Precision casting, also known as investment casting or lost-wax casting, stands as a beacon of modern manufacturing excellence. Its roots trace back to ancient civilizations, yet its applications and precision have evolved, shaping industries with technological acumen and artisanal expertise.
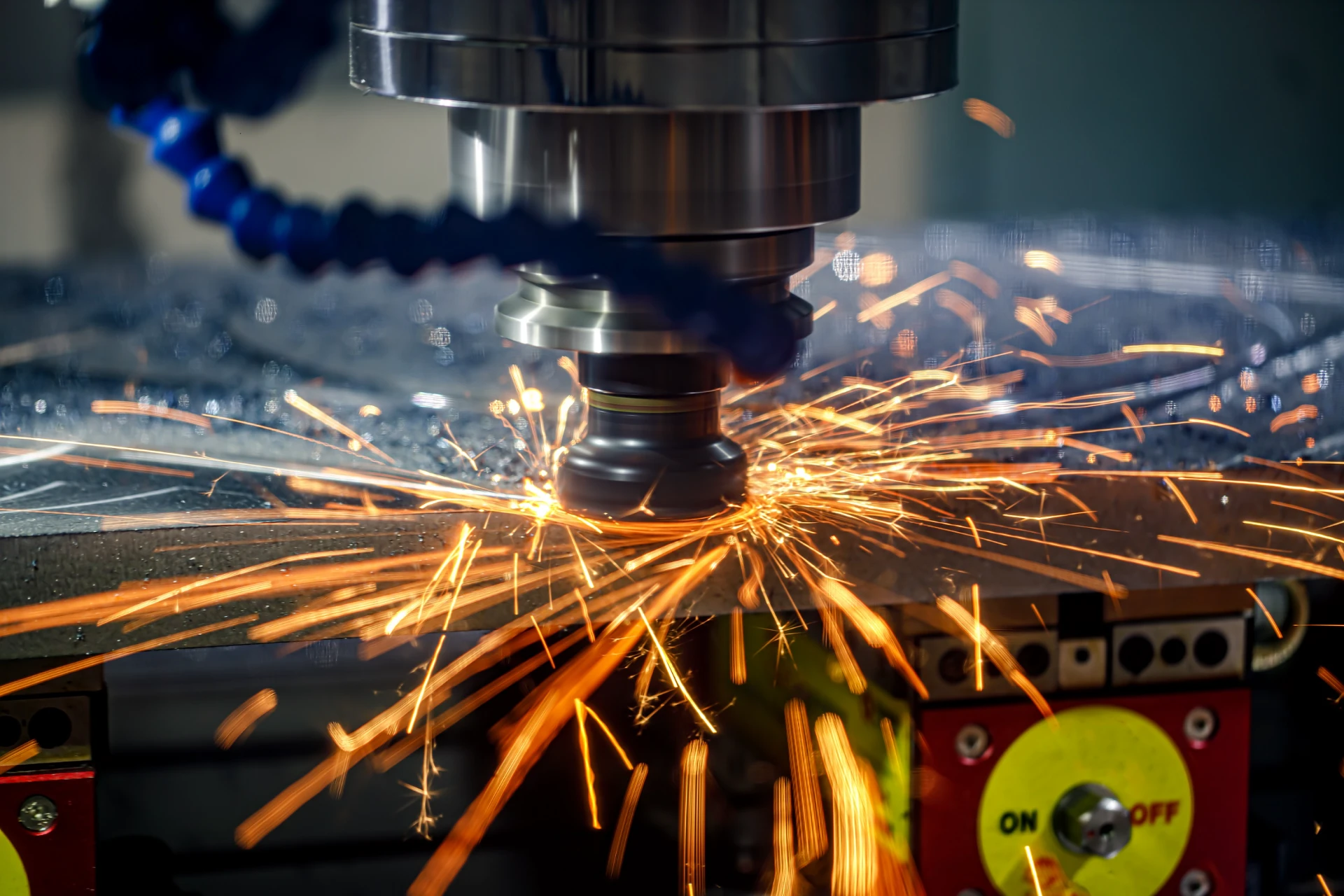
The precision casting process begins with the creation of a wax model, an exact replica of the desired end product. This wax is meticulously crafted to accommodate nuances and intricacies that define the component's ultimate functionality and aesthetic. It highlights the expertise required, as the fidelity of this model dictates the precision of the final cast. One can appreciate the artistry and attention to detail, reflecting years of experience honed into each phase of manufacture, from aerospace to medical implants.
Upon completing the wax model, it undergoes a ceramic shell coating process. Here, skilled technicians layer a refractory material onto the model, building a mold that can tolerate the extreme temperatures required in casting. This phase exemplifies trustworthiness, as this mold must withstand the rigors of metal casting without faltering. The authoritative craftsmanship becomes evident when the ceramic shell is subjected to high heat, causing the wax to melt and leave behind a void that will host molten metal.
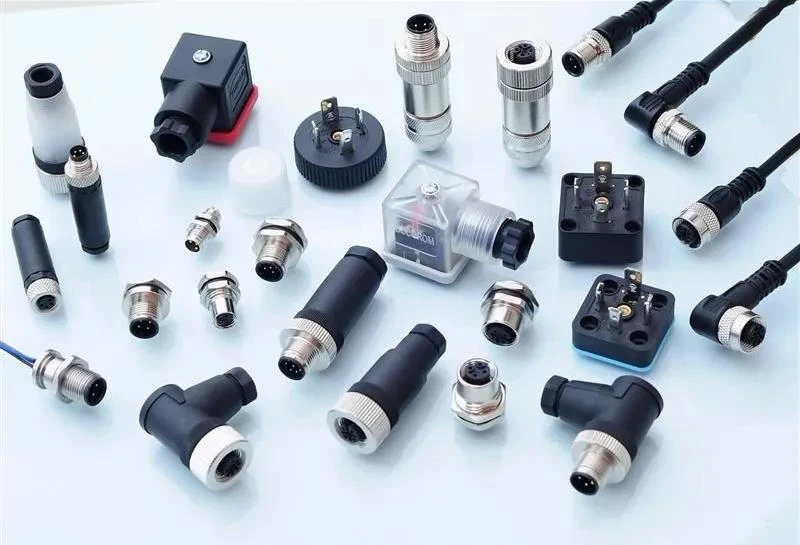
Once the mold is heated further to prepare for metal introduction, it is critical to maintain precise temperature control to ensure perfect fluidity and compound integrity of the molten metal. Expert metallurgists decide which alloys best fit the structural, thermal, and mechanical specifications needed for each project. Precision casting companies showcase their credibility by managing these conditions with cutting-edge technology and stringent quality control measures, ensuring every product meets rigorous industry standards.
The filling process is where precision gets its name. With molten metal introduced, the mold's tiniest details are captured with remarkable accuracy. This is the crux of the expertise applied throughout history and has made precision casting a cornerstone in producing complex geometries unattainable through other methods. The industry's reliance on Certified Precision Casting Foundry further cements its authority in manufacturing high-performance, critical-use components that demand stringent tolerance levels.
precision casting
Cool-down is gradual, a necessary practice to prevent the cracking or warping of the intricate cast. This patience, this dedication to precision, assures each component retains its engineered functionality. Afterward, the ceramic shell is broken away, unveiling the raw casting that combines raw material quality, technological sophistication, and skilled craftsmanship. Post-casting processes such as heat treatment, hipping (hot isostatic pressing), and surface finishing enhance material properties, underscoring manufacturers' commitment to excellence and upholding their trustworthiness hallmark.
Precision casting's applications are remarkably diverse, touching lives across countless industries. In aerospace, it provides lightweight yet robust turbine blades, and in automotive, it contributes to components that enhance fuel efficiency and emissions control. This process is equally vital in healthcare, where the precise manufacture of joint replacements and surgical tools ensures improved patient outcomes. The industry's ability to produce reliable components speaks volumes about its exhaustive expertise and experience, earning the unwavering trust of end-users.
In closing, precision casting stands not only as a pivotal manufacturing technology but as a testament to a heritage of craftsmanship combined with relentless innovation. Expertise and trustworthiness resonate across its chronicles, driving advancements that impact every modern industry's development and sustainability.
To explore precision casting solutions, fidelity in design, and success in implementation, engage with industry leaders who embody these principles as a bridge to future advancements and continual improvements in manufacturing science.