Aluminum sand casting is often hailed as a versatile and cost-effective method for manufacturing intricate metal parts. Having delved deeply into this field over several years, I can share insights that address essential elements of the process while highlighting its practical applications, precise technical nature, industry authority, and the trust built upon consistent results.
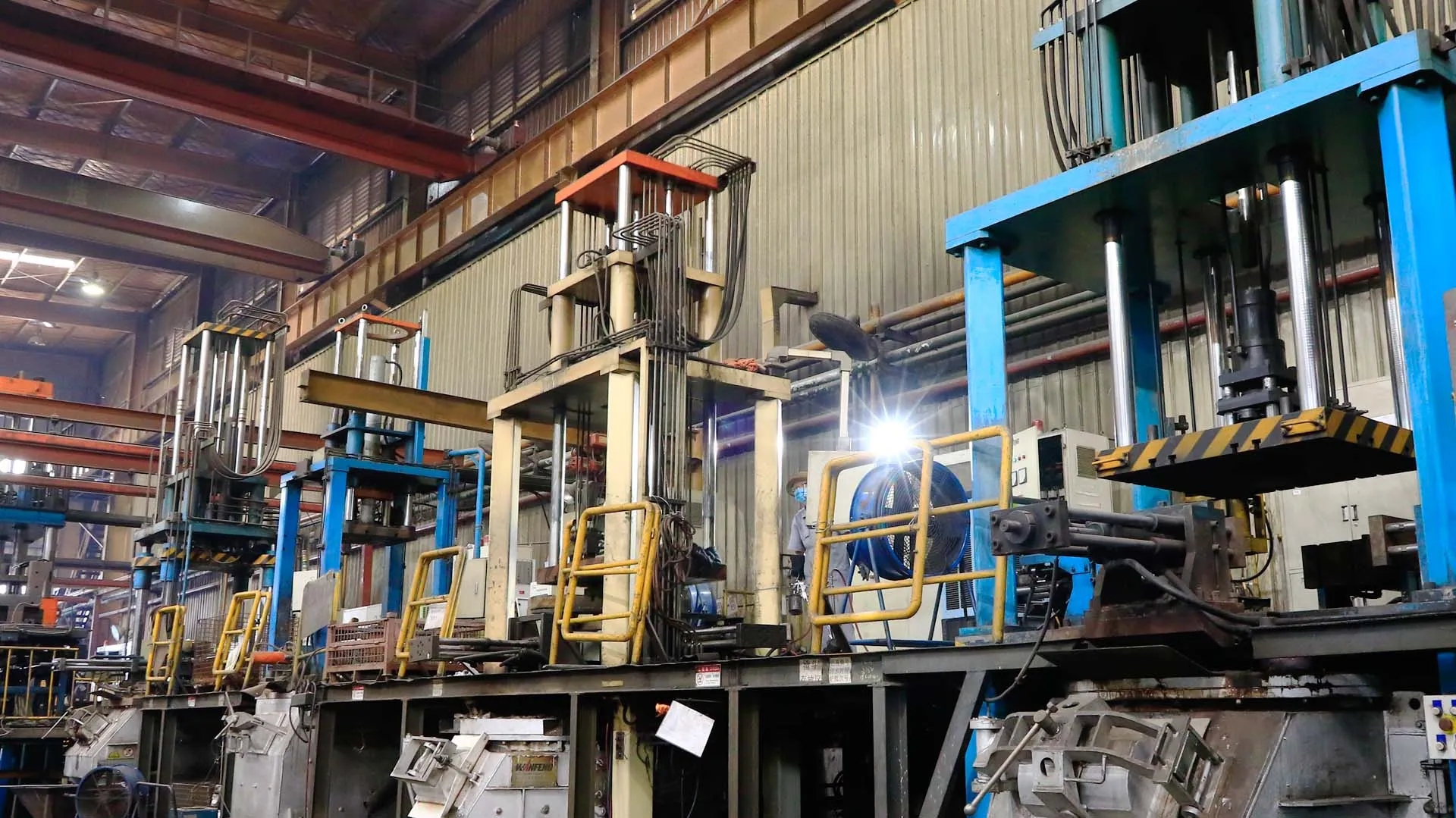
At its core, aluminum sand casting involves creating a mold by packing sand around a pattern of the desired component. The sand mold is then removed, and molten aluminum is poured into the cavity created by the pattern. Once cooled, the mold is broken away to reveal the cast aluminum part. This technique is particularly advantageous when producing complex shapes that would be difficult or cost-prohibitive with other processes. By leveraging sand molds, manufacturers can achieve intricate geometries and surface details with high accuracy and repeatability.
Experience dictates that the success of aluminum sand casting heavily relies on the quality of the sand and the expertise of the foundry workers involved. High-quality silica sand is generally preferred due to its uniform grain size and high melting point, ensuring the mold holds its shape under the extreme temperatures of molten aluminum. Equally crucial is the know-how of the craftsmen who prepare and handle the molds, as even a minor deviation in the sand-packing process can lead to defects and imperfections in the final product.
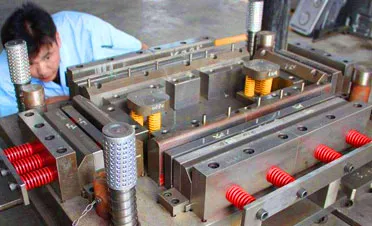
In my practice, collaboration with an engineering team is essential to optimize the design of the component for sand casting. This collaboration helps mitigate common casting defects such as porosity, which can compromise the integrity of the cast piece. Employing computer-aided design (CAD) models and simulations can predict potential issues and streamline the manufacturing process. By identifying and addressing these issues early, manufacturers can reduce waste, lower costs, and improve the overall quality of the finished product.
The authority of aluminum sand casting in various industries cannot be overstated. Its applications span automotive, aerospace, and marine sectors, where durability and performance are critical. For instance, automotive manufacturers often use aluminum sand casting to produce engine blocks, cylinder heads, and other crucial components that require lightweight characteristics without sacrificing strength. The aerospace industry similarly benefits, employing this process for crafting intricate parts like housings and brackets that demand high-performance materials.
aluminum sand casting
Aluminum itself is a preferred metal in casting due to its excellent corrosion resistance, mechanical properties, and recyclability. It's no surprise that many industries regard aluminum sand casting not just as a means of production but as an environmentally friendly choice that aligns with the growing demand for sustainable manufacturing practices.
Trust in aluminum sand casting is built through rigorous quality assurance and adherence to industry standards. It's imperative for foundries to conduct comprehensive inspections, utilizing techniques like X-ray and ultrasonic testing to detect subsurface flaws and ensure the integrity of the castings. Certification from recognized bodies, such as ISO and ASTM, further validates the quality management systems in place, bolstering confidence among clients and stakeholders.
Producing consistently high-quality aluminum castings engenders trust, and being transparent about the processes and checks involved enhances that trust. Companies often provide detailed reports outlining the process controls, test results, and certifications associated with each casting. This approach not only reassures clients of the reliability of their suppliers but also fosters long-lasting partnerships based on proven performance and accountability.
Aluminum sand casting, through experience, expertise, authoritative application, and trustworthiness, serves as a cornerstone of modern manufacturing. It stands as a testament to the harmonious blend of traditional craftsmanship and modern technology, offering endless possibilities for engineers and product designers seeking to push the boundaries of what aluminum components can achieve.