In the dynamic world of die casting, the term plunger sleeve die casting holds a crucial place. Professionals working in manufacturing industries recognize the importance of precision and quality in the creation of countless metal products. This process involves intricate techniques requiring expertise, authoritative knowledge, and trust in materials and methods. Understanding the complexities of plunger sleeve die casting can position a business for success and innovation.
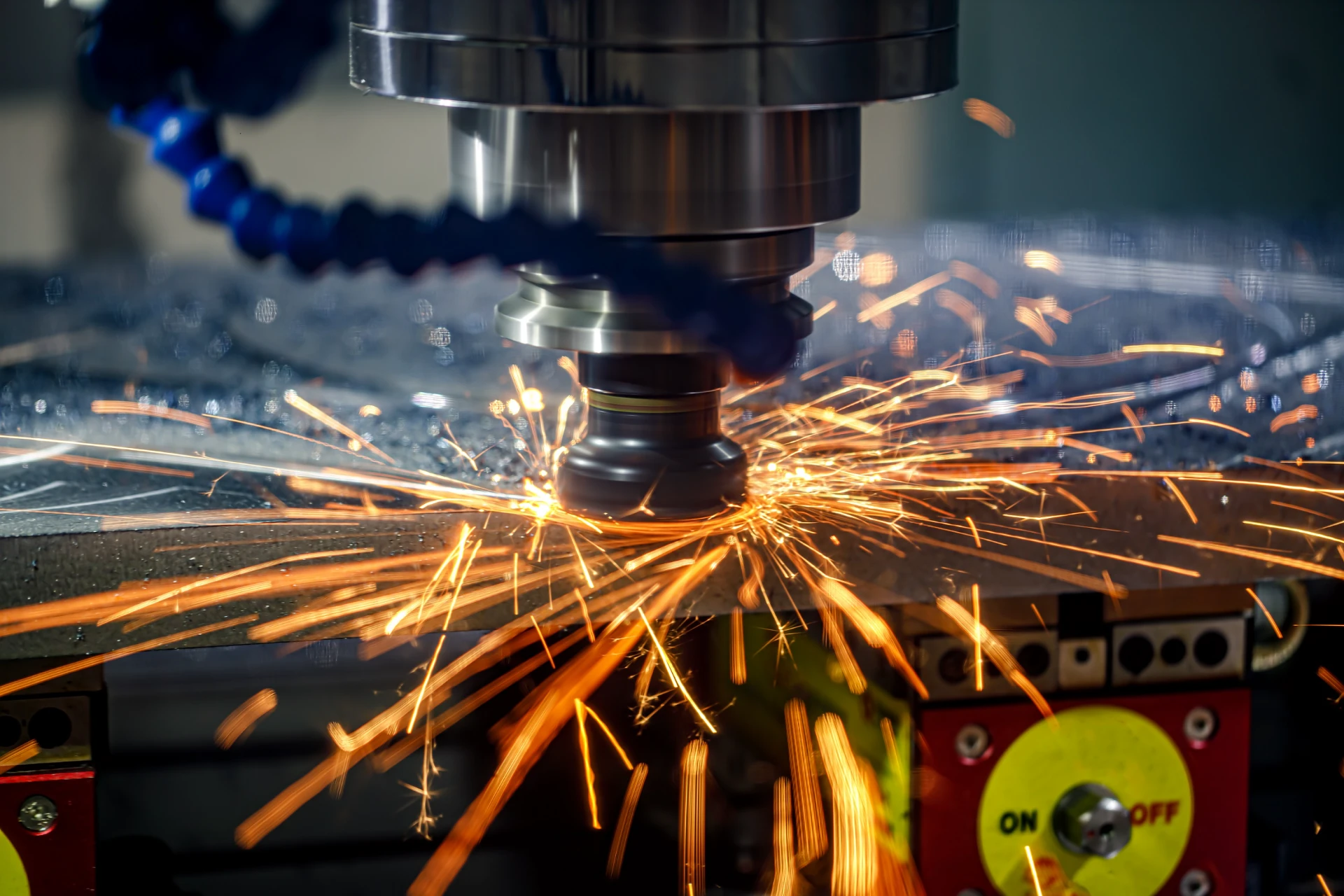
Die casting is a repetitive manufacturing process that involves forcing molten metal into a mold cavity. It is widely used for producing metal parts with intricate geometries quickly and with exceptional accuracy. A plunger sleeve is an essential component in this process, serving as a conduit to guide the molten metal into the die cavity. The plunger sleeve's primary function is to provide a smooth, uniform flow of metal, prevent leakage, and ensure the longevity of the die.
Expertise in selecting the right plunger sleeve material is crucial. Traditionally, materials such as tool steels and cast iron have been used due to their remarkable resilience to heat and wear. However, advancements in materials science have introduced superior alternatives like advanced composites and ceramic coatings, offering enhanced durability and thermal management. Engineers must consider several factors, including thermal conductivity, wear resistance, and the coefficient of thermal expansion, to optimize the plunger sleeve's efficiency and durability.
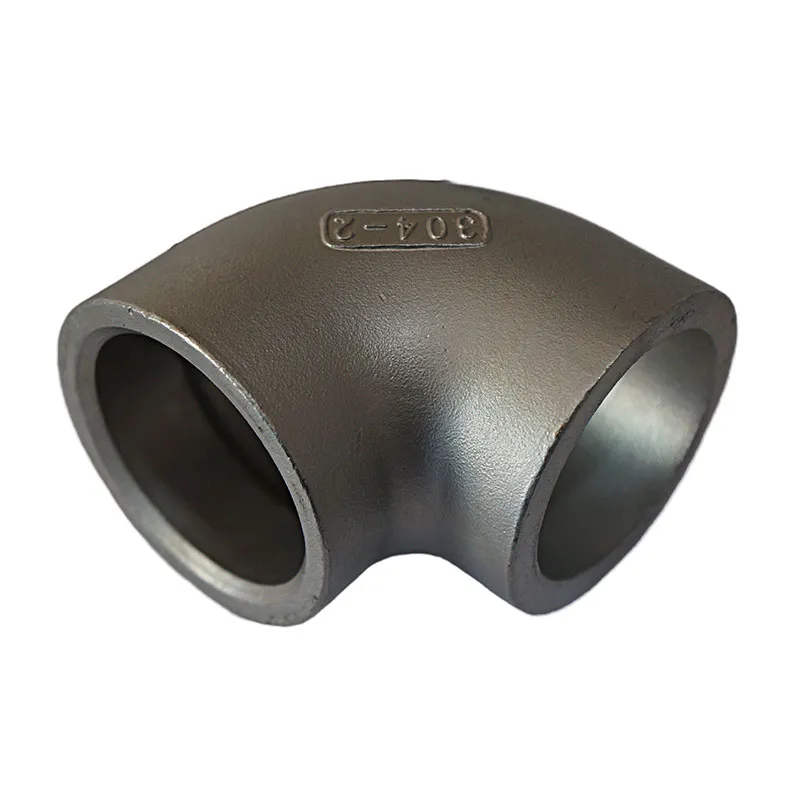
Strategically, correct sizing and alignment of the plunger sleeve are paramount. Misalignment or incorrect sizing can lead to defects in the casting, such as cold shuts or misruns. These defects not only diminish the product's mechanical integrity but also increase the likelihood of rejections and remanufacturing costs. Experienced die casting professionals ensure meticulous attention to these parameters, using simulations and precise measurements to align the plunger sleeve perfectly with the die.
Authoritativeness in die casting comes from a deep understanding of the forces at play during the plunger sleeve's operation. The plunger experiences immense pressure as it drives molten metal. Hence, even minor deviations or defects in the sleeve can lead to catastrophic failures. Manufacturers who adhere to strict quality control procedures and employ state-of-the-art inspection methods, such as X-ray and ultrasonic testing, demonstrate authoritative command over the production process.
plunger sleeve die casting
Innovations in plunger sleeve die casting have also introduced automation and digital twins, bolstering efficiency and repeatability. Automation reduces human error, boosts productivity, and ensures consistent quality. Meanwhile, digital twin technology allows virtual modeling of the entire die casting process. This facilitates real-time adjustments, prediction of potential issues, and preventative maintenance scheduling.
The trustworthiness of a manufacturing process lies in its ability to continuously deliver quality results while adapting to new challenges and demands. In the realm of plunger sleeve die casting, trust is earned through a commitment to precision, quality assurance protocols, and ongoing research and development. Manufacturers often collaborate with academic institutions and research organizations to stay abreast of the latest technologies and methodologies.
From a product lifecycle perspective, understanding the maintenance and replacement intervals of plunger sleeves is key to maintaining optimal die casting operations. Regular inspections are necessary to detect hairline fractures, surface fatigue, or any abnormalities. Predictive maintenance leveraging IoT sensors and AI analytics is transforming how manufacturers forecast the lifespan of their components, minimizing downtime and extending the sleeves’ operational longevity.
In conclusion, mastering plunger sleeve die casting requires a blend of experience, expertise, authoritative process control, and trust in technological advancements. By focusing on these elements, companies can innovate with confidence, reduce waste, and produce high-quality metal parts demanded by diverse industries globally. As technology evolves, so too will the capabilities and efficiency of die casting processes, paving the way for unprecedented advancements in manufacturing.