Hard anodizing die-cast aluminum is an advanced finishing process that significantly extends the durability and performance of aluminum components. With decades of experience in the field, manufacturers have constantly refined the technique to ensure that it meets the rigorous demands of industries ranging from aerospace to consumer electronics. This process transforms the surface of aluminum through electrochemical means, creating a thick, highly resistant oxide layer.
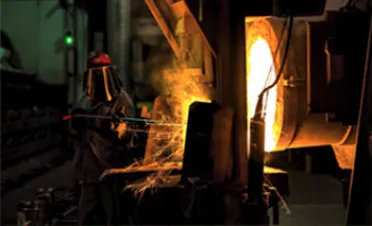
The hard anodizing process for die-cast aluminum stands out due to its ability to enhance both wear and corrosion resistance. Traditional anodizing methods provide a moderate level of surface improvement, but hard anodizing goes a step further. By utilizing a meticulously controlled electrolytic bath, often at low temperatures, manufacturers achieve a dense, wear-resistant coating that can withstand harsh environments. This is particularly advantageous for components exposed to abrasive conditions, where longevity and reliability are critical.
In real-world applications, hard anodized die-cast aluminum components are witnessing increased demand due to their superior performance attributes. For instance, in the automotive industry, manufacturers rely on these components for parts that require both lightweight properties and high strength, such as engine parts and transmission systems. The enhanced hardness offers a significant reduction in friction, which translates into improved fuel efficiency and reduced wear and tear, ultimately minimizing maintenance costs.
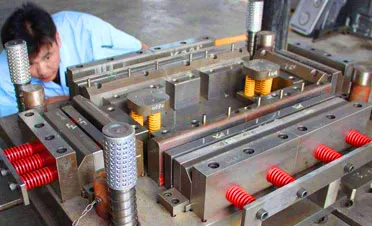
The process also shines in electronics, where it protects enclosures and housings from environmental factors such as moisture and chemicals. The hard anodized coating serves as a barrier, safeguarding sensitive electronic components from the outside world. This protective nature makes such components ideal for use in outdoor or industrial settings where environmental factors could otherwise jeopardize performance and safety.
Expertise in this domain highlights the delicate balance required during the hard anodizing of die-cast aluminum. Unlike other substrates, die-cast aluminum presents unique challenges due to its inherent composition and potential for casting defects. Professionals in this field have developed and implemented stringent quality control measures to address these challenges. By carefully monitoring the chemical composition of the alloy used, and optimizing the parameters of the anodizing process, such as current density and bath composition, experts ensure a uniform and flaw-free finish.
hard anodizing die cast aluminum
Through comprehensive research and development, manufacturers have solidified their authority in hard anodizing techniques. Publications in leading scientific journals and presentations at international industry conferences further cement their status as pioneers and innovators in this realm. Their commitment to continuous improvement is evident in the exhaustive testing protocols that assess factors such as coating thickness, microhardness, and adhesion strength.
Trustworthiness is paramount in the hard anodizing industry. Clients need to have absolute confidence that the components will perform reliably overtime. To build this trust, manufacturers invest in certification and accreditation programs that align with international standards such as ISO 9001 and Nadcap. These certifications serve as a testament to the rigorous quality management systems in place, ensuring that every piece of die-cast aluminum receives the same precision treatment.
Feedback from industries that incorporate hard anodized die-cast aluminum components is overwhelmingly positive. For example, aerospace companies have reported reduced maintenance cycles and increased performance reliability, leading to enhanced operational efficiency. Moreover, these components have demonstrated exceptional resilience in extreme conditions, maintaining their integrity and function where others might fail.
In conclusion, hard anodizing die-cast aluminum is more than just a finishing process; it is a critical enhancement that maximizes the potential of aluminum components. The process's evolution, supported by extensive experience and expertise, reinforces its authority as a top-tier solution for demanding applications. With proven trustworthiness, it continues to inspire confidence across multiple industries, becoming an essential tool for designers and engineers striving for excellence in their products.