Miniature metal stamping has emerged as a precise and reliable solution for various industries requiring compact components. This advanced manufacturing technique involves the process of converting flat metal sheets into specific shapes by using a dedicated die and a pressing machine. With its growing significance, understanding the nuances of this technology provides valuable insights into its applications, benefits, and evolving innovations.
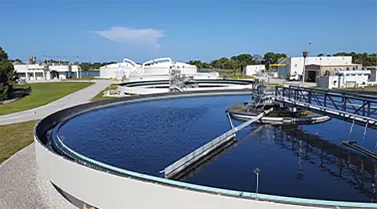
One of the primary reasons miniature metal stamping has gained attention is its unmatched precision. Industries such as electronics, automotive, aerospace, and medical devices rely heavily on components that need to meet exact specifications. The precision offered by miniature metal stamping ensures that each piece matches the intended design, thereby minimizing errors and enhancing functional reliability. For instance, in the electronics industry, producing small, intricate components like connectors and sensors with consistency is crucial for the assembly of circuits, where even minor deviations can lead to significant failures.
Expertise in miniature metal stamping is characterized by a deep understanding of the materials and processes involved. Engineers and technicians specializing in this area must choose the appropriate metal types and gauge levels, taking into consideration the mechanical properties required for the final product. Materials such as copper, stainless steel, aluminum, and various alloys are commonly used. Each material possesses unique characteristics, such as conductivity, corrosion resistance, and malleability, impacting their performance in different applications. By leveraging knowledge of metallurgical properties, professionals can optimize the stamping process, enhancing the durability and performance of the components produced.

The authoritative nature of miniature metal stamping lies in its contribution to innovative design and rapid prototyping. As product lifecycles shorten, manufacturers face constant pressure to innovate swiftly and cost-effectively. Miniature stamping addresses this by allowing for quick adjustments in design without extensive overhauls in the production process. This is particularly beneficial in prototyping phases where multiple iterations and tests are needed before finalizing a design. As a result, industries can accelerate their product development timelines, bringing new innovations to market faster than before.
miniature metal stamping
Companies renowned for their expertise in metal stamping often pride themselves on the trustworthiness of their processes and results. Trust in this context is built through rigorous quality control measures and adherence to industry standards. Advanced inspection technologies, such as automated visual systems and coordinate measuring machines (CMM), are employed to ensure precision and consistency across batches. This rigorous check against quality standards not only assures customers of product reliability but also strengthens the reputation of manufacturers as leaders in precision component manufacturing.
Furthermore,
sustainability is increasingly becoming a pivotal aspect of the metal stamping sector. Conscious efforts to minimize waste in the stamping process align with industry moves towards sustainability. Implementing closed-loop systems for metal shavings and scrap recycling is one approach to reducing environmental impact. Moreover, as industries adopt greener practices, there is a growing demand for components manufactured from recycled materials, integrating sustainability with innovation.
The future of miniature metal stamping holds significant potential with the integration of smart manufacturing techniques. Incorporating IoT and AI into the stamping process allows for real-time monitoring and adjustments, enhancing efficiency and reducing downtime. Predictive maintenance enabled by machine learning can foresee equipment malfunctions before they occur, allowing for proactive measures, minimizing disruptions, and ensuring a seamless production cycle.
In conclusion, miniature metal stamping stands as a cornerstone of modern manufacturing with its precision, reliability, and adaptability. Its role in fostering innovation, aligning with sustainability goals, and incorporating next-gen technologies underscores its importance across industries. As the demand for smaller, more efficient components continues to grow, those with expertise in this area will be pivotal in shaping the future of manufacturing technology.