Exploring the world of zinc sand casting unveils a fascinating blend of traditional techniques and modern advancements. As a pivotal force in manufacturing, zinc sand casting is celebrated for crafting intricate components with precision and efficiency. This process is exemplary in various industries, providing unique advantages that cater to diverse needs while ensuring high-quality production.
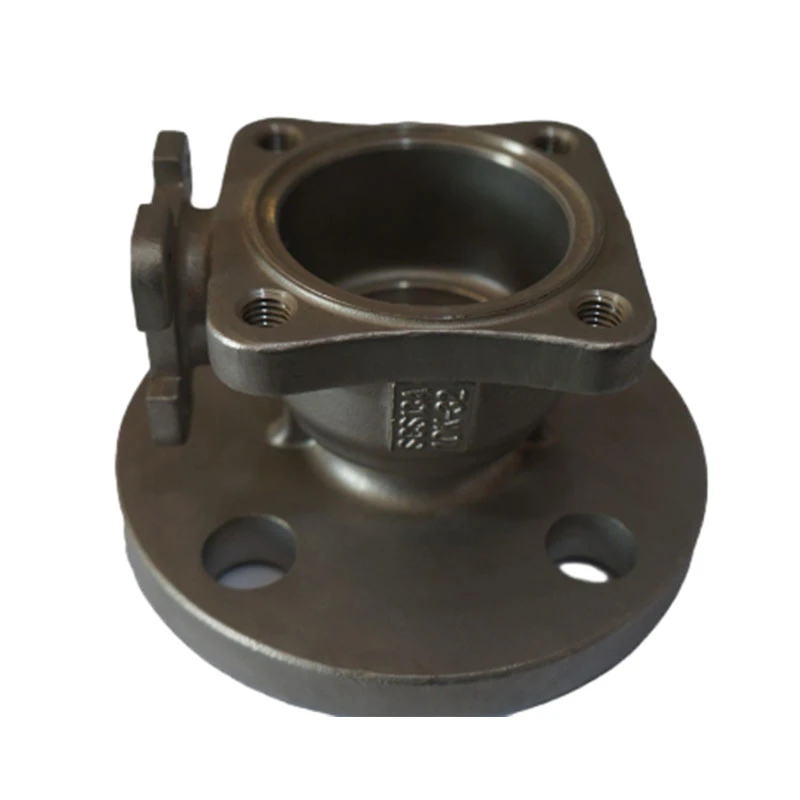
Zinc sand casting embodies a marriage between time-honored methods and cutting-edge technology. At its core, this process involves creating a sand mold into which molten zinc is poured to form complex structures. The flexibility of sand allows manufacturers to generate detailed and customized designs while maintaining economic feasibility. This capability makes zinc sand casting a preferred choice for sectors such as automotive, aerospace, and electrical industries.
The expertise in zinc sand casting offers distinct benefits that underscore its effectiveness. One of the main advantages is its ability to produce parts with excellent corrosion resistance. Zinc, being inherently resistant to oxidation, elongates the lifespan of components it forms, making it particularly advantageous for applications exposed to harsh environmental conditions. Moreover, zinc alloy compositions, specifically developed for sand casting, enhance mechanical properties such as strength and ductility, meeting stringent performance requirements.
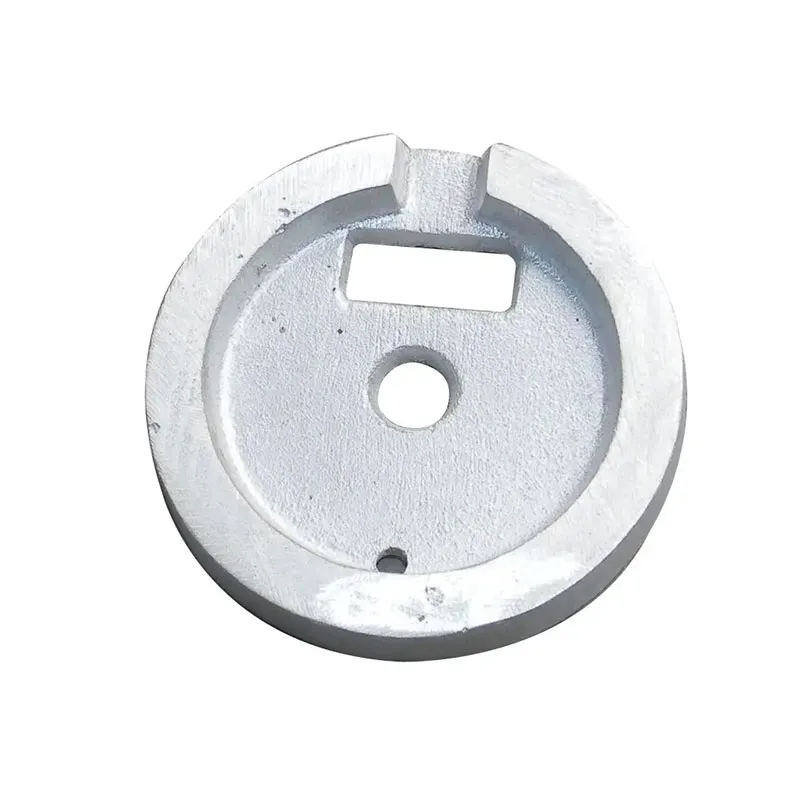
In terms of experience, manufacturers who leverage zinc sand casting often emphasize its cost-effectiveness. This process minimizes material waste and typically requires less machining compared to other production methods, reducing costs significantly. Additionally, sand casting enables high-volume production runs with quick turnarounds, which is crucial for industries needing scalability and prompt delivery. The adaptability of sand molds to incorporate multiple casting units simultaneously further contributes to efficiency.
Authoritativeness in zinc sand casting stems from its long-standing presence in manufacturing domains. Over the years, the process has evolved to incorporate automated technologies that increase precision and repeatability. Recent innovations include the integration of computer-aided design (CAD) and computer-aided manufacturing (CAM) systems, which refine mold design and optimize flow dynamics of molten zinc. These advancements ensure that each casting meets exacting standards, reinforcing zinc sand casting’s status as a reliable manufacturing process.
zinc sand casting
Trustworthiness in zinc sand casting is embodied by industry regulations and standards aimed at ensuring quality and safety. Compliance with international standards, such as ISO and ASTM, is crucial for component reliability and serves as a testament to the process's credibility. Manufacturers consistently invest in quality control measures, such as X-ray inspection and tensile strength assessments, to maintain the integrity of cast components.
Furthermore, environmental sustainability is an emerging focus in zinc sand casting. As industries shift towards eco-friendly practices, zinc casting aligns with sustainability goals due to its recyclable nature. Zinc components can be re-melted and recast, minimizing environmental impact and conserving resources. This adaptability to green manufacturing practices positions zinc sand casting as a future-forward process that addresses both industrial needs and environmental concerns.
For product lines reliant on precision and durability, zinc sand casting offers a compelling combination of benefits. Its adaptability to produce ranging sizes and complex geometries makes it indispensable for products requiring customized specifications. Whether for intricate automotive parts, durable aerospace components, or reliable electrical housings, zinc sand casting remains at the forefront of manufacturing excellence.
Selecting the right partner for zinc sand casting induces a collaborative approach to product development. Manufacturers often provide consultation services to assist from concept design through to finished product, ensuring expertise is embedded at every stage. This partnership not only yields superior components but also fosters innovation, where ideas transform into tangible, high-performance products.
In conclusion, zinc sand casting emerges as a cornerstone in contemporary manufacturing, bolstered by its expertise in delivering cost-effective, reliable, and finely crafted components. Its ability to balance between tradition and innovation while adhering to strict quality standards renders it a trusted choice across various industries. As technology and sustainability continue to evolve, zinc sand casting stands resilient, ready to meet future manufacturing challenges with its unique blend of experience and authority.