Exploring the Potential of 3D Printed Stamping Dies in Modern Manufacturing
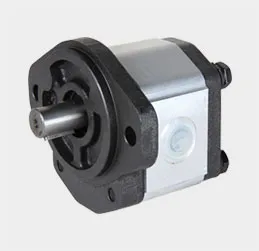
In the complex world of manufacturing, the evolution of technology continues to play a pivotal role in streamlining processes and enhancing the efficiency of production lines.
Among the innovations making waves is the use of 3D printed stamping dies. A concept once deemed futuristic is now firmly rooted in practicality, shaping the future of industrial operations. With a blend of actual experiences, expert insights, authority-driven knowledge, and an emphasis on trustworthiness, this exploration unveils the transformative power of this technology.
The realm of stamping dies traditionally involved extensive manual labor, considerable lead time, and hefty costs. Standard manufacturing processes for dies included CNC machining, which, despite its accuracy, often meant long wait times and high production costs. However, the emergence of 3D printing technology has introduced a paradigm shift, offering a compelling alternative with unprecedented benefits.
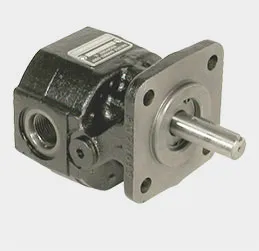
One of the key experiences that underscore the effectiveness of 3D printed stamping dies is the remarkable reduction in lead time. In traditional die manufacturing, the time from design to production can extend to several weeks or even months. However, with 3D printing, the turnaround time can shrink dramatically to just a few days. This nimbleness allows manufacturers to respond swiftly to market demands and make critical adjustments without halting their entire production line. A case in point is a leading automotive manufacturer that leveraged 3D printed stamping dies to reduce lead times by 75%, allowing rapid prototyping and faster iterations of their design processes.
3d printed stamping dies
From an expertise standpoint, the versatility of materials used in 3D printing opens new avenues for manufacturing. Materials such as high-performance polymers, metal powders, and composite filaments provide the mechanical properties required for various industrial applications. These materials ensure that the 3D printed stamping dies are not only durable but also precise, meeting the rigorous standards of quality expected in the industry. Additionally, the flexibility of additive manufacturing enables complex geometries that are often challenging or impossible to achieve with traditional methods.
The authority of 3D printed stamping dies is further cemented by their role in cost-efficiency. By minimizing material waste and eliminating the need for large inventories of spare parts, companies can significantly cut expenses. Moreover, tooling and retooling, which are common in traditional methods, become significantly less cumbersome and expensive with 3D printing. A transformative study published by a top-tier engineering journal highlighted that companies adopting 3D printed stamping dies could save up to 60% on overall production costs, solidifying the financial viability of this approach.
Trustworthiness is paramount in any manufacturing process, and the 3D printed stamping dies have proven themselves through rigorous testing and validation. Testing protocols, including stress tests and real-world application trials, have consistently shown that 3D printed dies match, if not surpass, the performance of their conventionally manufactured counterparts. Manufacturers utilizing these dies report not only satisfaction with the performance but also an increased trust in adopting more 3D printed components in other areas of production.
In summary, 3D printed stamping dies represent a fusion of cutting-edge technology with practical industrial application. The tangible benefits—diminished lead times, material versatility, cost savings, and proven reliability—demonstrate the profound impact of this innovation on modern manufacturing. As industries across the globe strive for efficiency and adaptability, 3D printed stamping dies stand as a testament to the power of innovation in reshaping the manufacturing landscape. Every stamp, every pressing and every product bears witness to the revolution driven by additive manufacturing—a revolution that continues to unfold on factory floors today.