In the vast realm of metalworking, sand casting stands as one of the most fundamental techniques employed for producing intricate metal components. Yet, there's an advanced subcategory within this technique that has gained significant traction due to its robust applications hard sand casting.
This advanced method elevates traditional sand casting, offering a myriad of benefits that cater to industries demanding precision and durability.
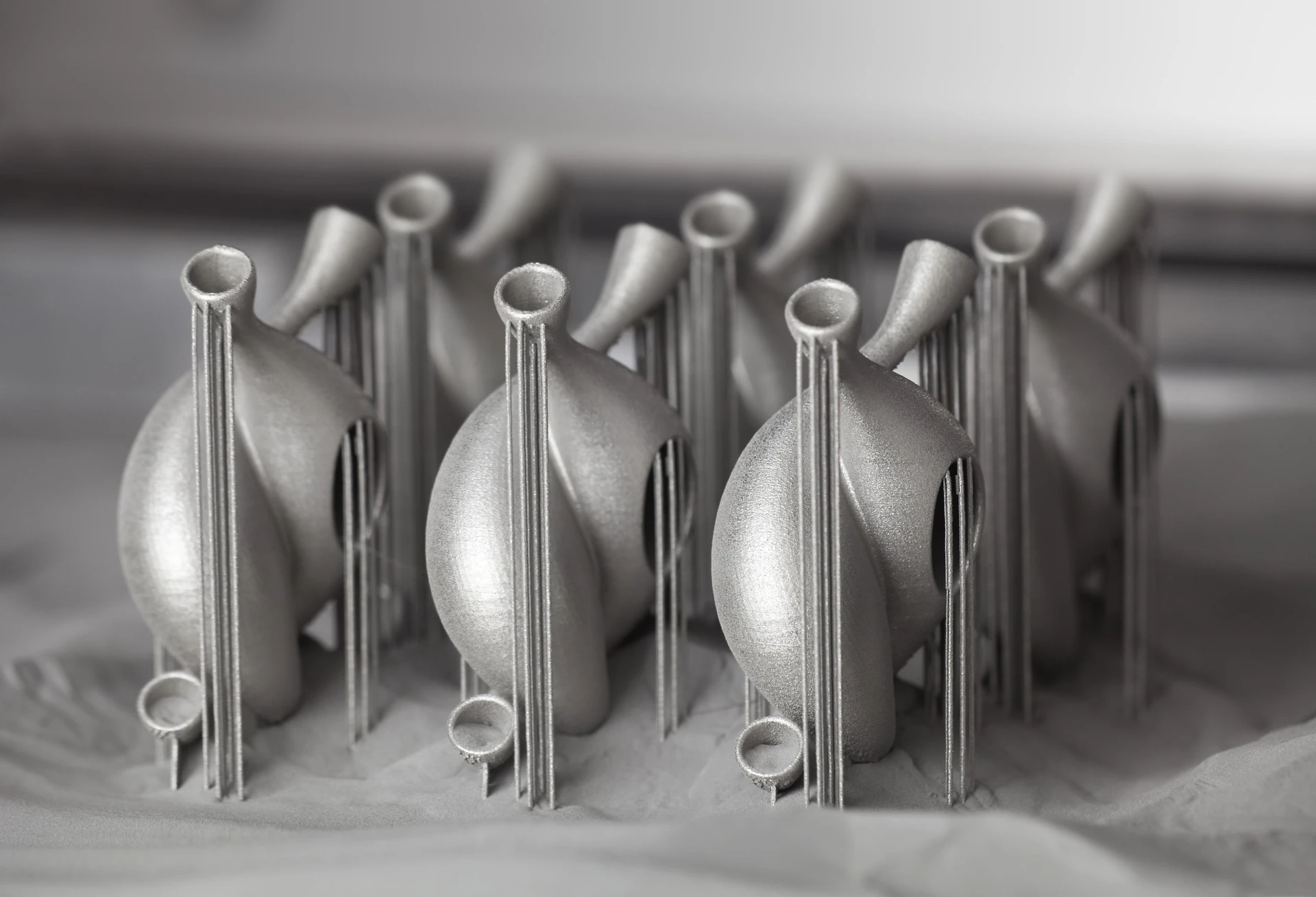
Hard sand casting is not just about pouring molten metal into sand molds; it involves the utilization of specially formulated sand mixes that ensure enhanced mold stability and superior surface finish. The process begins with selecting high-strength sand mixes combined with chemical binders, creating molds that can withstand higher pressures and temperatures than conventional sand molds. This unique approach is particularly advantageous for producing large-scale metal components that require tight tolerances and a high degree of accuracy.
One of the primary reasons hard sand casting has become a preferred choice in the industrial sector is its ability to produce metal parts with exceptional surface finish and dimensional accuracy. Unlike traditional sand casting, where surface irregularities and porosity might pose challenges, hard sand casting minimizes these defects, reducing the need for post-casting machining and finishing. This efficiency not only saves time but also cuts down on manufacturing costs, making it an economically viable option for large-scale production runs.
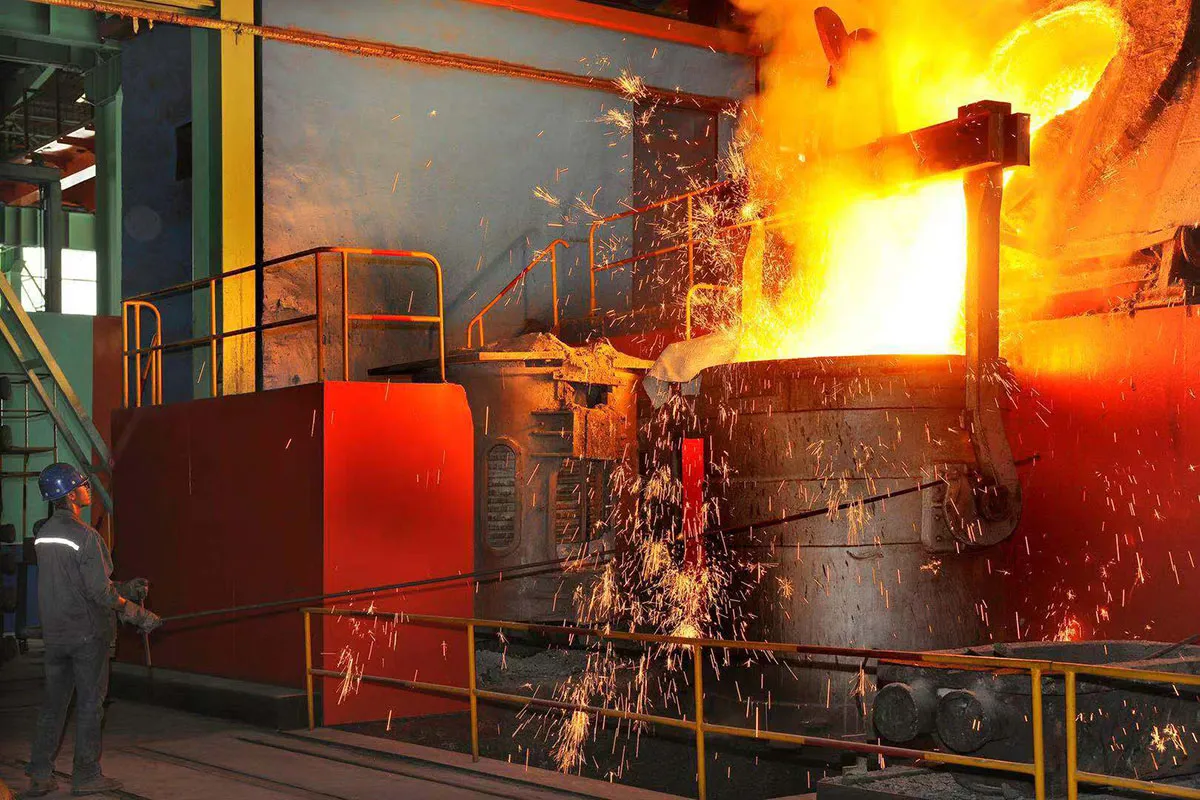
Industries such as automotive, aerospace, and heavy machinery have benefitted immensely from the adoption of hard sand casting. The automotive industry, for instance, leverages this process to cast alloy engine blocks and transmission cases that must endure extreme environments while performing flawlessly. Similarly, aerospace manufacturers utilize hard sand casting to create complex components that meet stringent safety and performance standards.
Professional expertise is paramount in achieving the high-quality results that hard sand casting promises. With years of experience, casting specialists develop the necessary skills to choose the right sand blend, achieve precise mold assembly, and control the casting parameters meticulously. This expertise ensures that each step of the process is executed flawlessly, resulting in products that meet specified requirements without compromise.
hard sand casting
A testament to hard sand casting's authoritativeness is its compliance with internationally recognized standards, showcasing its reliability and trustworthiness. Facilities specializing in hard sand casting often undergo rigorous audits and certifications, ensuring their processes align with global industry benchmarks. This adherence to quality standards positions hard sand casting as a trusted method for producing critical components in demanding applications.
Moreover, ongoing advancements in sand casting technology have further cemented hard sand casting's position as an authoritative approach to component manufacturing. Innovations in sand binder chemistries and automated molding systems continue to enhance the process, improving its efficiency, sustainability, and quality. As these technologies evolve, so too does hard sand casting's capacity to address an even broader range of industrial challenges.
For businesses considering hard sand casting as a solution, it's important to partner with a foundry that not only understands the nuances of the method but also prioritizes quality and consistency. Trustworthy foundries will provide detailed insights into the casting process, from material selection to quality assurance protocols, ensuring clients receive components that meet or exceed their expectations.
In summary, hard sand casting offers a robust solution for industries requiring precision-cast metal components. Its enhanced mold stability, superior surface finish, and compliance with international standards make it a preferable choice for manufacturing needs that demand accuracy and durability. By leveraging the expertise of seasoned professionals and embracing technological advancements, organizations can reap the benefits of this authoritative casting technique, producing components that are both cost-effective and high-performing.