When it comes to welding die cast metal, the process involves combining an intricate blend of art and science. Over the past few decades, die casting has emerged as a preferred method for manufacturing high-precision metal components, providing advantages like high dimensional accuracy, smooth surface finishes, and complex geometrical flexibility. However, the intricacy increases when these die-cast components require welding, a factor often dictated by the design or repair needs within an industrial context.
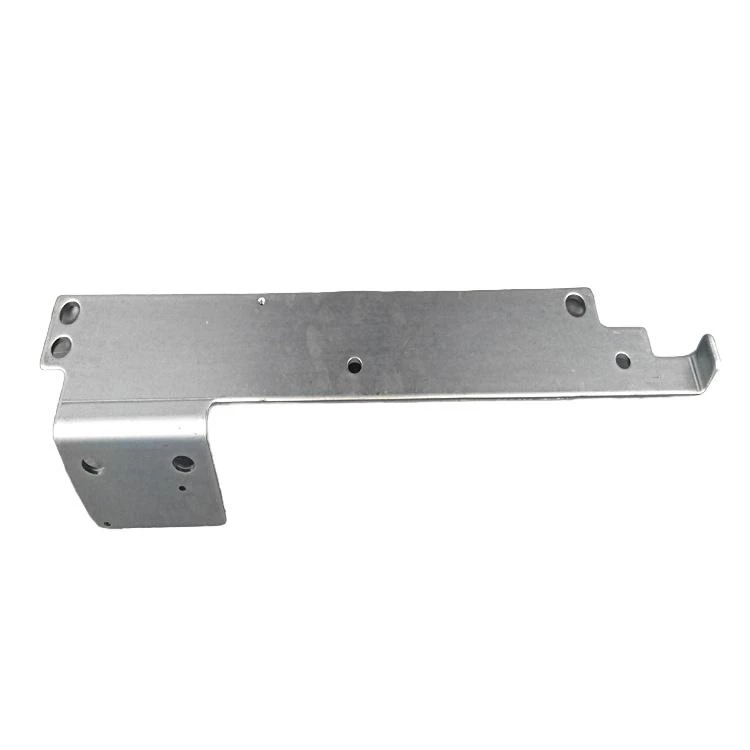
Expertise in welding die-cast metals begins with understanding the unique properties of the materials involved. Die-cast metals, ranging from aluminum and zinc to magnesium and other alloys, present distinctive challenges due to their lower melting points and the presence of casting imperfections like porosity. These factors make the welding of die-cast metals more complex compared to traditional metal welding processes.
For industry professionals, selecting the appropriate welding technique is pivotal. TIG (Tungsten Inert Gas) welding and MIG (Metal Inert Gas) welding are two prevalent methods. TIG welding, with its ability to provide control and precision, is often favored for thinner die-cast components and applications where aesthetics are paramount. Conversely, MIG welding, known for its speed and ease, is suitable for thicker sections and faster production environments.
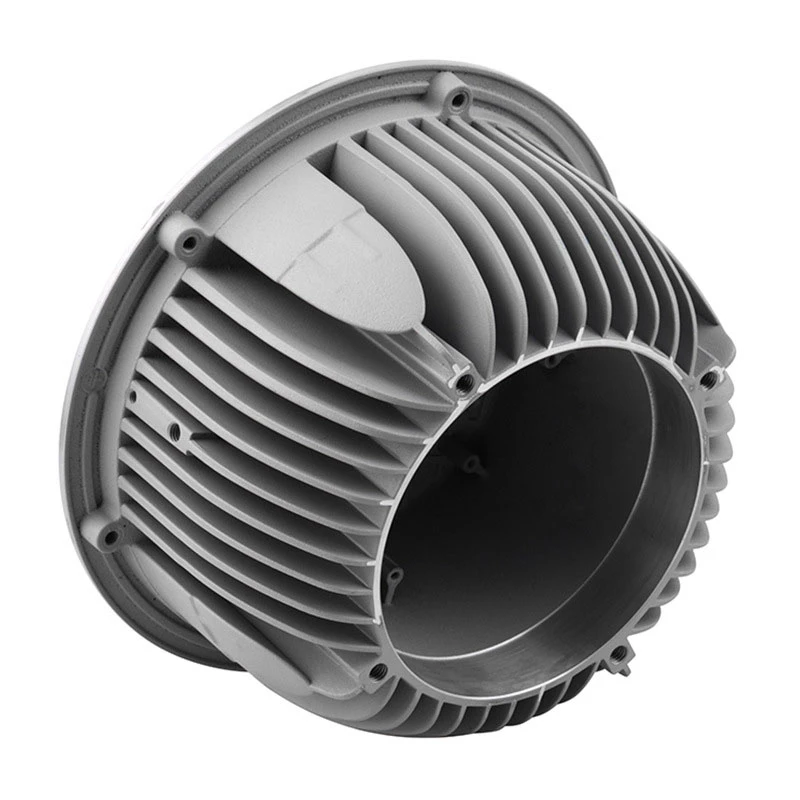
Experience underscores the importance of preparation. Adequate surface cleaning, to remove oxides and contaminants, is crucial. The application of appropriate pre-heat temperatures can significantly mitigate cracking risks, especially for aluminum alloys. Welding experts emphasize the necessity of post-weld heat treatments to relieve residual stresses, ensuring structural integrity and preventing future failures in welded joints.
Authoritativeness in this domain is backed by industry standards and certifications. Professionals often adhere to guidelines set forth by authoritative bodies such as the American Welding Society (AWS) and the International Organization for Standardization (ISO). These standards ensure not only the quality of the welds but also the safety and reliability of the components in their operational environments.
welding die cast metal
Practitioners in the field of welding die-cast metals are constantly innovating. The introduction of advanced techniques like ultrasonic welding and friction stir welding represents a seismic shift in capability. Ultrasonic welding, for instance, offers advantages in joining thin or delicate sections by using high-frequency ultrasonic vibrations, which create strong bonds without excessive heat input. Similarly, friction stir welding is gaining traction for its ability to join metals without melting, reducing defects and improving mechanical properties.
Trustworthiness in welding die-cast metal is often underscored by a track record of successful applications across industries such as automotive, aerospace, and consumer electronics. In these sectors, welded die-cast components play critical roles, from engine parts to intricate housing for electronic components, necessitating reliable execution and precision.
Real-world case studies highlight the transformative impact of proficient die-cast metal welding. In the automotive industry, for instance, intricate lightweight structures are now possible due to advancements in welding techniques, which contribute to overall vehicle efficiency and performance. Similarly, in aerospace, the joining of die-cast components has enabled innovations in aircraft design that emphasize weight reduction without compromising strength or safety.
To underscore trustworthiness and continual improvement, companies in this field invest in ongoing training and research. By staying at the forefront of technological advancements and understanding material science nuances, they offer trustworthy and cutting-edge solutions to meet modern manufacturing demands.
In conclusion, mastering the welding of die-cast metal involves a symbiosis of experience, expertise, authoritativeness, and trustworthiness. As the manufacturing landscape evolves, the emphasis on refining and perfecting welding processes for die-cast metals remains crucial, ensuring reliability and excellence in various applications worldwide.