Casting green sand is an essential component in the manufacturing and foundry industries, providing a versatile and cost-effective medium for creating molds. Drawing from years of hands-on experience and deep expertise, this article delves into the intricacies of green sand casting, highlighting why it remains a trusted method for producing high-quality components.
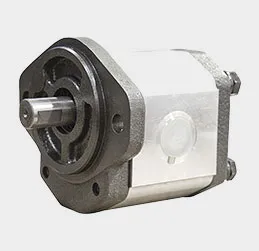
Green sand is composed primarily of silica sand, bentonite clay, and water, with optional additives to enhance specific properties of the mold. This mixture is lauded for its recyclability and flexibility, allowing foundries to produce detailed and complex parts efficiently. Its ability to withstand high temperatures and pressures without compromising the integrity of the finished product makes it indispensable in various casting scenarios.
The expertise required in manipulating and optimizing green sand involves precise control over its moisture content, clay-to-sand ratio, and compaction level. These factors influence the mold's permeability, strength, and surface finish. Foundry specialists are adept at adjusting these variables to tailor the sand's properties to specific casting needs. For instance, increasing the clay content can improve mold strength, but it may also reduce permeability, necessitating careful balance.
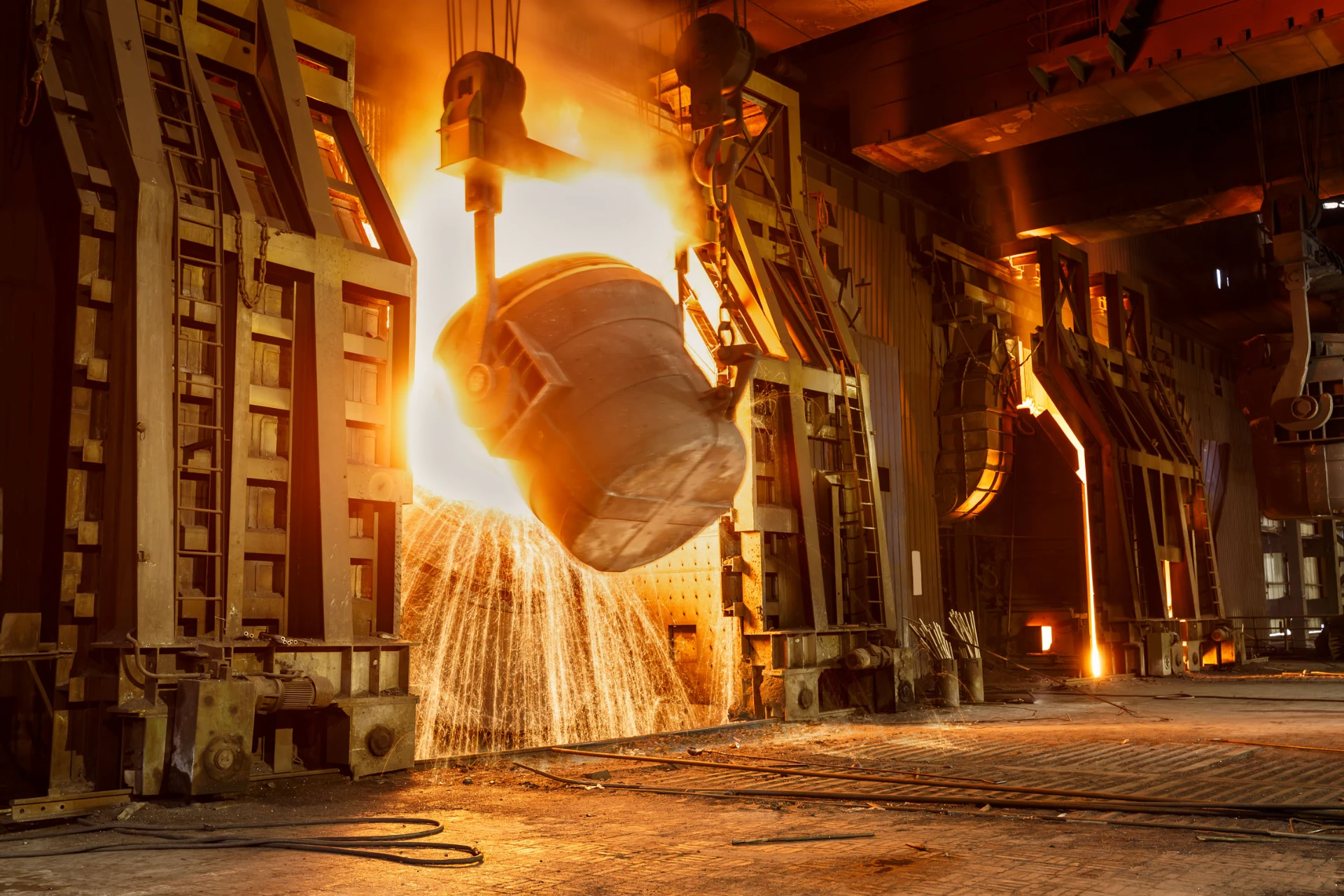
Authoritativeness in this domain comes from a profound understanding of the core principles of green sand casting. Historically, green sand has been a staple in metal casting processes since the Bronze Age, attesting to its enduring reliability and adaptability. Modern advancements have been built on this foundation, incorporating sophisticated technology to monitor and refine mold quality consistently.
casting green sand
The trustworthiness of the green sand casting process is underscored by its widespread acceptance in industries producing automotive components, machinery parts, and even artistic sculptures. This technique's ability to produce large batches of identical parts with minimal material waste and high precision contributes to its sustainability and economic viability. Furthermore, green sand casting supports a variety of metals, including iron, aluminum, and copper alloys, making it a versatile choice for manufacturers.
A robust green sand system requires diligent management. Regular testing of sand properties ensures optimal performance, where factors such as grain size distribution, compactability, and moisture levels are routinely assessed. Implementing a rigorous quality control regimen establishes a dependable system capable of producing consistent results. Foundries often employ state-of-the-art equipment to automate these processes, reducing human error and enhancing overall mold quality.
In conclusion, the casting green sand process embodies a harmonious blend of traditional methods and modern technology, driven by a deep-seated expertise and a commitment to sustainability. It holds a revered place in the manufacturing world, trusted for its reliability and efficiency. Embracing advancements in digital monitoring and process optimization, green sand casting represents an evolving yet steadfast technique, ensuring that manufacturers can continue to produce high-quality products with precision and confidence.