Silica sand serves as a cornerstone in the casting process for foundries worldwide, owing to its extraordinary properties and reliability. With over two decades of experience working in the casting industry, I have witnessed firsthand the crucial role that high-quality silica sand plays in enhancing casting outcomes. This granular material has established itself as a vital component in creating precise, high-quality cast components from a variety of metals.
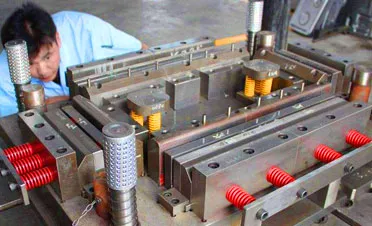
Silica sand, primarily composed of silicon dioxide (SiO2), is revered for its refractory characteristics and thermal stability. These properties enable it to withstand the high temperatures necessary for metal casting without deforming. During the casting process, silica sand forms a mold when combined with binding agents, providing the desired shape and surface finish for the metal being cast. In this role, its grain size and shape play an essential part; the rounder and more uniformly sized the grains, the better the resulting mold will be.
The prominence of silica sand is not just due to its physical properties but also its cost-effectiveness. Compared to synthetic or other refractory materials, silica sand offers significant savings, especially for large-scale operations where cost management is crucial. Moreover, its availability across various regions of the world makes it a sustainable option for many casting facilities.
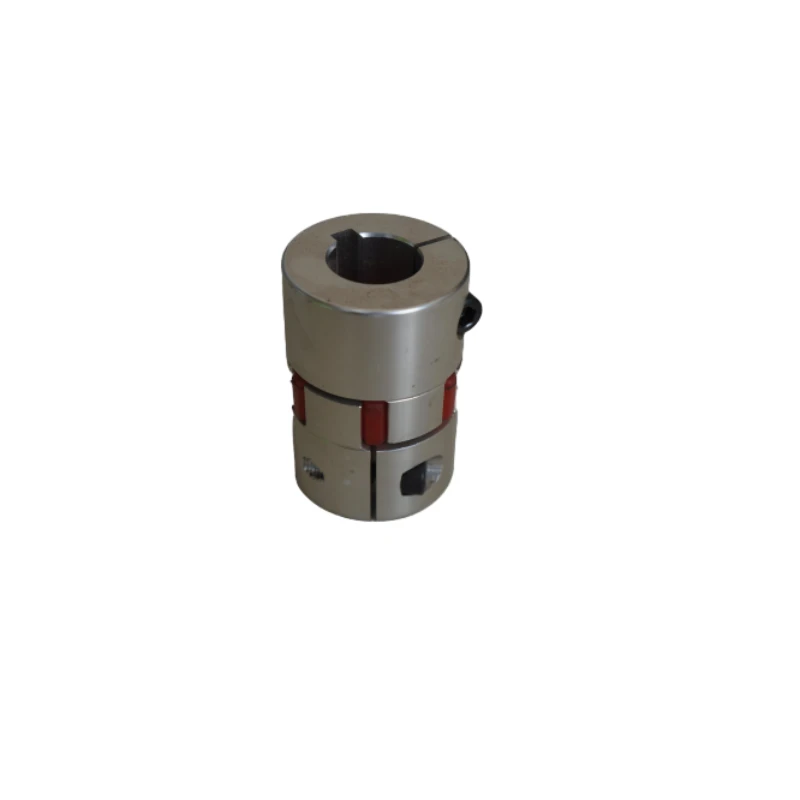
From a technical perspective, silica sand offers extraordinary permeability, which is key to reducing defects in casting. Permeability refers to the ability of the sand to allow gases to escape during the metal pouring and solidification processes. Proper escape of these gases prevents the formation of air pockets and other imperfections in the final cast product. In high-pressure casting environments, this aspect translates to a lower rejection rate and higher yield of quality castings.
Research has consistently reaffirmed the versatility of silica sand in various casting applications. Whether it’s for casting steel, iron, or even non-ferrous metals, silica sand adapts well to the shifting demands of different foundry processes. Advanced testing and quality control measures have further enhanced its usability in producing complex geometries and finely detailed components.
silica sand for casting
Expertise in selecting and using the right type of silica sand can considerably impact the efficiency of the casting operations. The key dimensions to consider are the grain fineness number (GFN), acid demand value (ADV), and moisture content, among others. Additionally, conditioning processes such as attrition, screening, and mixing with new sand can improve the sand's regenerative properties, expanding its utility for multiple cycles.
Silica sand’s trustworthiness as a casting material is well-established through years of consistent performance in the industry. Yet, continuous innovation in foundry technology propels improvements in silica sand processing and applications. For instance, advancements in resin-coated sand technology are enhancing the ability to produce cast components with intricate designs, without compromising the integrity or functionality.
Environmental considerations are increasingly influencing choices in sand sourcing and processing. Transitioning to environmentally friendly processes, such as adopting green sand casting methods, supports sustainable manufacturing while maintaining high-quality production standards. Proper waste management and recycling practices can substantially diminish the ecological footprint of casting operations involving silica sand.
The authoritative voice on silica sand in casting derives not just from historical data but from ongoing dialogues within the industry focused on innovation and quality assurance. Regulatory compliance, industry standards, and collaboration with research institutions continue to build upon the trusted reputation of silica sand as a paramount casting material.
In conclusion, silica sand’s robustness in casting applications is unmatched, a sentiment echoed by many industry veterans and foundry experts. Its economic advantages, coupled with reliable physical and chemical properties, make silica sand an indispensable element in the metal casting process. Investing in the right silica sand and maintaining rigorous quality standards can unlock greater efficiencies and more refined products in any casting operation.