In the dynamic world of manufacturing, the advancement of die casting technologies is reshaping how products are developed and brought to market. New die casting processes are not just pushing the boundaries of what’s possible; they’re redefining expectations in terms of efficiency, quality, and sustainability.
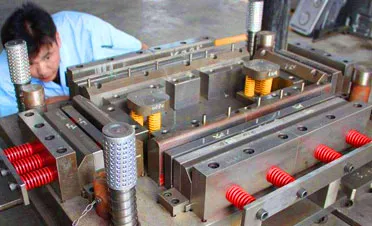
Die casting, by definition, involves forcing molten metal into a mold cavity under high pressure. While traditionally this technique has been synonymous with producing complex parts in large quantities, advancements in new die casting techniques are changing the landscape by offering improved precision, strength, and sustainability.
One of the most significant innovations in new die casting is the integration of advanced materials and alloys. By optimizing the metallurgical properties, manufacturers can produce parts that are not only lighter and stronger but also enhance the performance of the end product. For instance, the introduction of new aluminum-zinc alloys is enhancing the fatigue resistance and strength-to-weight ratio in automotive applications, directly contributing to more fuel-efficient and durable vehicles.
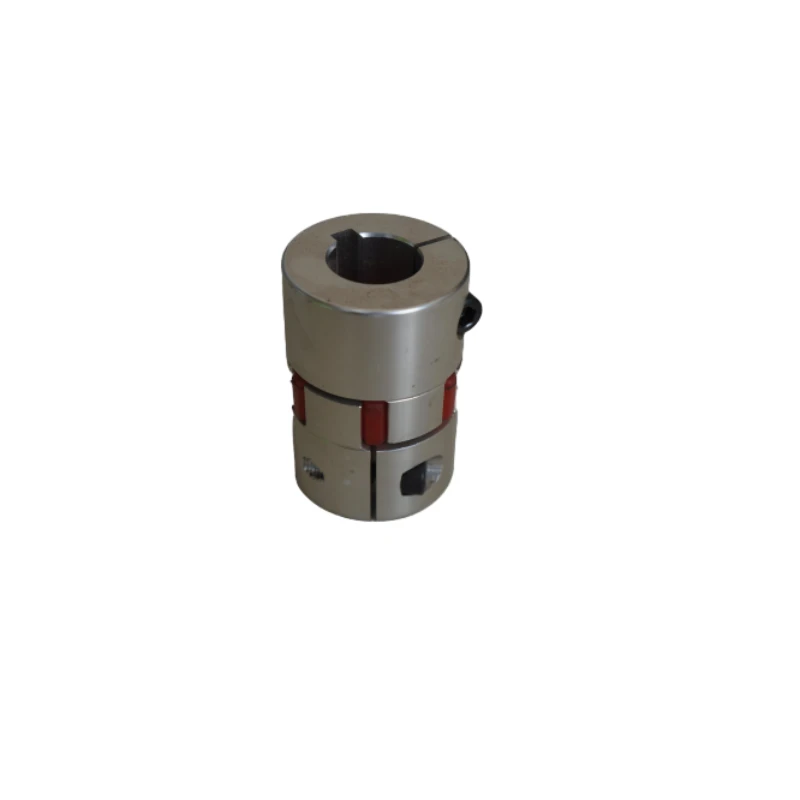
New die casting technologies are also embracing smart manufacturing principles. Advanced automation and real-time monitoring systems ensure that the die casting process is not only faster but also more reliable. Innovations such as closed-loop process controls use sensors and data analytics to monitor every stage of the casting process, significantly reducing wastage and improving the overall yield. This ensures that each cast part meets precise specifications and significantly reduces the rejection rates, which is a critical component when considering large-scale production costs and timeframes.
Another area where new die casting is making a mark is through the reduction of its environmental impact. Traditional manufacturing processes often face scrutiny for their carbon footprint, but pioneering die casting techniques are addressing these concerns. The adoption of energy-efficient furnaces and the recycling of scrap metal within the production cycle are ensuring that die casting remains at the forefront of sustainable manufacturing practices. Moreover, the precision offered by modern die casting reduces the necessity for secondary machining, further decreasing energy consumption and material waste.
new die casting
From an expert perspective, it’s essential to recognize the role of computer-aided design (CAD) and computer-aided engineering (CAE) in new die casting processes. These technologies allow engineers to simulate die casting operations before the physical process begins, identifying potential faults or inefficiencies. By optimizing the design and engineering phases, manufacturers can anticipate challenges and refine their processes to significantly reduce lead times and costs associated with trial and error. This level of predictive precision speaks volumes to expertise in the field.
Authoritativeness in the realm of new die casting emerges from the convergence of industry standards with technological advancements. Organizations are increasingly collaborating globally to set benchmarks, ensuring consistent quality and safety standards across the board. By adhering to these standards, companies reinforce their credibility, assuring clients and stakeholders of their commitment to delivering high-quality products.
Trustworthiness is another crucial pillar that underscores modern die casting techniques. Through transparency and the adoption of ISO standards, manufacturers offer clients peace of mind by ensuring that the production processes are not only innovative but also ethically and environmentally sound. Clients today demand full transparency not just about the product but also about how it is made, and new die casting meets this demand seamlessly.
In conclusion, new die casting technologies are setting the stage for a more efficient, sustainable, and high-quality production landscape. By harnessing advanced materials, automation, sustainability practices, and strict adherence to industry standards, die casting professionals can assure stakeholders of exceptional product outcomes. Keeping abreast with these developments is not just about staying competitive; it’s about pioneering the future of manufacturing.