Precision casting, also known as investment casting, is a fascinating process that has been honed over centuries, offering unparalleled accuracy and finish for complex metal components. Among the various casting methods, several stand out as key precision casting processes, each with its unique traits and applications, ensuring that components meet stringent specifications required in numerous industries.
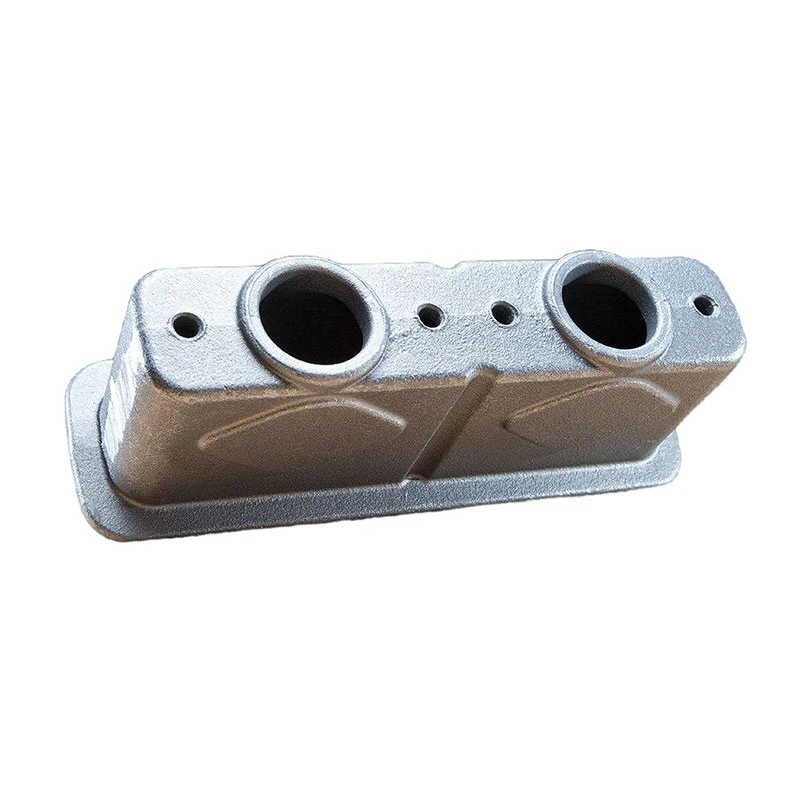
Investment casting, often considered the epitome of precision casting, involves creating a wax model of the desired end product. This wax model is dipped into a ceramic slurry to create a shell, which hardens to form a mold. Once the ceramic mold is robust, the wax is melted away, leaving a hollow cavity in the shape of the final product. This cavity is then filled with molten metal. Due to the meticulous process of mold creation, investment casting is capable of producing parts with extremely tight tolerances and intricate geometries. It is a preferred method for complex components used in aerospace, medical devices, and jewelry industries where detail and precision are paramount.
Die casting is another process that can qualify as precision casting. In this method, liquid metal is injected under high pressure into a steel mold. Die casting is renowned for its ability to produce large volumes of small to medium-sized parts with precise dimensions and fine surface textures. It is widely used in the automotive industry for manufacturing parts such as engine blocks, gearbox cases, and other components where dimensional perfection and smooth finish are critical.
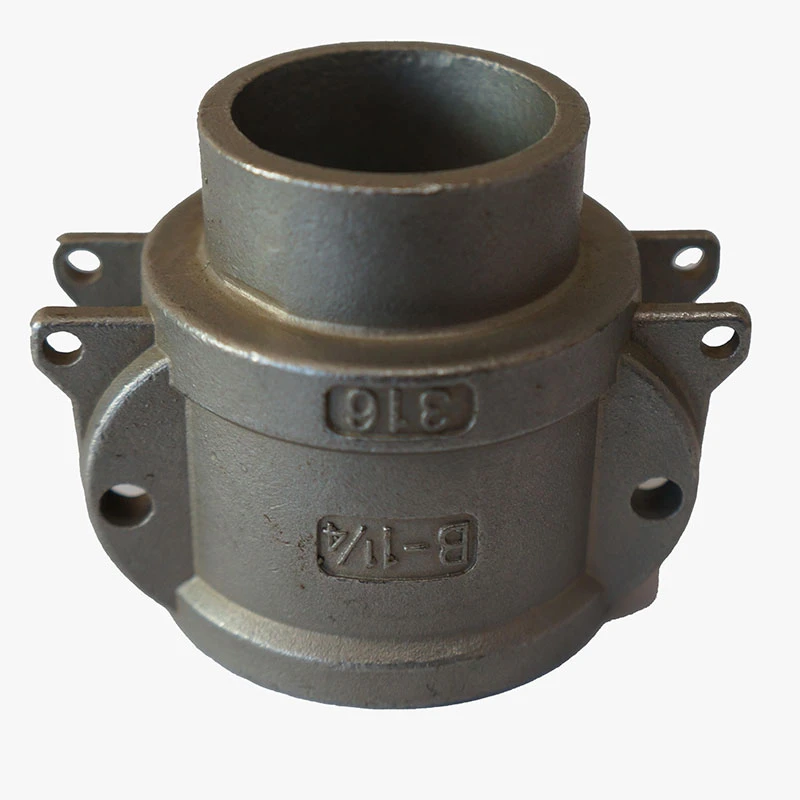
Centrifugal casting is also considered a precision method, particularly for cylindrical objects. This process involves pouring molten metal into a rotating mold. The centrifugal force distributes the metal evenly within the mold, creating a flawless, high-density product with no gas or shrinkage porosity. The remarkable precision and quality of centrifugal casting make it suitable for producing pipes, bushings, and other tubular components.
Continuous casting, while traditionally used for producing basic shapes like billets and bars, has evolved with technological advancements to offer precision casting capabilities. It is particularly precise in producing long, uniform shapes with excellent surface quality and internal consistency, crucial for industries requiring exacting standards, such as the construction and heavy machinery sectors.
which of the following qualifies as a precision casting process
Another noteworthy precision casting process is shell molding. This technique is particularly effective for high precision, high-volume applications. It involves creating a thin shell mold using a sand-resin mixture, which provides superior surface finish and dimensional accuracy. The process is advantageous for producing complex shapes that require detailed features, such as gear housings and intricate machine components.
These precision casting techniques are bolstered by recent advancements in technology, such as 3D printing and computer-aided design (CAD), which enhance the accuracy of wax models and casting patterns. Furthermore, quality control measures including X-ray inspection, coordinate measuring machines (CMM), and non-destructive testing ensure that precision cast parts consistently meet specified criteria for quality and performance.
Industry expertise shows that choosing the correct precision casting process hinges on the specific requirements of the end product, including volume, complexity, material compatibility, and mechanical properties. Moreover, the experience of professionals in the casting industry plays an imperative role in optimizing these processes to achieve maximum efficiency without compromising on quality.
In modern manufacturing, the integration of precision casting processes reaffirm the commitment to unparalleled product quality and performance consistency. As expert professionals continue to refine these methods, they set new benchmarks for precision and reliability, reinforcing the trustworthiness of precision casting as a cornerstone technology in the realm of advanced manufacturing.