Die casting design calculations are pivotal in ensuring the production of high-quality components for various industrial applications. Delving into the intricacies of these calculations goes beyond just understanding formulas; it requires a combination of experience, expertise, authoritativeness, and trustworthiness.
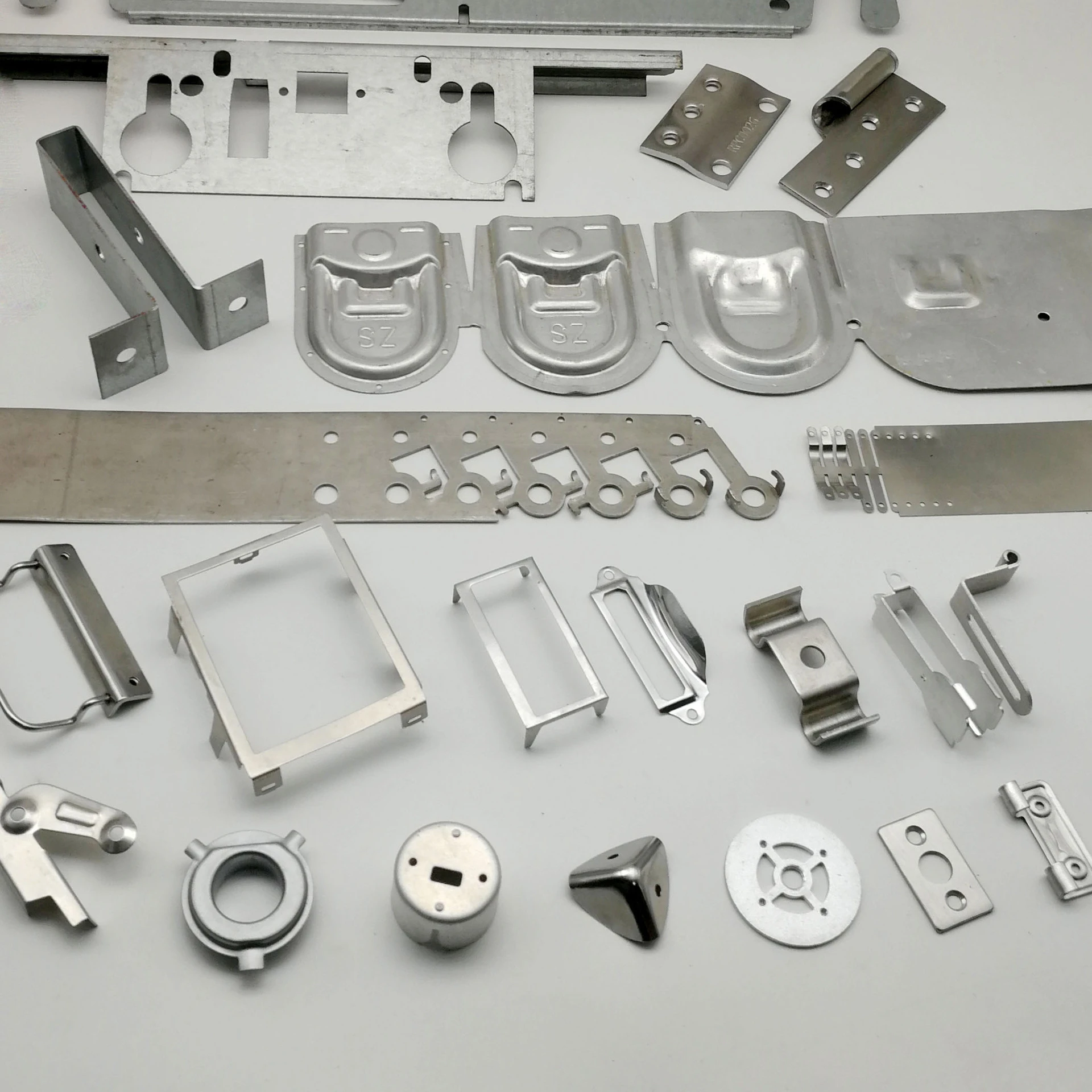
Firstly, understanding the nuances of die casting design begins with recognizing the material properties. Different materials, each with distinct melting points, thermal conductivity, and cooling rates, play a crucial role in influencing the design calculations. For example, when working with aluminum, renowned for its lightweight and high corrosion resistance, one must account for its specific characteristics during the cooling phase. This not only ensures structural integrity but also enhances the surface finish quality, reducing the necessity for further post-processing.
A pivotal aspect of the calculations is the gating system design. Achieving an optimal flow of molten metal into the die cavity is not just about the speed of injection but involves fine-tuning the gating system to minimize turbulence, avoid air entrapment, and enhance the final product's mechanical properties. Experience dictates that intricate designs frequently require simulation software to predict and rectify potential flow issues long before they become a reality on the production floor.
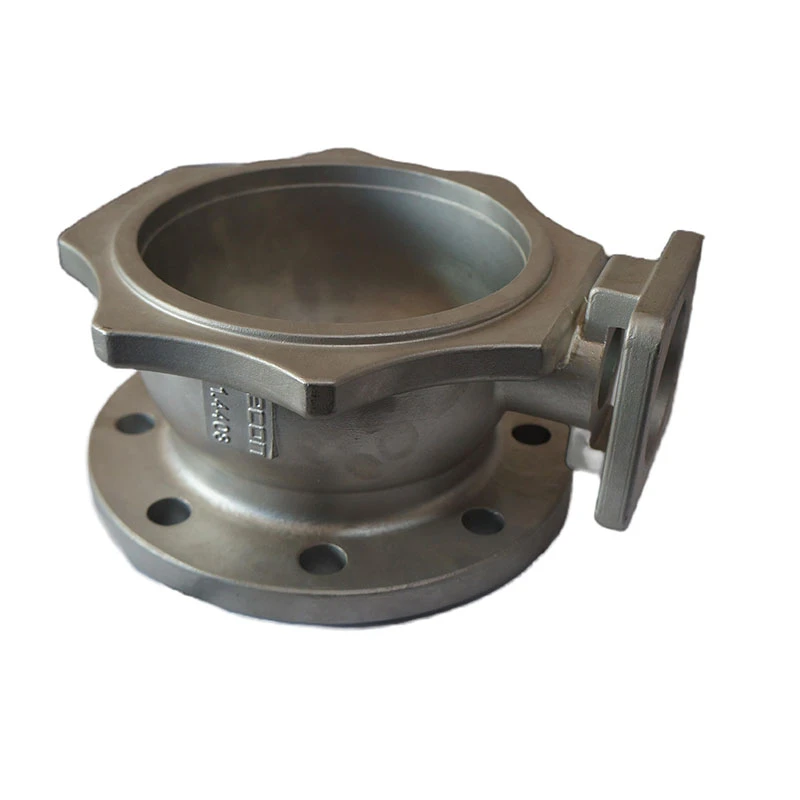
Furthermore,
the cooling system's design calculation is another cornerstone in die casting. Effective heat removal not only affects the cycle time but also impacts the mechanical properties of the cast component. The inclusion of strategically placed cooling channels can reduce cycle time, enhance the dimensional stability of the casting, and extend the die's operational lifespan. Expertise here stems from a keen understanding of thermal dynamics as well as practical experience in deploying various cooling techniques in real-world scenarios.
die casting design calculations
Dimensional analysis in die casting design calculations involves thorough consideration of shrinkage factors. Shrinkage, a natural consequence as the metal solidifies, differs across materials and needs precise calculations to ensure that the final product dimensions meet specifications. Trustworthy designs account for these variables by employing both historical data and cutting-edge simulation techniques to iterate and refine dimensions.
The last yet indispensable aspect is the selection of the appropriate die casting process parameters. These parameters include injection pressure, temperature, and plunger velocity, which must be meticulously calculated to avoid casting defects such as porosity and incomplete filling. Authoritativeness in this domain is marked by a manufacturer's ability to adjust these parameters dynamically, based on both statistical data and real-time monitoring insights.
In terms of advancements, leveraging technologies such as AI-driven algorithms can significantly enhance the precision of die casting design calculations. By analyzing large datasets from previous projects, these intelligent systems can predict outcomes and recommend adjustments with an accuracy unattainable through traditional methods.
In conclusion, the profound understanding and application of die casting design calculations are critical in producing high-quality parts that meet industry standards. This involves a harmonious blend of scientific principles, practical experience, and advanced technology. By embodying the principles of Experience, Expertise, Authoritativeness, and Trustworthiness, manufacturers can not only assure quality and efficiency but also maintain a competitive edge in the ever-evolving industrial landscape.