiness positions a manufacturer as a leader in a competitive marketplace.