Dry sand casting stands as a cornerstone process in the arena of metal casting, known for its versatility and cost-effectiveness. This method, an art form in its right, is where technical acumen meets practical innovation. By enveloping molten metal within molds formed from sand, dry sand casting has been essential for creating intricate parts efficiently. The expertise needed in handling this method not only necessitates understanding the mechanical principles but also demands an intimate knowledge of the materials involved.
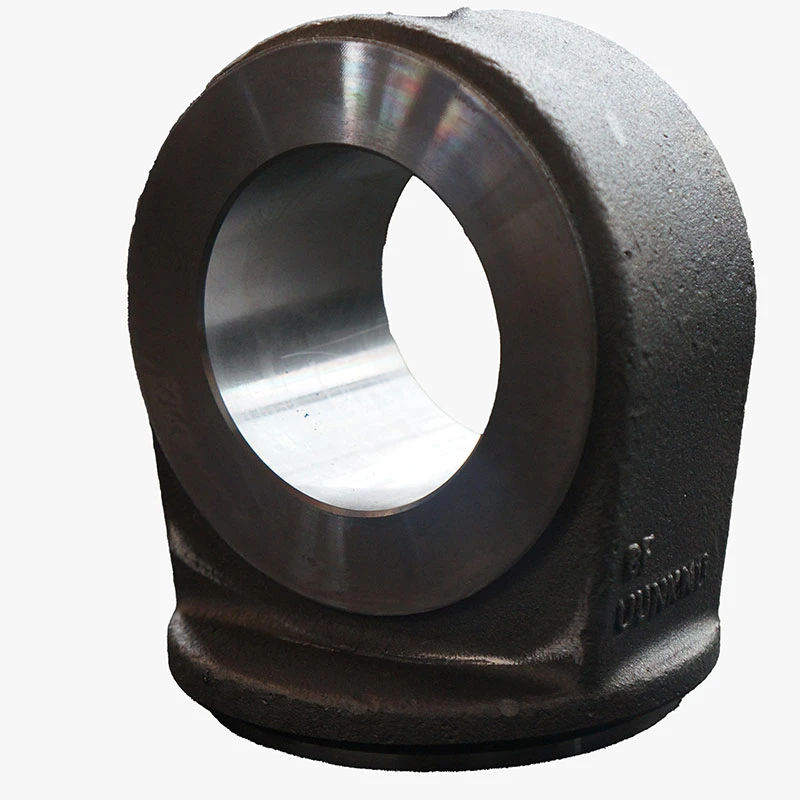
At its core, dry sand casting differs from other casting methods by the use of dry sand molds, which offer improved dimensional accuracy and superior surface finish.
The meticulous preparation of the sand mixture is pivotal. The sand must be capable of withstanding the intense heat of molten metal, while also maintaining its shape and allowing gases to escape efficiently. Achieving the ideal balance of clay, sand, and water is critical, requiring expertise honed from experience and rigorous testing.
Professionals in the industry appreciate the reliability that dry sand casting offers. The process begins with creating a pattern that reflects the shape of the desired part. This pattern is immersed in a sand mold mixture, where it becomes the foundation upon which the final product will be cast. Once the mold is prepared and dried, it becomes the cavity to which molten metal is introduced. The precision of pattern-making is paramount, as any discrepancies can lead to defects in the formed part. Thus, casting experts continually emphasize the significance of precision and attention to detail, guided by years of accumulated experience.
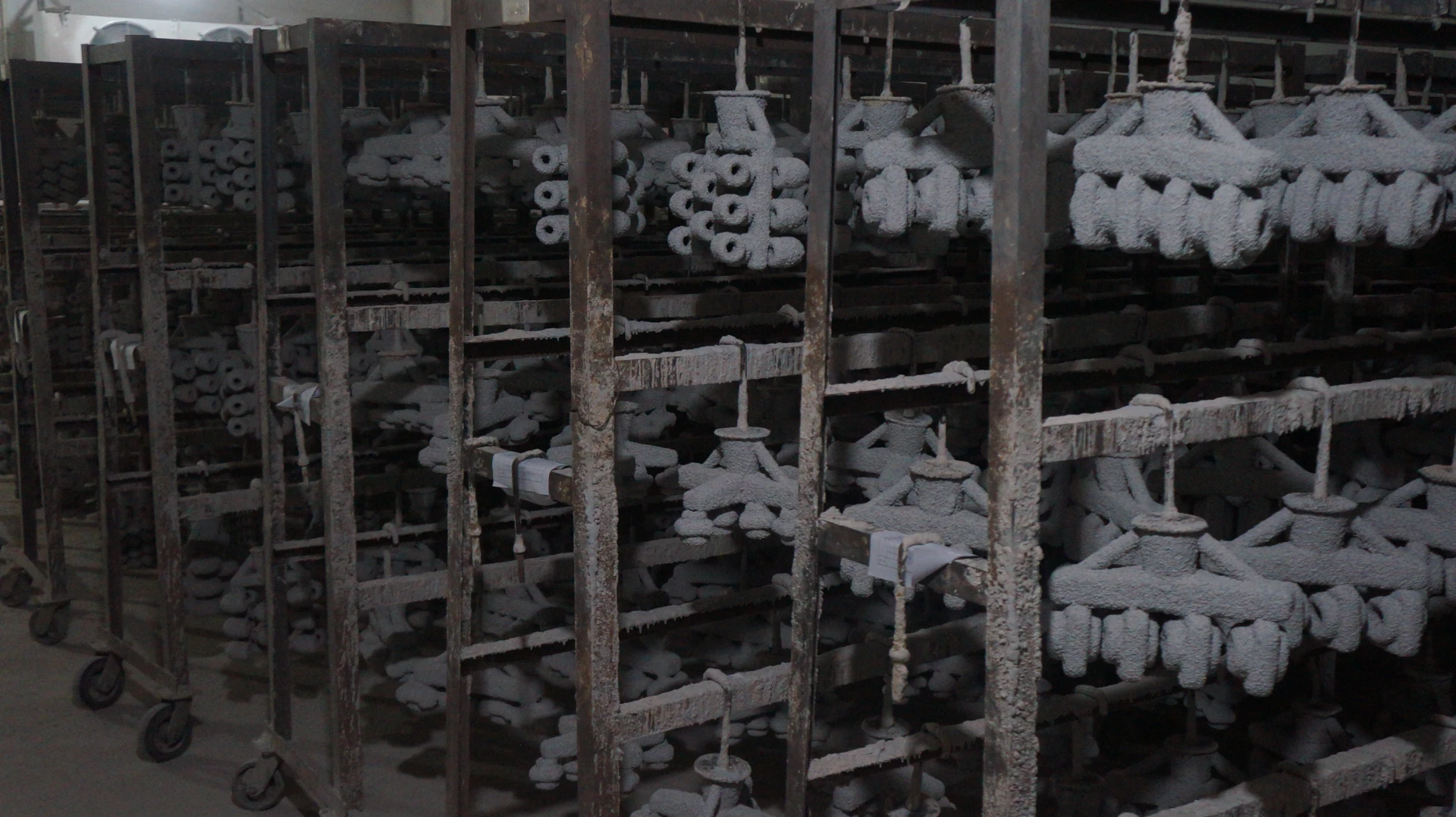
Another aspect distinguishing dry sand casting is its adaptability in producing large castings that other methods struggle with due to weight constraints or material limitations. As such, industries spanning from automotive to aerospace heavily rely on this method. Their trust in dry sand casting stems from a chronicled history of successful implementations, showcasing both the expertise and authority that industry leaders have cultivated over time.
dry sand casting
The environmental implications of dry sand casting are increasingly becoming a focal point. The method inherently allows for sustainable practices by virtue of its materials. Sand, being a naturally abundant material, can often be recycled and reused multiple times across casting lifecycle stages, thereby reducing waste. Modern advancements are directing focus towards enhancing the mold quality to further reduce environmental footprint, aligning with contemporary sustainability goals.
In today's competitive market, the demand for quality and trustworthiness in manufacturing cannot be understated. Dry sand casting professionals hold a reputable stance because their methodologies consistently yield products that meet stringent standards. Customers and stakeholders alike depend on the proven reliability that comes with this process, which is supported by industry certifications and quality controls that enshrine trust.
Mastery in dry sand casting is not achieved overnight but through persistent dedication and advanced technological integration. As we continue to harness more advanced modeling software and simulation techniques, the boundaries of what dry sand casting can achieve continue to expand. It is through this intersection of expertise, experience, and innovative spirit that dry sand casting maintains its authoritative position in the manufacturing landscape.
For those aiming to delve into or refine their approach within this field, it is prudent to seek insights from seasoned professionals, adopt best practices, and stay abreast of emerging technologies. These elements together form the foundation of a successful dry sand casting operation, securing its role as an indispensable process in manufacturing's future.