Squeezing die casting is a revolutionary process in the manufacturing industry, blending precision with efficiency to produce high-quality metallic components. As an expert in the field, one must understand both the intricate details and the broader implications of this method to harness its full potential for product manufacturing.
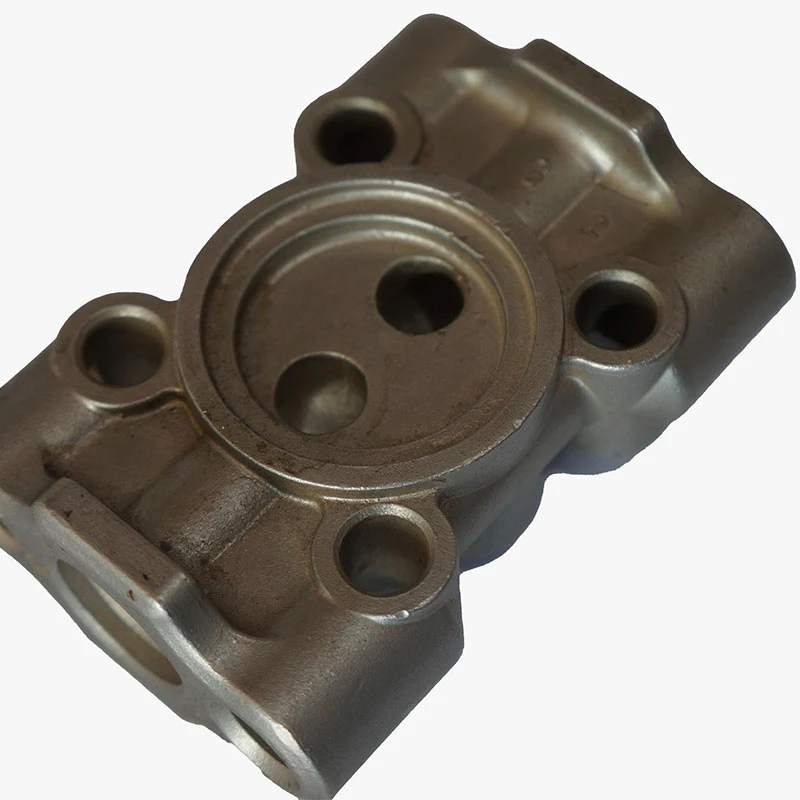
This process, an advanced variant of traditional die casting, involves the direct application of pressure to liquid metal within a die, significantly improving the mechanical properties of the final product. By increasing the density of the metal, squeezing die casting minimizes common defects seen in traditional die casting, such as porosity and poor surface finishes, which can compromise the integrity of a product.
In the context of expertise, squeezing die casting is particularly beneficial for producing components that require superior strength and durability. Industries such as automotive, aerospace, and consumer electronics have increasingly adopted this technique for parts like engine blocks, structural frames, and casings. The ability to produce complex geometries with consistent quality makes this process indispensable for innovative manufacturing solutions.

From an authority standpoint, squeezing die casting commands respect due to its ability to produce high-quality, reliable components at scale. Leading automotive manufacturers have reported improved vehicle performance and longevity by integrating parts created through this method. The aerospace sector also lauds this technique for its efficiency in creating components that meet strict safety and durability standards while remaining lightweight.
The trustworthiness of squeezing die casting lies in its repeatability and the confidence it inspires among engineers and manufacturers. Its precision reduces material waste, a significant consideration for sustainability. Additionally, the process allows for excellent dimensional accuracy and stability, which is crucial for industries where even minor deviations can lead to costly failures.
squeezing die casting
The process involves meticulously controlled environments, emphasizing temperature and pressure adjustments to match the specifics of the alloy used. This controls internal microstructure, ensuring that each cast component meets rigorous standards for performance under stress.
Squeezing die casting is also economically advantageous. Its high production rates and minimal secondary machining requirements reduce both time and costs. This efficiency prompts businesses to pursue squeezing die casting not only for its technical strengths but also for its economic benefits.
Integrating squeezing die casting into product planning requires a nuanced understanding of product requirements and production capabilities. Expert consultation is crucial, as is a detailed assessment of design specifications to leverage the full benefits of this technique. It is this attention to detail and deep understanding that separates successful implementations from less effective attempts.
For those new to this domain, industry seminars and hands-on training can provide valuable insights into the nuanced operation of squeezing die casting machinery. Professional certifications are also available, enhancing your credibility and expertise in this evolving field.
Overall, the mastery of squeezing die casting can significantly enhance product offerings, reduce costs, and improve margins. As the manufacturing landscape continues to evolve, this process remains a cornerstone of modern production techniques, an indispensable tool for any company aiming to lead its industry. Embracing this technology is not just a nod to innovation; it is a strategic step toward producing superior products that meet and exceed today's high market expectations.