Aluminium casting is a crucial process across various industries, offering a balance between weight, strength, and corrosion resistance. However, the challenge of porosity in aluminium casting can significantly affect the quality and performance of the final product. Porosity refers to the presence of small voids or holes within the metal, which can compromise the material's integrity, leading to potential failure in critical applications. Understanding and adhering to aluminium casting porosity standards is essential for anyone involved in the manufacture or procurement of aluminium parts.
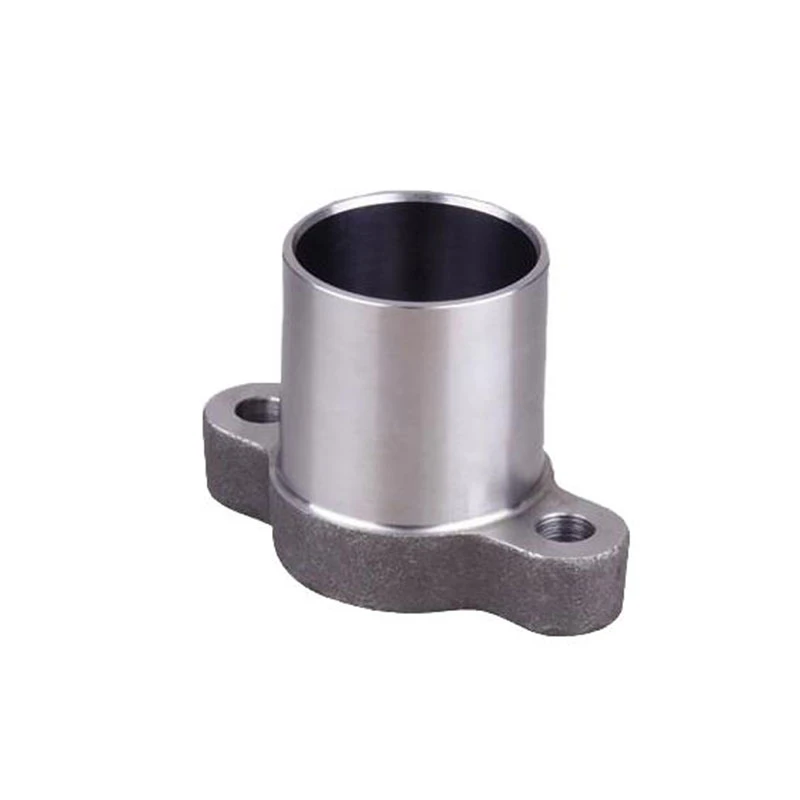
Porosity in aluminium casting typically arises from trapped gas, shrinkage, or ineffective feeding systems during the solidification of the metal. Experts have developed several standards that aim to classify and limit porosity to acceptable levels, ensuring the durability and reliability of the cast parts. These standards help in benchmarking quality, facilitating global trade, and enhancing customer trust.
The American Society for Testing and Materials (ASTM) is a prominent body that has established guidelines for controlling porosity in metals. ASTM standards provide a comprehensive framework for evaluating the density and integrity of cast aluminium. One such standard, ASTM E505, offers a visual reference for classifying porosity in metals, enabling accurate assessment and comparison. By leveraging such standards, engineers can ensure that their products meet rigorous quality specifications and perform reliably in demanding conditions.
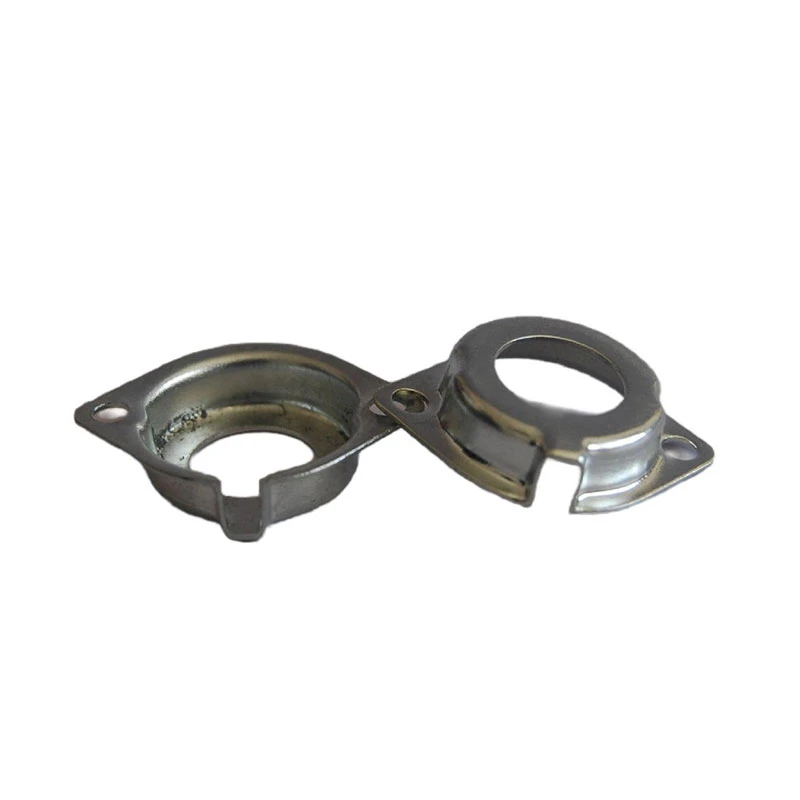
Implementing porosity standards involves cutting-edge technological solutions. Advanced non-destructive testing (NDT) methods such as X-ray and computed tomography (CT) scans allow for precise detection of porosity without damaging the part. These technologies help manufacturers verify the integrity of their products in line with established standards, preventing potential failures that could lead to costly recalls or safety hazards.
Manufacturers need to adopt best practices from the outset to minimize porosity. This includes optimizing the casting design, improving mold materials and coatings, and regulating the metal's temperature and pressure during the casting process. In industries like automotive and aerospace, where the structural integrity of parts directly impacts safety and performance, adherence to porosity standards becomes even more critical. Manufacturers often document their processes and quality assurance measures to provide transparency and build trust with their clients.
aluminium casting porosity standard
Continuous professional development and training are vital for any team working within aluminium casting. By staying informed on the latest research, technologies, and standards, professionals can ensure that their casting processes remain at the forefront of the industry. Collaborating with standard organizations, participating in industry forums, and engaging with academic institutions for research initiatives further bolster an organization's commitment to excellence in product quality.
Moreover, building robust relationships with suppliers is paramount. Suppliers of raw materials and equipment need to understand the standards and expectations surrounding porosity in aluminium casting thoroughly. By cultivating partnerships based on quality and reliability, manufacturers can significantly mitigate the risks associated with porosity.
Certified quality management systems such as ISO 9001 incorporate guidelines for process control and monitoring that align closely with maintaining porosity standards. Certification not only reflects a manufacturer's commitment to quality but also enhances their credibility in the eyes of potential customers and partners.
In conclusion, maintaining stringent aluminium casting porosity standards is not merely a regulatory requirement but a crucial component of delivering high-performance, reliable products. Through the commitment to quality, continuous improvement, and strategic partnerships, businesses can overcome porosity challenges, setting a new benchmark in product excellence.