Selecting an effective die casting cooling system can significantly impact the quality and efficiency of the die casting process, playing a pivotal role in forming and cooling metal parts. With advancements in cooling technology, manufacturers now have access to innovative systems that ensure uniform cooling, reduce cycle time, and enhance product quality.
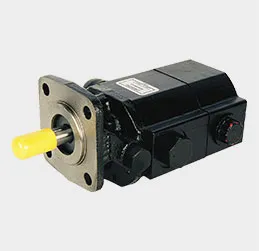
In the realm of die casting, cooling systems are essential in regulating temperature and preventing defects such as warping or internal stresses, which can compromise the integrity of the cast product. An optimized cooling system is crucial for maintaining consistent quality while also bolstering production efficiency.
Expert manufacturers emphasize the importance of tailored cooling solutions that align with the specific requirements of the casting material—be it aluminum, magnesium, or zinc alloys. Integrating advanced thermodynamics, modern cooling systems use fluid dynamics principles to optimize cooling channels within the die, enabling precise temperature control. This approach ensures that parts cool uniformly, reducing residual stresses and resulting in a superior finished product.
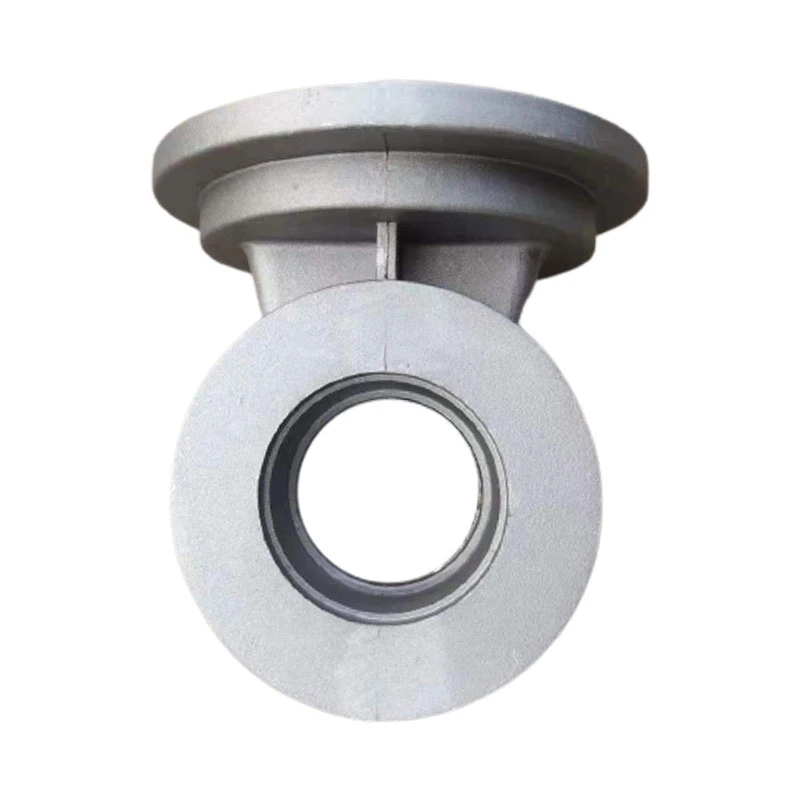
One of the standout innovations in die casting cooling systems is the incorporation of conformal cooling channels, which are designed to follow the contours of the part. This technology allows for improved heat extraction due to increased contact surface area, significantly reducing cooling times. Conformal cooling channels are created using additive manufacturing techniques, which allow for complex geometries that traditional machining methods cannot achieve.
Industry experts highlight the importance of utilizing high-quality materials in designing cooling systems to withstand the rigors of repeated thermal cycling. Advanced materials such as stainless steel and copper alloys are often recommended for their excellent thermal conductivity and durability, ensuring long-lasting performance.
die casting cooling system
Maintaining the cooling system is equally crucial. Routine checks and cleaning schedules help prevent clogs and inefficiencies, which can lead to increased cycle times and reduced product quality. Implementing a robust maintenance plan can prolong the lifespan of the cooling system components, minimizing downtime and reducing production costs.
Innovative monitoring technology is transforming the maintenance landscape by equipping manufacturers with real-time data on system performance. Sensors integrated into the cooling system provide live updates on temperature variations and flow rates, allowing for timely interventions that can prevent system failure and optimize operations.
Proper training for operators and engineers is essential for maximizing the efficiency of die casting cooling systems. Training programs should cover system setup, operation, and maintenance techniques, ensuring that all stakeholders are knowledgeable about the latest advancements and best practices within the industry.
In conclusion, as global demand for high-quality die-cast products continues to rise, manufacturers must invest in sophisticated cooling systems that promise reliability, efficiency, and precision. By aligning cooling system capabilities with production needs, manufacturers can significantly enhance product quality while ensuring economic viability. Establishing trust through demonstrable expertise in die casting cooling systems not only benefits production efficiency but also positions companies as leaders in a competitive market, meeting the ever-evolving needs of various industries.