Aluminium gravity die casting is a crucial process in modern manufacturing, offering a blend of affordability, efficiency, and precision that few other methods can match. This method, often simply referred to as gravity casting or permanent mold casting, harnesses the force of gravity to fill a mold with molten aluminium, producing robust and detailed components essential for numerous industries.
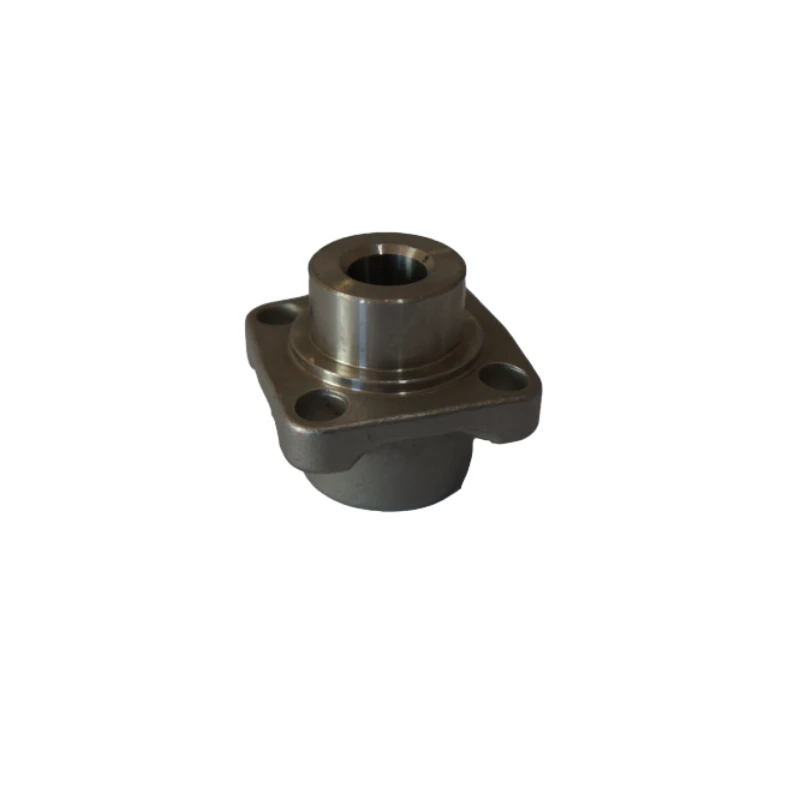
In the ever-evolving world of industrial manufacturing, aluminium gravity die casting has emerged as a cornerstone due to its ability to produce high-strength components with excellent durability. This process begins with the careful preparation of a mold typically made from steel or cast iron, designed with the utmost precision to meet specific production requirements. The mold’s durability is paramount as it can be used repeatedly, offering both economic and environmental benefits by reducing material waste.
One of the key advantages of aluminium gravity die casting is its ability to produce parts with superior mechanical properties. Aluminium, known for its lightweight characteristics and excellent corrosion resistance, makes it ideal for automotive, aerospace, and consumer electronics applications where weight reduction and longevity are paramount. By eliminating the need for external pressure or vacuum, this process reduces mold wear, thereby extending the tool’s lifecycle and enhancing cost efficiency.
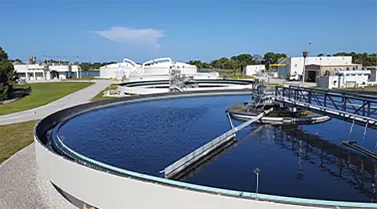
From an expert’s perspective, the aluminium gravity die casting process provides a unique blend of repeatability and complexity. It is ideal for middle to high-volume production runs, where consistency and precision are non-negotiable. The process is known for producing components with excellent surface finishes and tight dimensional tolerances, which minimizes the need for secondary machining operations. This contributes to faster production cycles and significantly reduced production costs.
In terms of design flexibility, the process allows for intricate geometries that are difficult or even impossible to achieve with other casting methods. This flexibility is achieved without compromising the structural integrity of the final product, making the process suitable for manufacturing complex automotive engine components, intricate aerospace assemblies, and detailed electronic housings.
The expertise required to successfully implement gravity die casting extends beyond technical knowledge of the equipment and process. It includes the skillful design of molds, precise control of pouring temperatures, and careful monitoring of the casting environment to prevent common defects such as porosity and shrinkage. Mastery of these variables is crucial in ensuring that the final product meets or exceeds industry standards.
aluminium gravity die casting
Industry leaders trust aluminium gravity die casting for its reliability and precision. Companies in sectors as diverse as transportation, electronics, and infrastructure rely on components made through this process due to their consistency and performance. The process doesn’t just offer high-quality outcomes but does so at scale, enabling manufacturers to meet large order demands without sacrificing quality.
Moreover, aluminium gravity die casting aligns with modern environmental and efficiency standards. The repeatability of the process reduces material waste, and the recyclability of aluminium further enhances its appeal. In an era where sustainability is as critical as production cost and efficiency, processes like this become increasingly vital.
Trustworthiness in casting processes is built over time through consistent and reliable outcomes, adherence to stringent quality standards, and the application of advanced technologies and materials. As the demand for lightweight and durable components grows, the role of aluminium gravity die casting becomes even more significant. This method is not just about casting metal; it’s about shaping the future of manufacturing with innovation and integrity.
The future of aluminium gravity die casting is bright, with advancements in simulation technology and automation promising to enhance precision and reduce production times even further. As industries continue to evolve, embracing smart manufacturing and design trends, this process will undoubtedly remain at the forefront, bolstered by ongoing research and development efforts aiming to push the boundaries of what is possible in the world of casting.
In conclusion, aluminium gravity die casting stands as a testament to the power of precise engineering and reliable manufacturing processes. Its applications are broad and impactful, proving essential in creating the products that drive modern society forward. Through its unmatched combination of efficiency, sustainability, and quality, it offers a clear path to manufacturing excellence.