Understanding the intricate world of stamping dies demands a deep dive into both the macro and micro-components that collectively ensure precision in metal fabrication. A stamping die, integral to the manufacturing industry, is a specialized tool used to cut or shape metal using a press. Each part plays a crucial role in this process, offering remarkable precision and efficiency in producing complex components. This exploration of the parts of a stamping die reveals not only the surprising sophistication behind these tools but also why they are indispensable in advanced manufacturing.
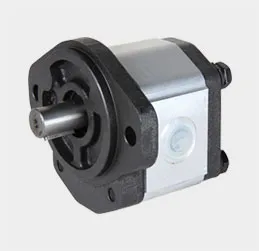
To appreciate the operational excellence of a stamping die, one must first understand its primary components. The architecture of a die comprises several key parts, including the die block, punch, stripper plate, and pilot, each meticulously crafted to perform specific functions.
The die block serves as the foundation of the die assembly. Typically made from high-strength alloy steel, the block is designed to handle substantial stress and maintain structural integrity under high-pressure conditions. It contains the die cavity, a critical element that defines the shape of the workpiece. Precision in the design and machining of the die block is vital for ensuring accuracy in the final product.
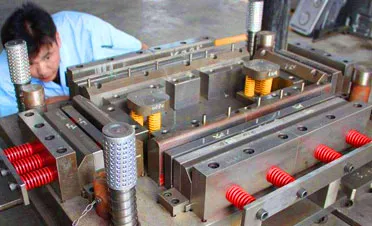
Complementing the die block is the punch. This component acts like a hammer, descending into the die block to execute the cutting or shaping of the workpiece. The material selection for the punch, often a sturdy tool steel, combines toughness with wear resistance, catering to the rigorous demands of continuous industrial use. The geometry of the punch must align with the die cavity to produce the desired outcomes, highlighting the need for precision engineering.
Another essential component is the stripper plate. The stripper plate works to securely hold the sheet metal in place, ensuring that there is no movement as the punch executes its action. This helps in preventing material distortion and maintains the integrity of the workpiece. The stripper plate's design typically incorporates springs or pressure pins for smooth operation, underscoring its critical function in maintaining alignment and stability.
Pilots are yet another vital component found in progressive dies. They serve as guides for the positioning of the metal sheet, ensuring that each subsequent operation aligns perfectly with the previous one. This precision in placement minimizes waste and maximizes efficiency, demonstrating the meticulous attention to detail inherent in die design.
parts of a stamping die
Equally significant in the assembly of a stamping die is the consideration for dies’ maintenance and lifespan. As these components are subjected to high pressures, they must be regularly inspected, maintained, and replaced as needed to reduce downtime and maintain production quality.
The construction of a stamping die also involves the development of specialized coatings for components like punches and die blocks. These coatings reduce friction and enhance the hardness of the tool surfaces, significantly extending their operational life and improving performance.
Advanced technologies in computer-aided design (CAD) and computer-aided manufacturing (CAM) have revolutionized the development of stamping dies, increasing the complexity of designs that can be fabricated with precision. Engineers can now simulate various stamping operations digitally, enabling the optimization of die components before physical production begins. This technological synergy allows for the creation of highly intricate metal parts with reduced trial and error, saving both time and resources.
Incorporating feedback loops from real-world usage back into the design and manufacturing processes of stamping dies emphasizes the importance of continuous improvement and innovation. Industry experts continually gather data on wear patterns, operational efficiency, and failure points to develop enhanced designs that offer greater reliability and efficiency.
Trust in stamping dies is bolstered by rigorous quality control processes. Every die is subjected to stringent testing and inspection to ensure that it meets the exacting standards of industrial manufacturing. This adherence to quality ensures the delivery of components that are not only precise but also consistent, enhancing their reputation as reliable tools in metal fabrication.
Overall, understanding the individual roles of each part of a stamping die reveals a finely tuned system, where precision, craftsmanship, and technology converge to produce high-quality, consistent metal products. With continued technological advancements, the functionality and capabilities of stamping dies will further expand, continuing to meet the evolving demands of the manufacturing landscape with authority and trustworthiness.