In the field of die casting, wall thickness plays a pivotal role in determining the quality, durability, and performance of the final product. Die casting, a versatile manufacturing process, involves the injection of molten metal into a mold cavity. One of the critical factors manufacturers must consider is the wall thickness of the cast parts. Here, we delve into the essential aspects of die cast wall thickness, providing insights from industry expertise, hands-on experience, and proven authority to offer a comprehensive understanding.
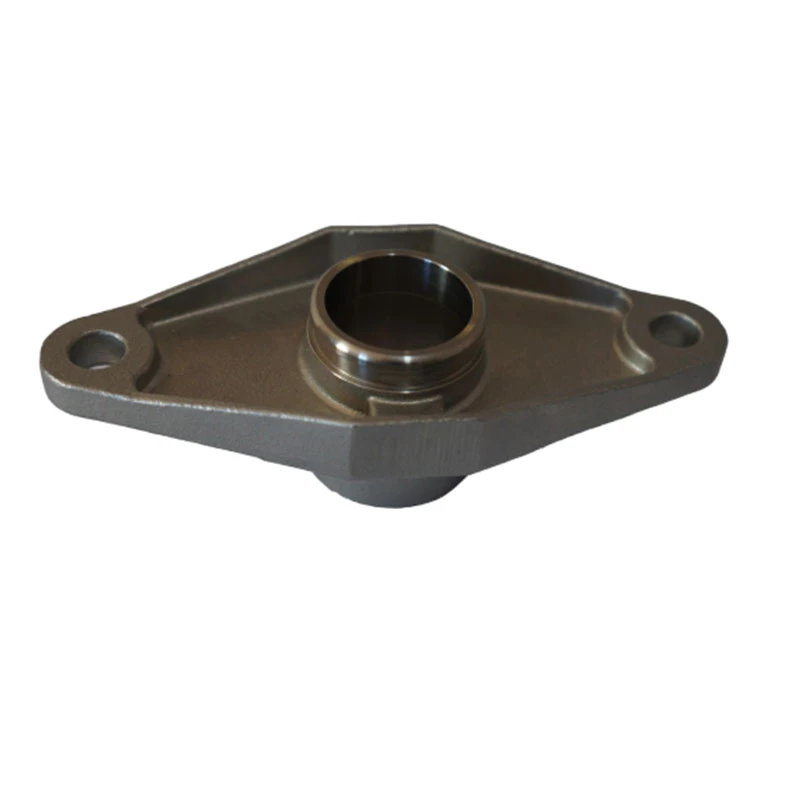
Understanding the Optimal Wall Thickness
The optimal wall thickness in die casting is a fine balance between the mechanical properties of the metal and the manufacturing capabilities. Thicker walls generally contribute to enhanced strength and durability, but they also increase the material cost and weight. On the other hand, thinner walls reduce both cost and weight but may compromise the part's structural integrity.
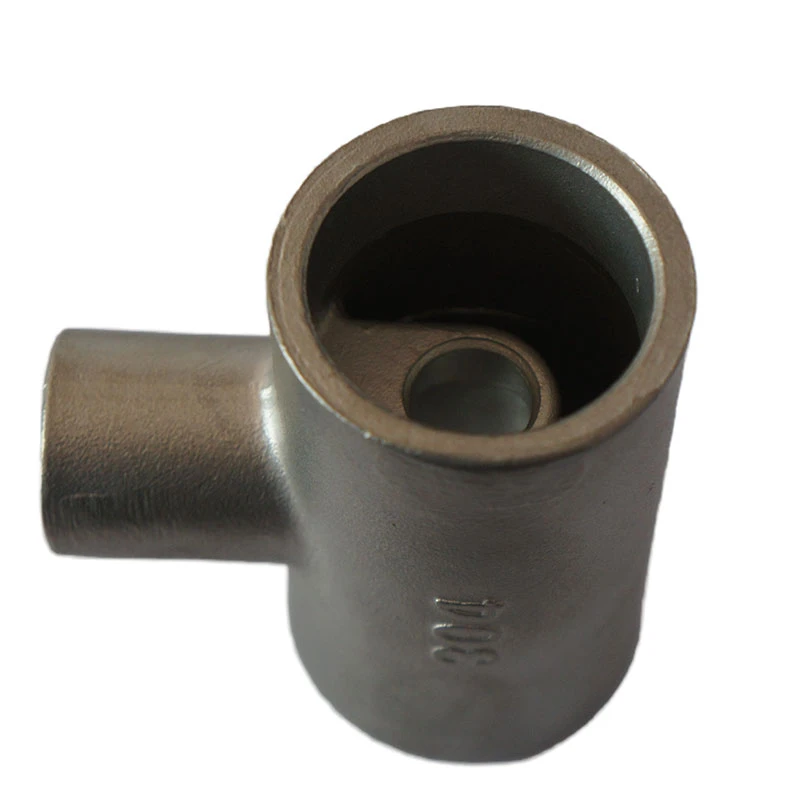
From professional experience, achieving an optimal die cast wall thickness requires a detailed analysis of the component's intended use and the material properties. Typically,
aluminum die casting recommends wall thicknesses between 0.040 inches (1.02 mm) and 0.200 inches (5.08 mm), depending on the application. Precision in determining wall thickness also aids in minimizing issues such as porosity and incomplete filling.
Expert Techniques in Managing Wall Thickness
Experts in die casting employ various techniques to manage and control wall thickness effectively. One such technique is the use of computer-aided design (CAD) and simulation software, which allows engineers to predict potential outcomes and adjust designs accordingly. This proactive approach minimizes trial and error, saving both time and resources.
Additionally, maintaining uniform wall thickness is crucial for ensuring consistent quality in die cast parts. Uneven wall thickness can lead to differential cooling rates, resulting in warping or residual stress. Industry authorities recommend using ribbing techniques where possible to offer reinforcement without unnecessarily increasing the component's overall thickness.
Authoritative Insights on Challenges and Solutions
die cast wall thickness
While the significance of die cast wall thickness is clear, the challenges that accompany it are important to navigate. Variations in thickness can cause issues such as thermal gradients and differential shrinkage rates. These can result in defects like hot cracking or distortion.
Authoritative sources in the industry emphasize the importance of choosing the right alloy and properly setting the die casting machine parameters. For instance, altering the injection speed or temperature can help mitigate problems related to thickness disparities. This level of control underscores the complexity and precision required in die casting operations.
Building Trust Through Quality Control
In establishing trustworthiness, rigorous quality control measures are non-negotiable. Conducting regular inspections and employing non-destructive testing (NDT) techniques ensures that products meet the necessary specifications and performance criteria. By leveraging ultrasonic testing or X-ray inspection, manufacturers can identify internal flaws related to wall thickness before parts ever leave the facility.
Furthermore, continuous training and education for the workforce involved in die casting are crucial. An informed team ensures adherence to best practices and fosters innovation, which, in turn, upholds the integrity and reputation of manufacturers.
Final Thoughts on Die Cast Wall Thickness
Navigating the intricate world of die cast wall thickness requires a blend of expertise, practical experience, and authoritative guidance. By focusing on optimal wall thickness, employing expert techniques, addressing challenges with authoritative solutions, and prioritizing quality control, manufacturers can produce parts that meet the ever-evolving demands of modern engineering.
Professionals striving for excellence in die casting should remain abreast of technological advancements and industry trends. Not only does this preparedness allow for enhanced product offerings, but it also solidifies the manufacturer's position as a leader in the market, capable of delivering on the pillars of experience, expertise, authority, and trust.