Chamber die casting is a pivotal manufacturing process that revolutionizes how metal parts are produced, distinguished by its efficiency and precision. With the demand for intricate metal components in industries such as automotive, aerospace, and electronics, understanding the nuances of chamber die casting can offer remarkable advantages.
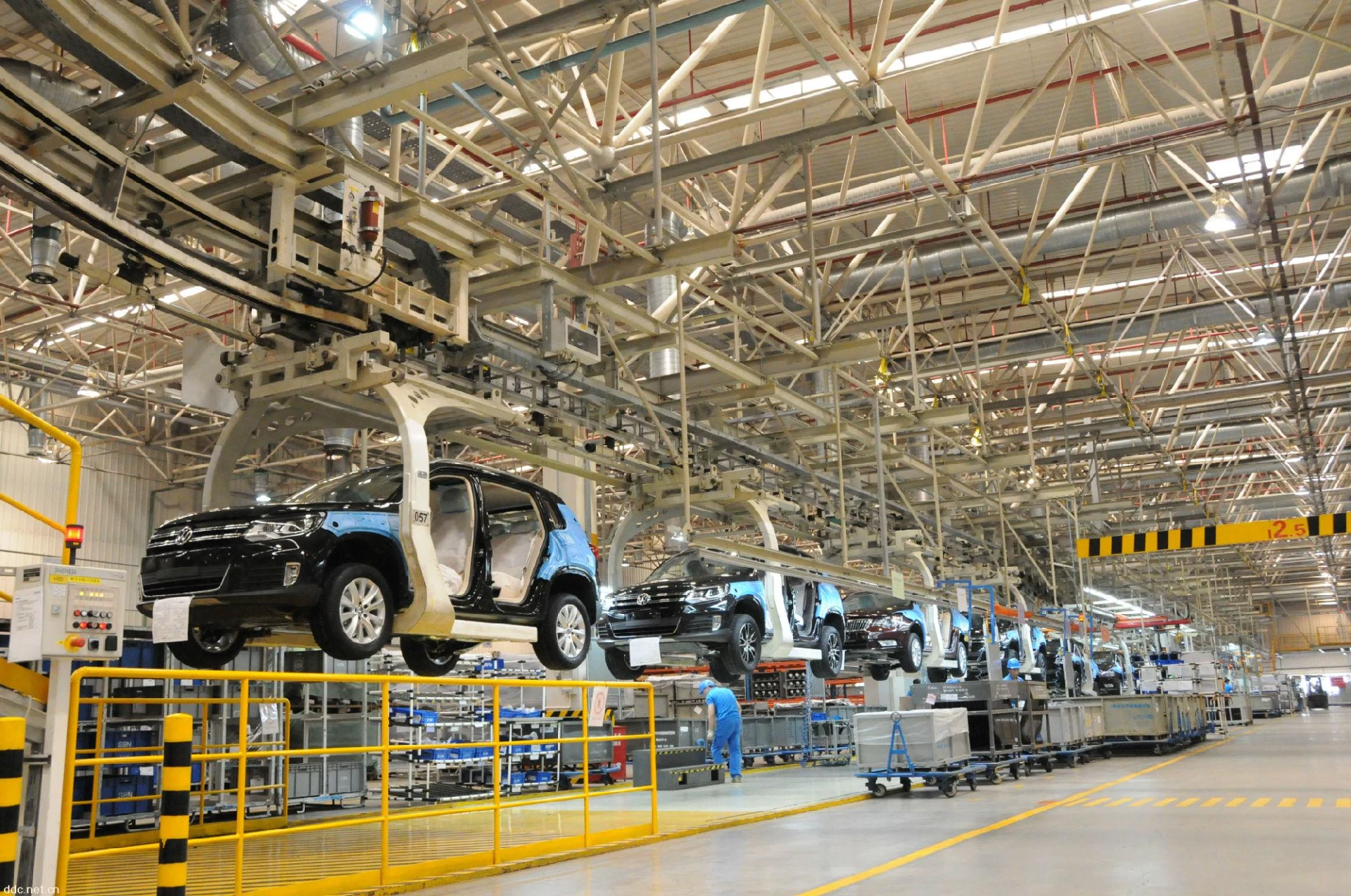
This process involves injecting molten metal into reusable metal molds under high pressure. The chamber die casting is divided into hot and cold categories, each offering distinct benefits depending on the application's requirements. Hot chamber die casting is generally suited for metals with lower melting points such as zinc, magnesium, and certain lead-based alloys. It involves immersing the die in the molten metal, allowing for rapid cycle times due to reduced transportation of the molten material. In contrast, cold chamber die casting, ideal for aluminum, brass, and copper alloys, involves pouring molten metal into the injection system. This distinction is crucial, as it influences the material properties, production speed, and overall cost-effectiveness.
For businesses seeking to leverage chamber die casting, understanding the process's experience, expertise, authoritativeness, and trustworthiness is essential. Experience in chamber die casting translates into a comprehensive understanding of material behavior under varying pressures and temperatures, optimization of cycle times, and the ability to predict and mitigate common issues such as porosity or surface finish defects. Companies with extensive experience in this area, such as those with decades in the industry, can guide new entrants through potential pitfalls and provide invaluable support in refining production processes.
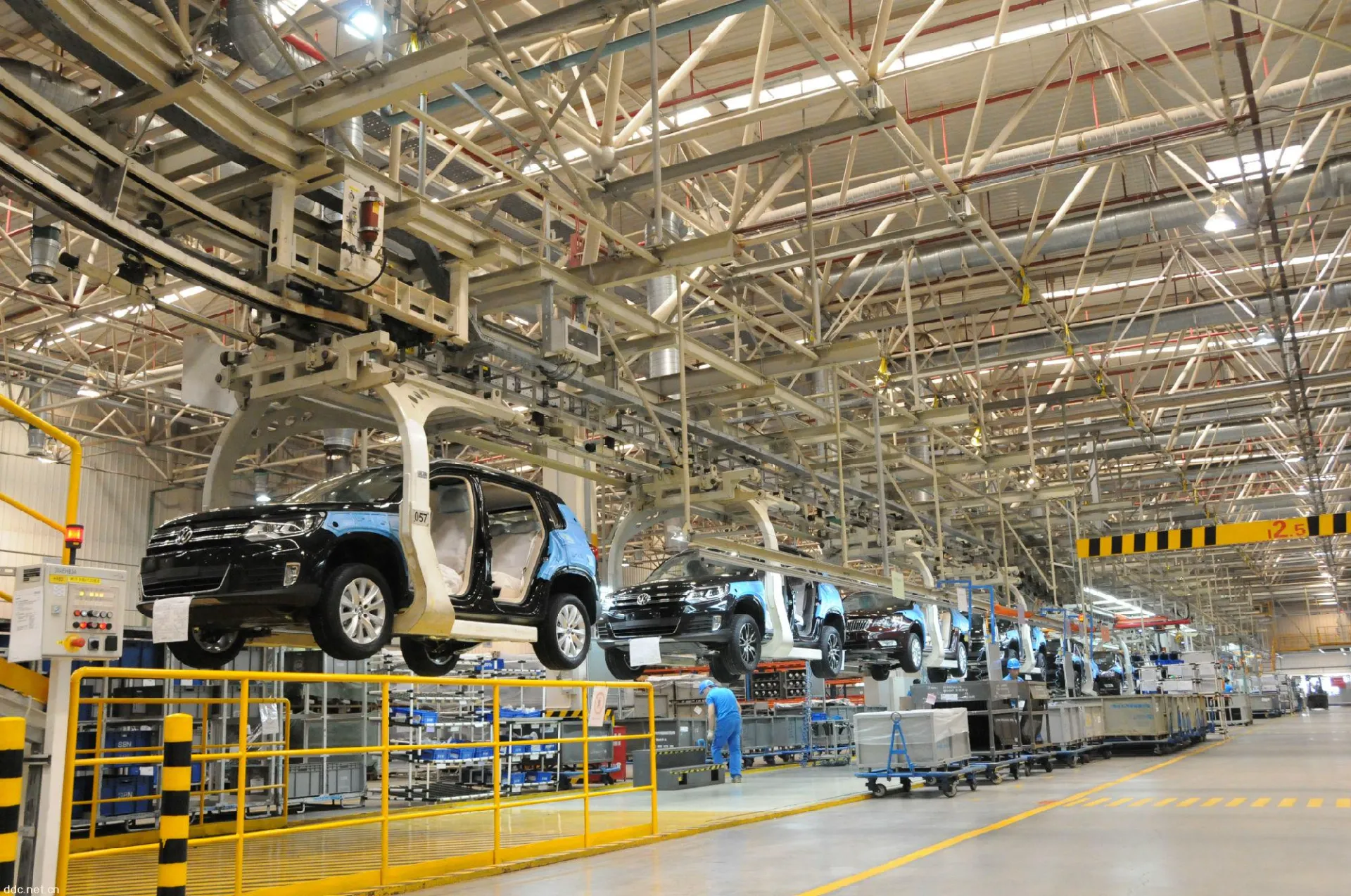
In terms of expertise, the chamber die casting process requires in-depth knowledge of material sciences, as the properties of the finished product are heavily influenced by the alloy composition, die temperature, and injection speed. Expert die casters can manipulate these variables to achieve superior mechanical properties and resilience in the final product, essential for demanding applications.
Authoritativeness in chamber die casting is demonstrated by facilities equipped with cutting-edge technology and adherence to stringent industry standards. These facilities often participate in continuous research and development, showcasing their commitment to innovation and quality. Accredited certifications and partnerships with industry-leading organizations further underscore their authoritative position in the manufacturing landscape.
chamber die casting
Trustworthiness is built through consistent delivery of high-quality components and a transparent relationship with clients. Reputable die casting companies maintain rigorous quality control measures, ensuring each piece meets or exceeds agreed specifications. Moreover, a trustworthy partner offers not just production capabilities but also design assistance, suggesting modifications that might enhance the function or manufacturability of a component.
When considering chamber die casting for production, it's also prudent to evaluate environmental impacts and sustainability practices. Many leaders in this field are adopting more eco-friendly practices, such as using recycled alloys or implementing energy-saving procedures within their operations. These practices contribute positively to both the environment and a company's reputation.
As industries progress, innovations such as advanced computer-aided design (CAD) and simulation technologies are transforming chamber die casting. These tools allow for the preemptive analysis of die designs, reducing the trial-and-error phase significantly, and ensuring more precision in the final product. Businesses that integrate these technologies tend to lead in efficiency and quality, providing a competitive edge in the global market.
In conclusion, chamber die casting is not just a production method but a comprehensive engineering discipline. Its mastery delivers unparalleled advantages in terms of part accuracy, strength, and production efficiency. Choosing the right partner, equipped with a profound grasp of the experience, expertise, authoritativeness, and trustworthiness, can significantly impact your manufacturing success, driving innovation and excellence in your products.