Aluminum casting costs encompass a broad spectrum of considerations that manufacturers and businesses must navigate to optimize production and remain competitive. Engaging with the multifaceted nature of these costs requires an understanding of both the material properties and the methodologies employed in the industry. Here is an exploration of factors influencing aluminum casting costs with a focus on experience, expertise, authoritativeness, and trustworthiness.
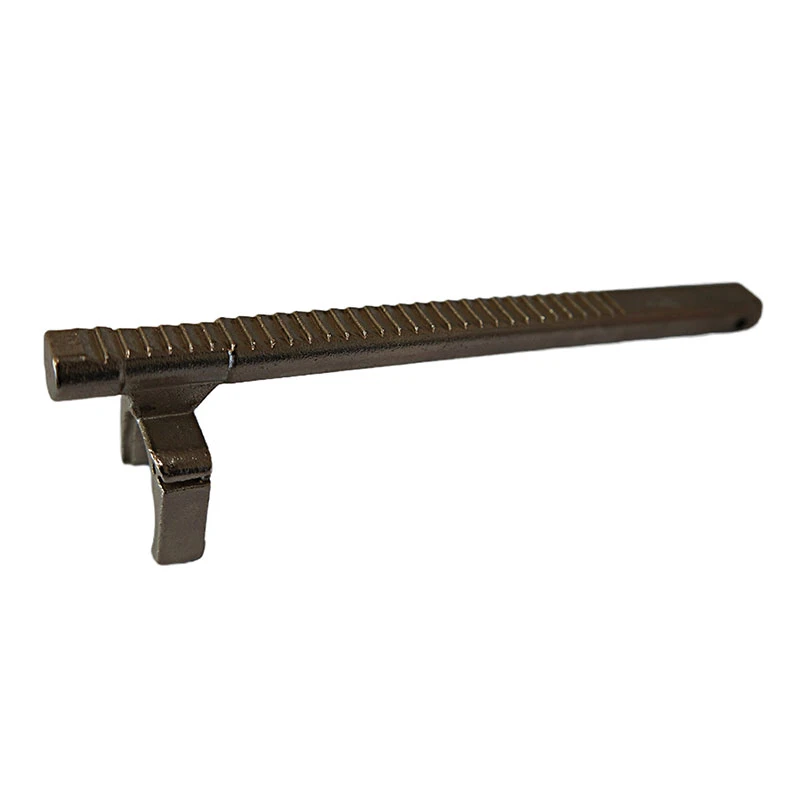
Understanding the core components of aluminum casting cost first involves material considerations. Aluminum's lightweight properties, corrosion resistance, and high thermal conductivity make it a favorable choice for various industrial applications, including automotive, aerospace, and consumer electronics. Industry experts cite that sourcing aluminum alloys can vary widely in cost depending on market fluctuations, quality, and specific alloy composition required for the casting process.
Casting methods play an instrumental role in defining cost efficiency and quality outcomes. Die casting is renowned for its precision and repeatability, yet it demands significant initial capital investment due to the tooling required. Alternatively, sand casting might present lower upfront costs, but involves greater manual labor and process complexity that can increase variable costs. Industry experience shows that selecting a casting method aligns closely with production volume and part complexity, hence influencing total cost. Insight from seasoned professionals suggests that manufacturers often benefit from conducting a cost-benefit analysis tailored to their specific production needs when choosing between casting methods.
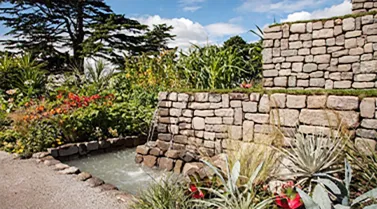
Production scale remains a decisive factor in determining aluminum casting costs. High-volume projects often leverage economies of scale, thereby reducing per-unit cost significantly. For smaller-scale productions, manufacturers may face increased per-unit expenses due to less optimized resource utilization. Expertise in the field suggests that businesses should carefully evaluate their production forecasts and adjust their casting strategies to leverage batch processing capabilities effectively. Additionally, efficient scheduling and advanced production planning can mitigate bottlenecks, thus enhancing cost efficiency.
aluminum casting cost
Labor costs constitute another critical aspect of casting expenses. Skilled labor is essential to ensure precision in the casting process, and the availability of such talent can vary regionally, affecting cost structures. Authoritative sources in the field recommend implementing training programs and investing in automation to balance labor costs while maintaining high quality standards. Trustworthy data indicates that adopting emerging technologies, like CNC machining and advanced robotics, can yield longer-term cost savings by minimizing human error and enhancing consistency.
Quality control and testing are additional factors contributing to aluminum casting costs. High standards of quality assurance can prevent costly defects and ensure customer satisfaction, thus safeguarding reputational capital. Methods such as non-destructive testing (NDT) and X-ray inspection, while adding to upfront costs, can ultimately reduce costs by preventing failures and reducing returns. Experienced manufacturers advocate for a robust quality control framework that integrates real-time data analysis to swiftly address discrepancies and implement corrective actions.
Finally, sustainability initiatives are increasingly impacting aluminum casting costs. The trend toward eco-friendly processes and materials not only reflects corporate responsibility but also influences direct costs. Recycling aluminum, adopting cleaner production technologies, and minimizing waste can lead to cost reductions through reclaimed materials, reduced waste disposal fees, and improved energy efficiency. Trustworthy reports emphasize that integrating sustainability into the production model can enhance brand reputation and align with evolving regulatory standards, adding value that goes beyond immediate financial metrics.
In summary, navigating aluminum casting costs requires a blend of material knowledge, process expertise, and strategic foresight. By attentively balancing these elements, businesses can achieve precision, sustainability, and cost efficiency in their casting operations. The dynamic nature of the industry underscores the importance of continuous learning and adaptation to maintain a competitive edge.