Welding die-cast aluminum presents unique challenges that require a deep understanding and specialized techniques to ensure success. As a professional in the field of metal fabrication, navigating through these complexities not only demands expertise but also a strategic approach to maintain the integrity of the product. This article aims to provide an advanced insight into the process of welding die-cast aluminum, emphasizing the critical factors involved, expert practices, and proven methods to achieve optimal results.
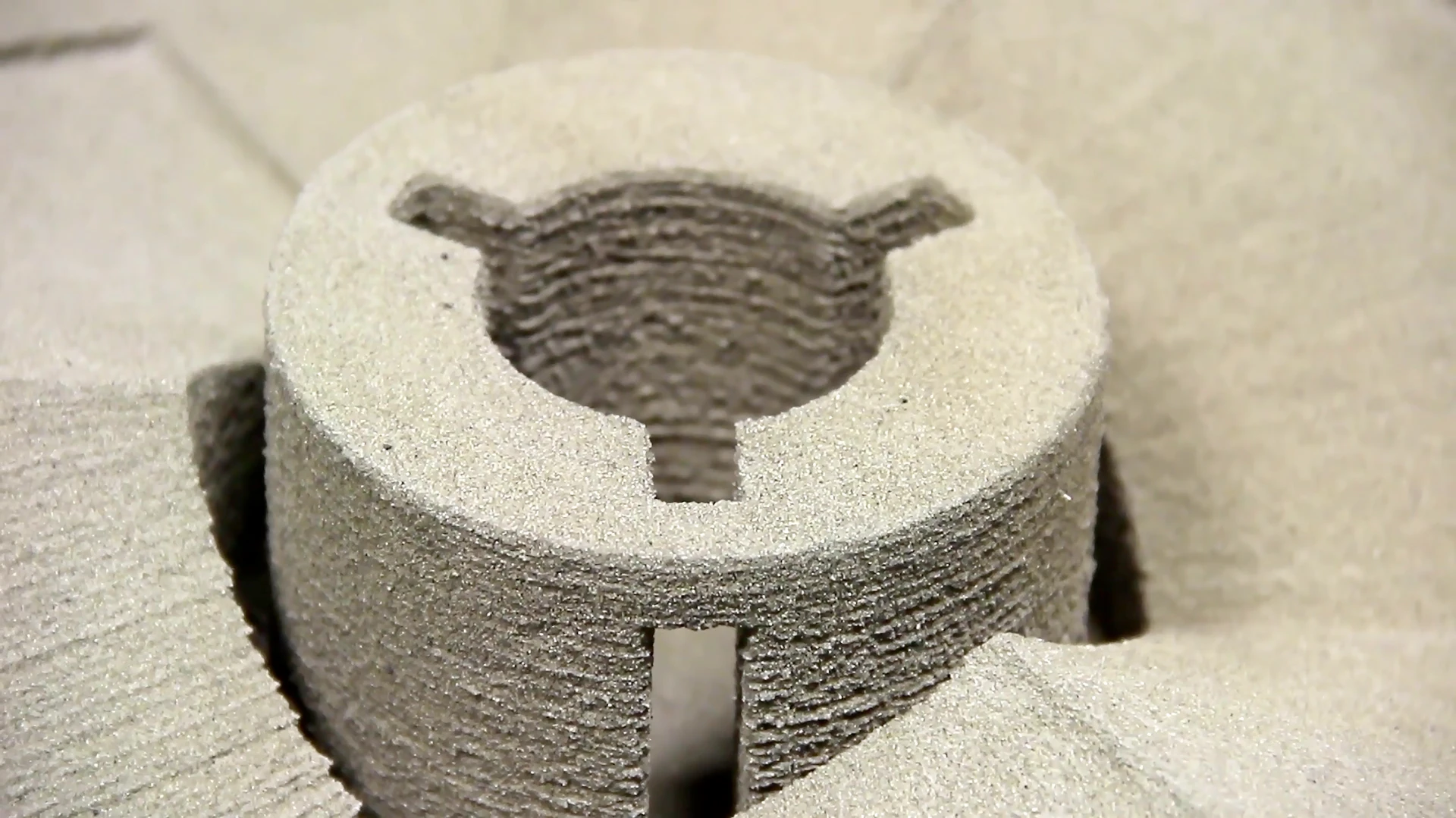
Die-cast aluminum is frequently favored in manufacturing due to its excellent strength-to-weight ratio, corrosion resistance, and ability to form complex shapes. However, welding this material is notoriously difficult, primarily due to its high thermal conductivity, low melting point, and the presence of impurities such as gas porosity. These factors can lead to defects like cracking, warping, and weak welds if not properly managed.
The first step towards successful welding of die cast aluminum involves selecting the appropriate welding process. Gas Tungsten Arc Welding (GTAW), also known as Tungsten Inert Gas (TIG) welding, is often regarded as the best choice. TIG welding provides greater control, precision, and cleaner welds which are critical for die-cast materials. Alternatively, Gas Metal Arc Welding (GMAW) or Metal Inert Gas (MIG) welding can also be used, but with adjustments to accommodate the intricacies of die-cast aluminum.
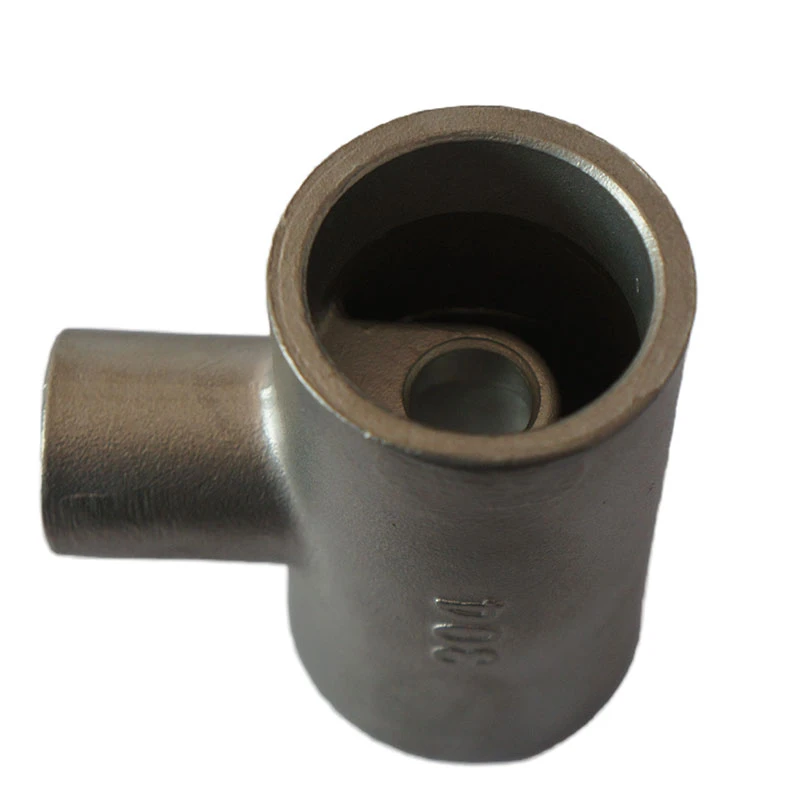
A fundamental aspect of welding die-cast aluminum is the preparation phase. Surface contamination is a common issue, as die-cast parts often contain oil, grease, or embedded oxides. Thorough cleaning with a wire brush or chemical cleaners, followed by proper drying, ensures a strong weld. Preheating the aluminum can also mitigate issues with cracking by reducing thermal stress during welding. The optimal preheat temperature generally lies between 300°F to 400°F.
When it comes to selecting filler material, it is crucial to consider both the alloys being welded and the desired properties of the weld. Filler alloys such as 4043 and 5356 are popular choices for aluminum due to their versatility and reliability. Each filler type brings specific advantages; for instance, 4043 offers better fluidity and reduced crack sensitivity, while 5356 provides higher strength.
welding die cast aluminum
Expertise in controlling heat input is paramount. Aluminum's high thermal conductivity can dissipate heat rapidly, causing difficulties in maintaining a stable weld pool and risking insufficient penetration. Adjustments in welding parameters, such as reducing welding speed and voltage whilst increasing current, can help address these issues.
Furthermore, employing advanced techniques such as pulse welding can significantly improve outcomes by minimizing heat input and providing better control of the weld pool. Pulse welding alternates between a high peak current, which improves penetration, and a low background current, which allows cooling, thus reducing the likelihood of overheating and distortion.
Monitoring and maintaining the inert gas shield, commonly using argon or a mixture of argon and helium, ensures that the weld pool is adequately protected from atmospheric contamination. A proper gas flow rate is critical; too low a rate may allow oxidation, while too high can cause turbulence and draw in contaminants.
Post-weld treatment is equally important for ensuring the longevity and quality of the weld. Techniques such as peening, annealing, or mechanical finishing can be used to relieve stresses and improve the mechanical properties of the weld zone.
In conclusion, while welding die-cast aluminum presents significant challenges, a detailed understanding and application of the correct processes and techniques can yield strong and reliable welds. Mastery of the nuances involved, from preparation to post-weld treatment, underscores the importance of expertise and continuous learning in this field. With advancements in technology and growing knowledge, future innovations are likely to further enhance the efficiency and effectiveness of welding die-cast aluminum, making it a less daunting task for welders worldwide.