In the intricate world of manufacturing, efficiency and precision are paramount.
Hot and cold chamber die casting processes have emerged as pivotal solutions in the production of complex metal components. As a seasoned industry expert, understanding the intricacies of these methods not only enhances credibility but also ensures the delivery of high-quality products.
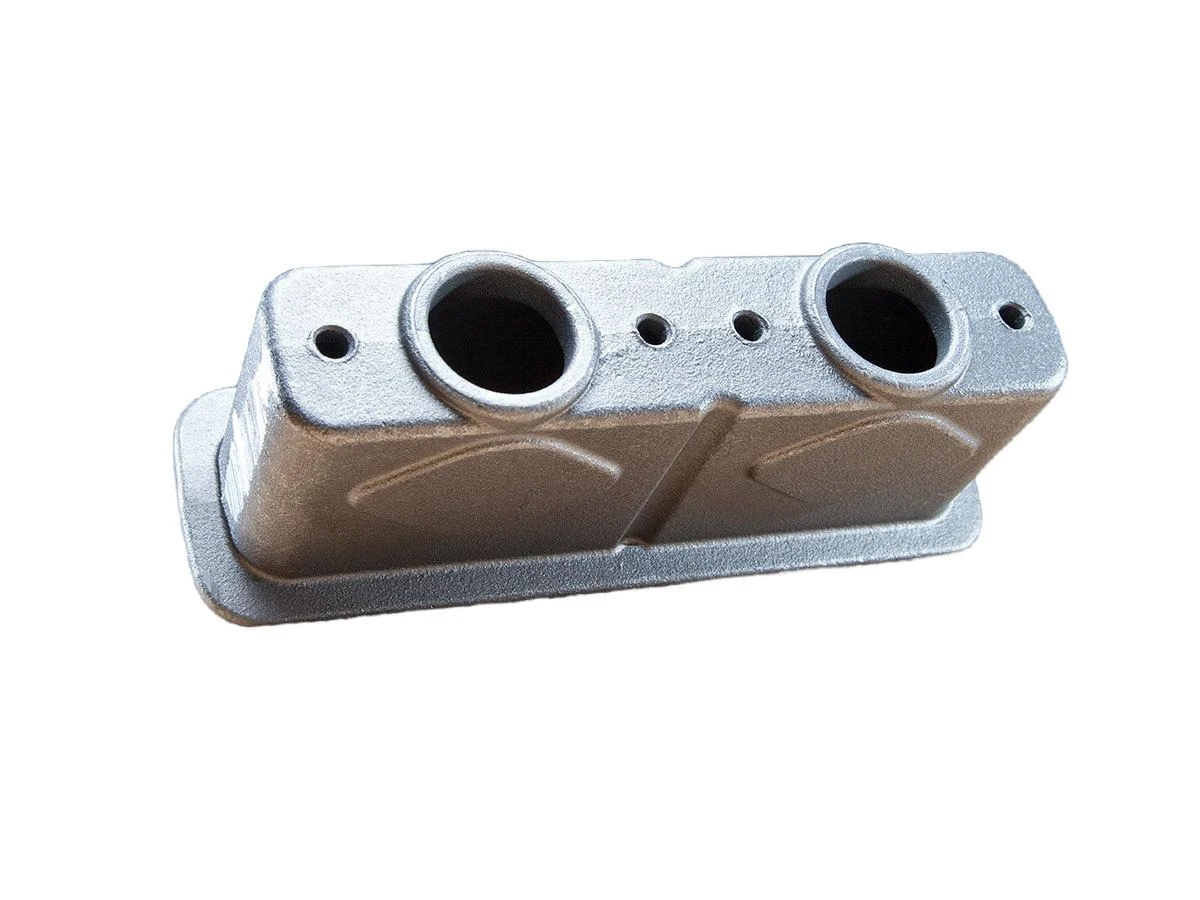
Die casting is a metal casting process that harnesses high-pressure techniques to mold metal into specific shapes. This process is differentiated by the type of chamber used—hot or cold—each catering to different types of metals and end applications.
The hot chamber die casting process is defined by its efficiency and speed, making it ideal for metals with low melting points such as zinc, magnesium, and certain tin-based alloys. This process involves a molten metal reservoir connected to the die cavity via a gooseneck. The metal is injected into the die, where it rapidly cools and solidifies. One notable advantage of hot chamber die casting is its ability to offer fast cycle times due to the direct access of the molten metal to the chamber, reducing the time needed for metal transportation.
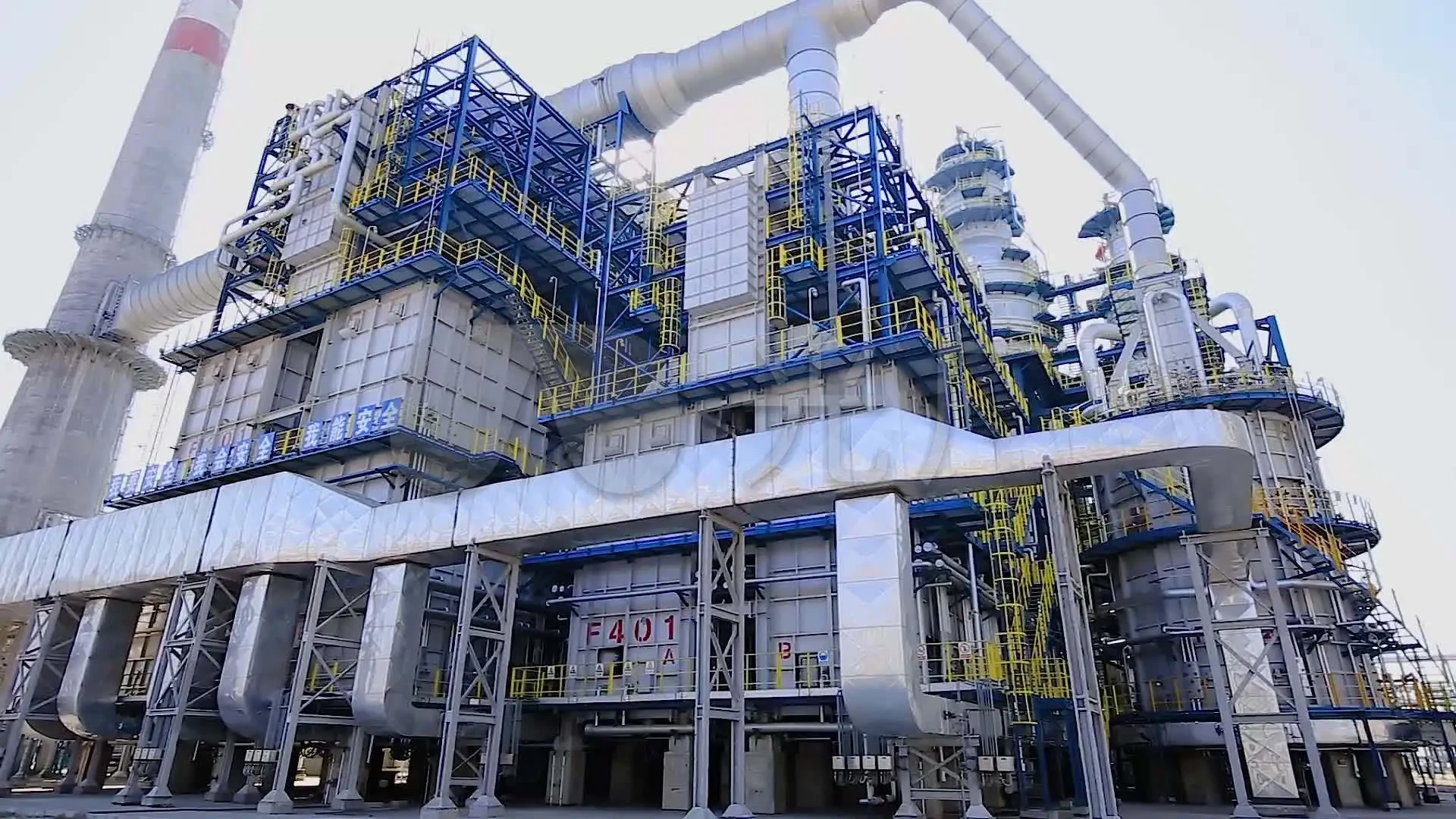
Industry professionals recognize several benefits of the hot chamber process. The automation of the system, coupled with minimal manual handling of molten metal, not only enhances workplace safety but also maintains product consistency. The reduced exposure to atmospheric conditions during casting limits oxidation and other potential defects, an essential consideration for maintaining integrity in high-quality components. Thus, when high output and consistent quality are required, the hot chamber process becomes an industry favorite.
In contrast, the cold chamber die casting process is tailored for metals with higher melting points, such as aluminum and copper alloys. In this approach, molten metal is manually ladled into a cold cylinder before being injected under high pressure into the die. This separation from the furnace ensures the machinery withstands higher temperatures without degrading over time. However, this process typically involves longer cycle times due to the steps involved in manually transferring the molten metal.
hot and cold chamber die casting
While the cold chamber process might seem labor-intensive, it is revered for its precision in producing components with complex geometries. Its ability to work with high-strength alloys expands its use in industries where durability and resistance to extreme conditions are required, such as aerospace and automotive sectors.
The choice between hot and cold chamber die casting depends heavily on the specific project requirements. Factors such as part size, geometrical complexity, production volume, and material properties dictate which method suits best. For instance, zinc’s low melting point and excellent fluidity make it a prime candidate for hot chamber casting, whereas aluminum’s strength and lightweight nature make it suitable for cold chamber casting.
Moreover, die casting professionals must consider the environmental impact and operational costs associated with each method. Hot chamber die casting generally offers lower operational costs due to its faster cycle times and energy efficiency. However, cold chamber die casting can offer a higher return on investment for large-scale projects requiring durable parts due to its ability to accommodate a wider range of metal alloys.
The advanced nature of both hot and cold chamber die casting methods underscores the importance of ongoing research and development in the field. Cutting-edge technologies, such as computerized process monitoring and enhanced metallurgical techniques, are being incorporated to optimize performance, enhance precision, and reduce wastage. Staying abreast of technological advancements and integrating them into traditional practices fortifies a manufacturer’s position as both an innovator and a reliable provider in the industry.
In conclusion, the expertise required to navigate the nuances of hot and cold chamber die casting cannot be overstated. For manufacturers and engineers, understanding the specific advantages and limitations of each method is crucial. Mastery of these processes not only elevates the quality and consistency of produced components but also builds trust with clients—a fundamental pillar for any successful enterprise in this competitive field. By continually advancing knowledge and adapting to new techniques, industry leaders reinforce their authority, offering reassurance of their unwavering commitment to excellence.