Die casting is a manufacturing process that has revolutionized the production industry by streamlining the creation of metal parts and products. This technique involves injecting molten metal under high pressure into a mold cavity, allowing for the high-volume production of intricate and complex components. However, understanding the cost dynamics of die casting is crucial for businesses looking to optimize their production expenses while ensuring a high-quality finish for their products.
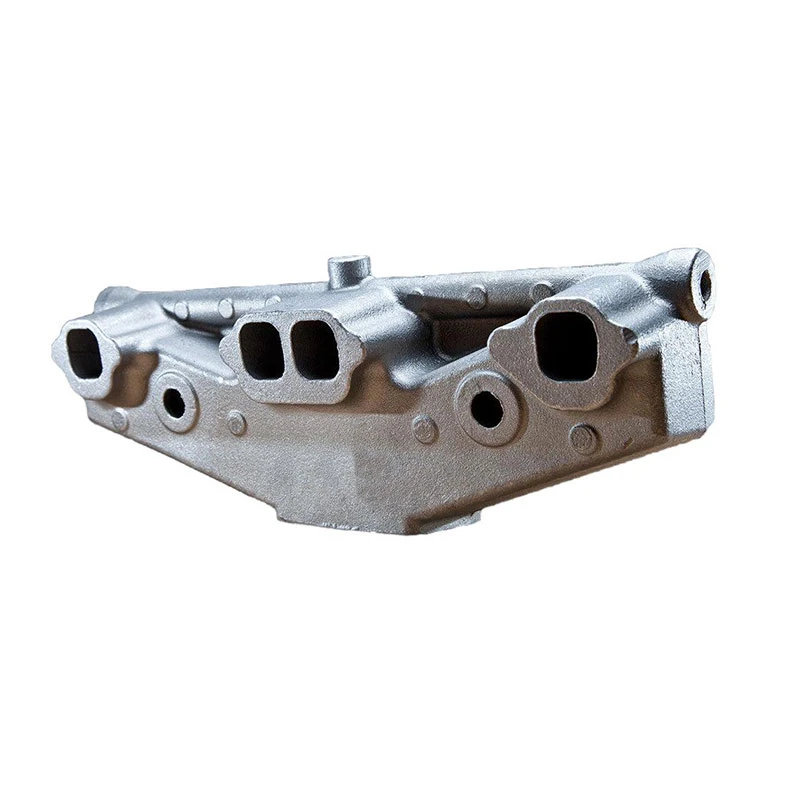
Experience in the field of die casting reveals that several factors collectively influence the overall cost. First and foremost, the choice of material significantly impacts expenses. Materials commonly used in die casting include aluminum,
zinc, and magnesium. Each material has a different cost per pound and varying properties that influence the final cost of the product. For example, aluminum is lightweight and highly resistant to corrosion, making it a popular choice, though it may incur higher costs than other materials due to these advantageous properties.
The complexity of the part being cast is another critical factor that contributes to cost. Parts with intricate details and tight tolerances require more sophisticated and precise tooling, which raises the initial cost of the die. Moreover, the machine size and the cycle time also play crucial roles. Larger machines that can accommodate bigger parts may cost more to operate, while longer cycle times can decrease output and increase labor costs.

Speaking of cycles, the production volume directly affects the cast cost. Die casting is particularly cost-effective for large-scale production due to economies of scale. Higher volumes allow the high initial costs of tooling and setup to be spread over more units, significantly reducing the per-unit cost. For low-volume production, however, these fixed costs can substantially increase the cost per unit, making other processes like CNC machining or 3D printing more economical depending on the complexity and size of the parts.
die casting cost
Expertise in die casting also emphasizes the importance of optimizing the design for manufacturing. By simplifying geometries and minimizing the use of inserts or post-production machining, manufacturers can reduce waste and streamline the production process. Collaborative efforts between the design and manufacturing teams can lead to innovative approaches that balance performance, aesthetics, and cost.
Investing in quality tooling is another authoritative strategy for managing die casting costs. High-quality tooling may come with a higher initial price tag, but it provides better lifecycle value through improved durability and precision, reducing downtime and maintenance expenses. Ensuring regular maintenance and timely upgrades of machinery and tools also promotes efficiency, leading to long-term cost savings.
Trustworthiness in choosing a die casting partner can significantly affect the economic outcomes. Reliable suppliers provide not only high-quality end products but also contribute valuable insights into cost-saving practices. Establishing a transparent relationship, involving detailed cost breakdowns and collaborative problem-solving, fosters a favorable foundation for successful projects.
In conclusion, understanding and managing die casting costs involves a multifaceted approach that takes into account material choice, design complexity, production volume, and the quality of tooling. By considering these factors and leveraging both industry experience and expertise, businesses can strategically navigate the complexities of die casting. A thorough understanding of the process and a reliable partnership with a knowledgeable die casting provider can transform potential cost barriers into competitive advantages, allowing for the production of high-quality components at optimal costs.