Sand for metal casting is an indispensable material in the metalworking industry, significantly influencing the quality and efficiency of the casting process. Over the years, metal casting has evolved, and with it, so has the type and role of sand used. For manufacturers aiming to optimize their production, understanding the intricacies of casting sand is not only beneficial; it is necessary.
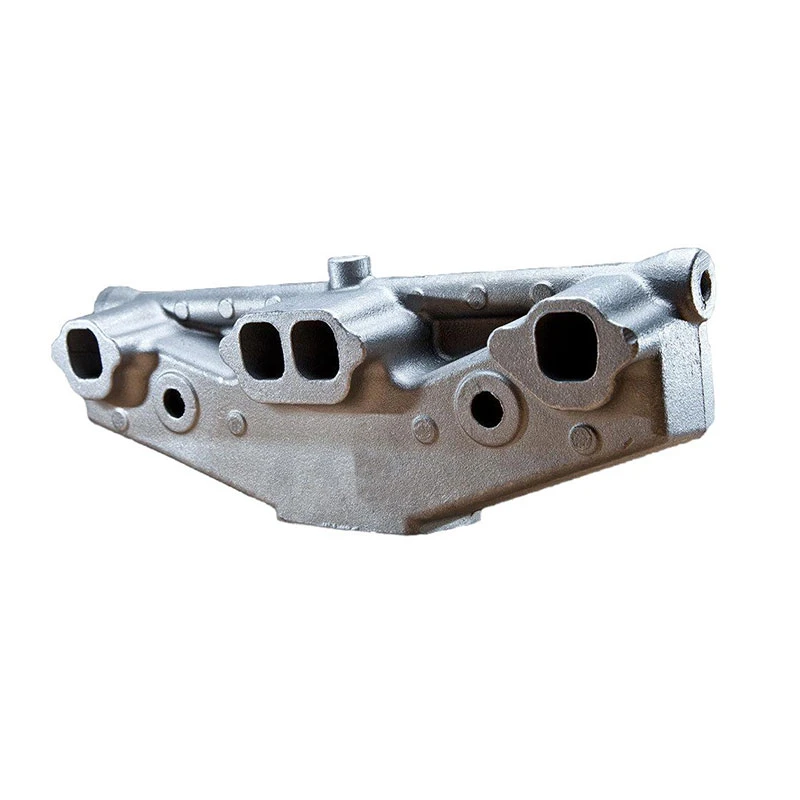
The core of metal casting sand often contains silica, primarily chosen for its high melting point, thermal expansion properties, and ability to bond with multiple resins. However, the choice is not limited to traditional silica sand. Industry experts have explored alternatives such as chromite sand, zircon sand, and olivine sand, each offering distinctive advantages based on the characteristics of the metal and the requirements of the casting process.
With silica sand, its affordability and wide availability make it a go-to option, especially for iron casting processes. On the other hand, alternatives like chromite sand bring the advantage of higher thermal conductivity, making them suitable for casting high-carbon steel to prevent surface defects. Zircon sand, albeit expensive, is ideal for precision casting due to its high fluidity and low reactivity, ensuring an impeccably smooth metal finish.

The selection process of casting sand is critical. It involves evaluating factors like grain size, shape, and distribution, influencing the sand’s permeability and, consequently, the casting's surface finish. Fine-grained sand can produce exceptional smoothness in small castings but may lead to gas retention and casting defects in larger molds. Balancing these characteristics is a nuanced task, requiring not just experience but also scientific understanding.
Industries now widely introduce bentonite clay to enhance sand's binding properties, giving it the necessary green strength. However, the right choice of additives, including coal dust, dextrin, or cornflour, can result in a favorable balance of moisture and strength, reducing casting defects.
sand for metal casting
Reusability and environmental safety of casting sand have become significant considerations. The shutdown of foundries due to non-compliance with environmental standards highlights the importance of sand reclamation processes. Effective practices involve mechanical or thermal reclamation to reuse sand, reducing waste and lowering costs. Maintaining control over sand contamination and optimizing reclamation equip industries with a dual advantage of sustainability and profitability.
The successful application of sand for metal casting is largely dependent on monitoring and control. Implementing advanced diagnostic tools to measure grain size distribution, moisture content, and sand strength can preemptively address issues that arise during casting. Real-time data analytics provide invaluable insights, enabling proactive modifications in the sand preparation process, ensuring consistency in casting quality.
Moreover, the experience of professionals who have a deep understanding of metallurgy contributes to the quality control and refinement of sand casting processes. These experts can identify subtle discrepancies in casting finishes and troubleshoot them, embodying the experience-driven knowledge that elevates the entire production process.
In conclusion, casting sand, much more than just a medium, is a science and an art combined. Its role is accentuated through tailored selection, effective reclamation, and precise monitoring. Companies that invest with an expertise-driven approach—harnessing experience and technology—ultimately enhance their casting operations' efficiency and environmental sustainability, establishing themselves as leaders in the competitive sphere of metal manufacturing. By doing so, they not only uphold industry standards but set them, leveraging their authority and trustworthiness as benchmarks of quality and innovation in metal casting.