Gravity die casting, a profound technique within the manufacturing sector, yields a wide array of benefits through its diverse types. This advanced form of casting, known for producing high-precision components, revolves around the principle where molten metal is poured into a metal mold through the force of gravity. Understanding the various types of gravity die casting, their distinct methodologies, and applications enhances the quality and efficiency of metal components used across industries.
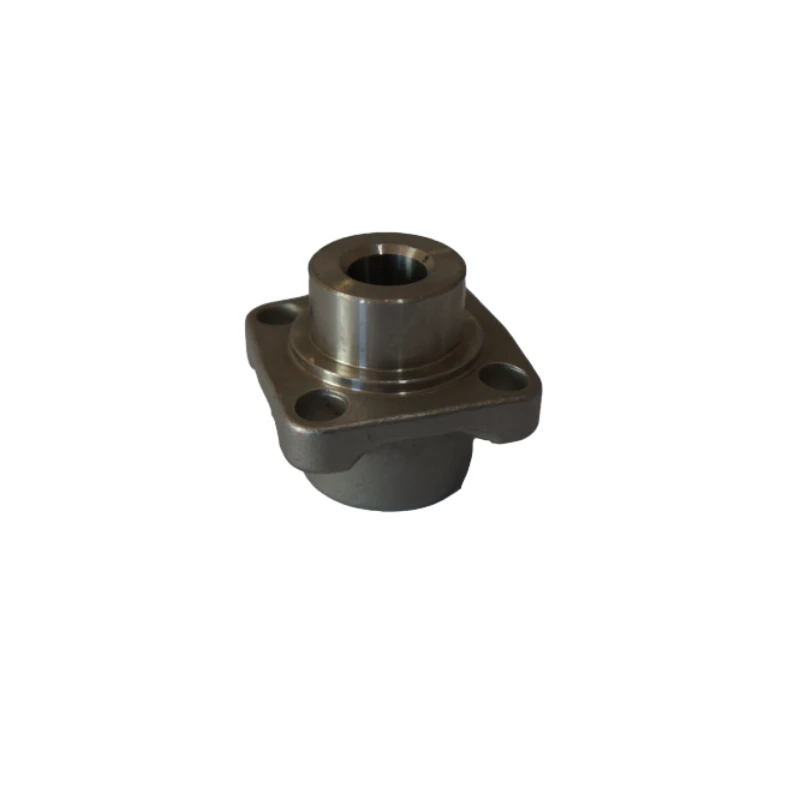
Permanent Mold Casting stands out as a prevalent type within gravity die casting. This method involves the use of durable metal molds constructed from materials like steel or cast iron. These molds can be reused numerous times, making them cost-effective and efficient for high-volume production. Key applications of permanent mold casting include the automotive industry, where critical components such as engine blocks, cylinder heads, and various structural parts are manufactured. The consistent mechanical properties and dimensional accuracy provided by this method are invaluable, ensuring strict adherence to industry standards.
Additionally, Semi-Permanent Mold Casting represents an innovative variation of traditional permanent mold casting. This technique encompasses the use of sand cores within a permanent metal mold, facilitating the creation of complex internal geometries within the cast product. This hybrid approach capitalizes on the strength of metal molds and the design flexibility offered by sand cores. The aerospace and marine sectors frequently utilize this method to manufacture intricate components such as gear housings, pump bodies, and impellers, which require precise internal features and high strength-to-weight ratios.
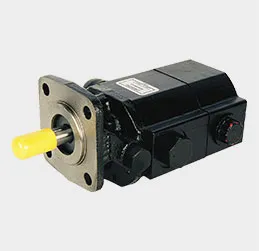
types of gravity die casting
Tilt Pouring, another specialized type of gravity die casting, introduces a dynamic aspect to the casting process. The mold is gradually tilted during the pouring operation, allowing the metal to flow smoothly and evenly into the mold cavity. This tilt mechanism reduces turbulence, minimizes porosity, and enhances the overall uniformity of the cast product. Tilt pouring is particularly advantageous for components needing impeccable surface finish and intricate detailing, commonly applied in manufacturing electronics enclosures, decorative castings, and appliances where aesthetic appeal complements functionality.
Furthermore, Low Pressure Die Casting, while sometimes categorized under pressure casting, shares similarities with gravity die casting in terms of mold utilization. In this technique, a controlled amount of pressure assists gravity to facilitate the molten metal's entry into the mold. This results in finer-grained structures and improved mechanical properties in the cast components. Low pressure die casting is typically employed in producing high-integrity components such as wheel rims, suspension parts, and structural components subjected to dynamic stress, predominantly in the transportation industry.
Each type of gravity die casting offers distinct advantages tailored to specific industrial needs, underscoring the importance of selecting the appropriate technique for each application. Understanding and leveraging the unique benefits of permanent mold casting, semi-permanent mold casting, tilt pouring, and low pressure die casting ensures that manufacturers meet stringent quality standards while optimizing production efficiency. Through continuous innovation and the adoption of advanced materials, gravity die casting maintains its position as a cornerstone technology in modern manufacturing.