Die cast parts are the heartbeat of many modern manufacturing processes, particularly in the automotive and consumer electronics industries. My journey with die casting began over two decades ago, and through hands-on experience, I've witnessed the evolution and the nuances that define its impact in today's world.
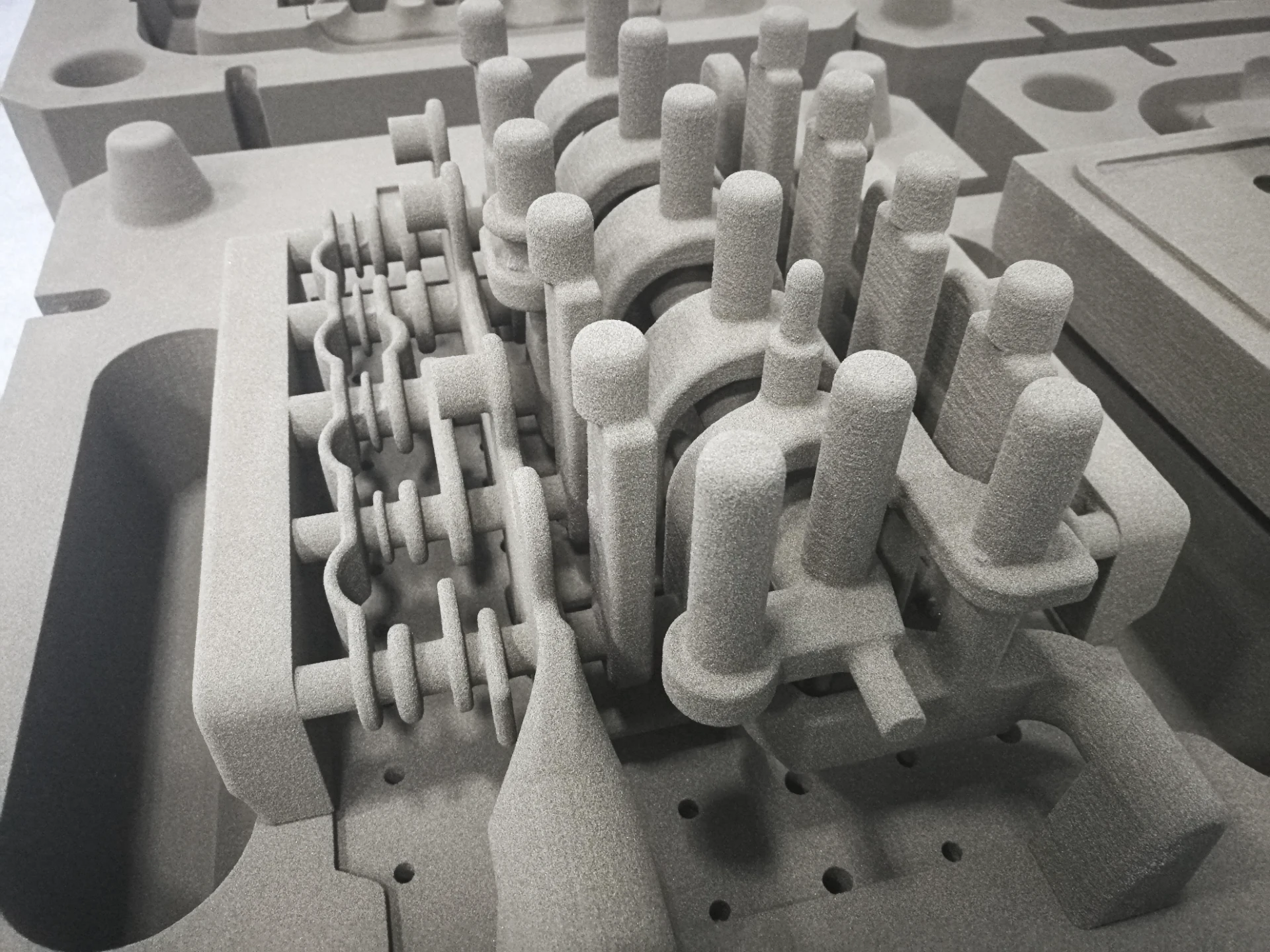
The essence of die casting lies in its ability to produce complex parts with excellent dimensional accuracy at a faster rate than other manufacturing processes. This is primarily due to the use of non-ferrous metals like aluminum, zinc, and magnesium, which offer a harmonious blend of lightweight characteristics and superior strength. From my vantage point as an industry expert, die cast parts have been instrumental in enabling manufacturers to meet the rigorous demands for speed and precision in production timelines.
Consider the automotive industry; die cast components are often praised for reducing vehicle weight without compromising strength, thereby enhancing fuel efficiency. For instance, components such as engine blocks, transmission cases, and even extensive body panels are now often composed of die-cast materials. The meticulous design and the finished surface quality of these components help auto manufacturers maintain their edge in a fiercely competitive market.
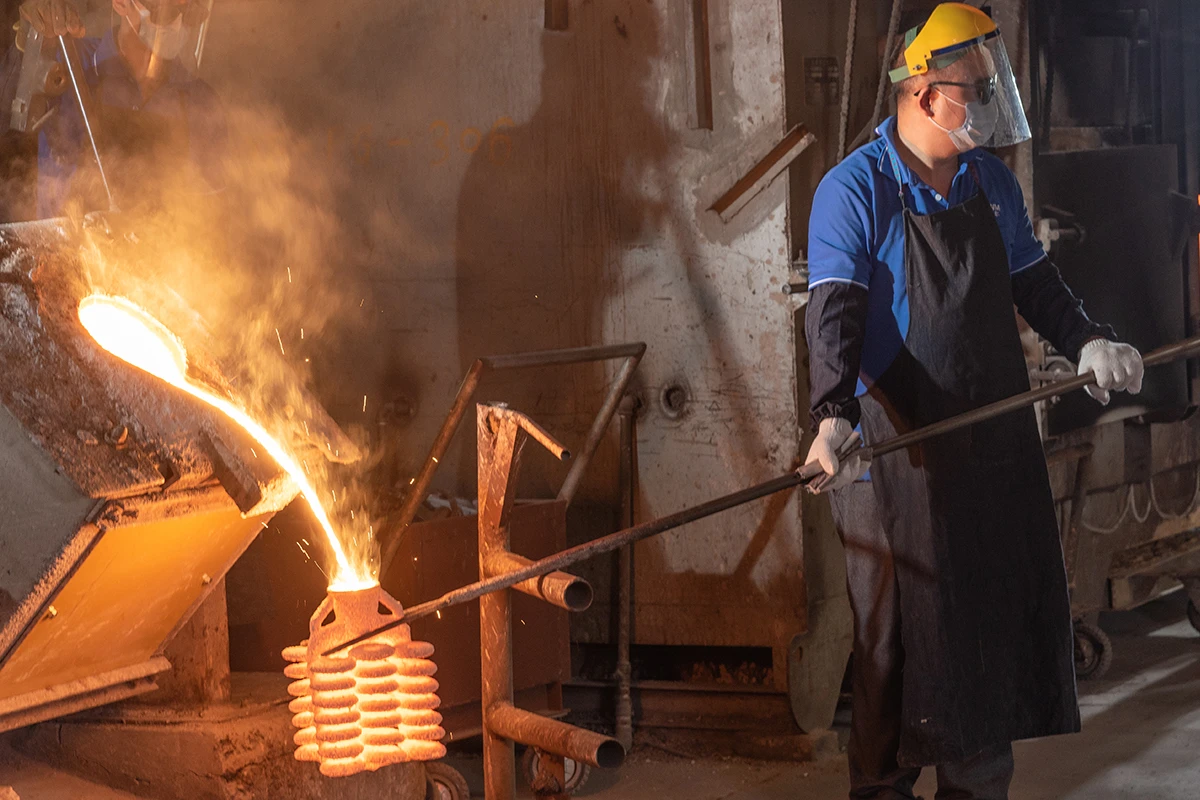
In consumer electronics, die cast parts make their presence known in the durable casings of smartphones, laptops, and cameras. The consistency in quality provided by die casting processes ensures that these products meet both aesthetic and functional standards, which is critical for consumer satisfaction. It is within this domain where my expertise has particularly flourished, having consulted for top-tier electronics firms seeking to optimize their part manufacturing.
die cast part
The authority of die cast parts manufacturing is rooted in its widespread application and the technical advancements it has assimilated over the years. Innovations like vacuum die casting and advanced thermal management techniques have minimized defects such as porosity, which once plagued the industry. As an advocate for continuous improvement, I have often liaised with R&D departments to incorporate cutting-edge technologies that push the boundaries of die casting efficiencies.
Trustworthiness within this sector is anchored in compliance with rigorous testing and quality assurance standards. The ISO certifications many die casting firms hold reflect their commitment to excellence and reliability, ensuring that each component is tested to withstand real-world applications. During my tenure, I have led numerous workshops and training sessions on the importance of maintaining and exceeding these standards, reinforcing trust within the supply chain.
In my professional narrative, die cast parts represent more than just an element of manufacturing; they are a testament to the synergy of art and engineering. With new materials and modern technologies like AI-driven design optimizations on the horizon, the future only seems to promise more precision and performance from the die casting arena.
Through transparency, a commitment to quality, and a continual pursuit of innovation, the die cast industry remains an exemplary model of how traditional manufacturing practices can adapt to meet modern demands—ensuring it retains its relevance and authority in the global market.