Die casting is a precise manufacturing process involving the creation of metal parts by forcing molten metal under high pressure into a mold cavity. The expertise behind this method has enabled manufacturers to produce complex shapes with high levels of repeatability and stunning accuracy. As industries continue to demand more intricately detailed metal parts, understanding the steps in die casting becomes essential for ensuring efficiency, reliability, and top-tier product quality.
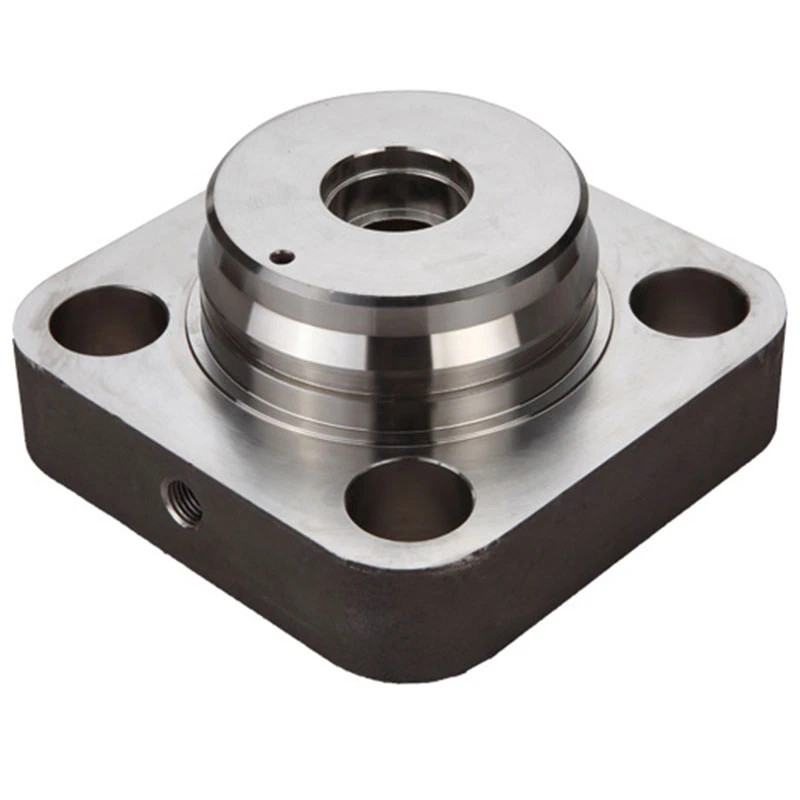
First, the choice of material is crucial. Zinc, aluminum, and magnesium are commonly used due to their excellent mechanical properties. Their lightness, corrosion resistance, and high thermal conductivity make them ideal for a myriad of applications. The selection process involves considering the specific requirements of the final product, such as strength, durability, and weight.
Crafting of the mold, or die, is the next critical step. The die design needs to account for complex geometries, cooling channels, and ejection mechanisms. Made from hardened tool steels, the molds must withstand significant thermal cycling and mechanical stresses. Precision in the mold design translates directly to the precision of the cast part, making this a paramount stage in die casting. Expert mold makers utilize advanced CAD software to simulate the molding process, ensuring minimal defects in the final product.
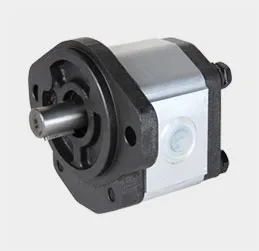
The die casting process itself involves several stages, starting with die preparation. The mold is coated with a lubricant to regulate temperature and assist in the removal of the final cast. The molten metal is then injected into the die under high pressure using specialized machinery. Injection periods are short, usually ranging from milliseconds to a few seconds, which requires meticulous control to ensure the metal completely fills the cavity before solidification. Precise control over injection pressures and speeds is a hallmark of expertise in die casting operations.
Solidification and cooling of the metal occur in the die, which is then followed by the removal of the cast part. This is where the ejection system built into the mold plays a critical role, leveraging pins or plates to release the part without inflicting damage or introducing surface defects. The efficiency of the cooling process impacts the production cycle time and, subsequently, overall costs.
Trimming and finishing come next—the cast parts often have excess material known as flash that needs removal. This is done through various processes including manual trimming, CNC machining, or tumbling, further achieving the product's precise specifications. Additional finishing techniques such as shot blasting, drilling, or tapping may also be employed depending on the product's end-use requirements.
die casting steps
Quality control is intertwined throughout the die casting steps. To establish authority in the industry, a rigorous QA process checks for defects such as porosity, dimensional inaccuracies, and surface blemishes. Advanced inspection techniques like CT scanning and X-ray inspections provide a non-destructive means of verifying internal integrity and are a testament to trustworthiness in die casting expertise.
Trust in die casting companies is built on their commitment to sustainability, highlighting their authoritative position in the market. Sustainable practices, such as recycling metals and using energy-efficient machines, reduce the environmental impact while maintaining product quality. Transparency in these practices enhances the credibility of die casting companies.
In-product application, die-casted parts are present in a myriad of industries from automotive to consumer electronics, each demanding high levels of precision and robustness. The expertise of experienced engineers and the reliability of advanced technologies enable the production of lightweight, yet enduring components which perform under the most demanding conditions.
Innovations continue to propel die casting forward, such as the use of simulation software for optimization, vacuum-assisted dies for reducing porosity, and new alloys that offer superior properties. Staying abreast of these advancements is crucial for maintaining a competitive edge and delivering products that meet the stringent demands of modern applications.
In conclusion, die casting is a refined process requiring deep expertise in material selection, mold design, and post-casting processes. The seamless integration of each step—from injection to finishing—defines the excellence in die casting. By adhering to high standards of quality and striving for continuous improvement, manufacturers not only meet but exceed industry expectations, cementing their authority and trust in a highly competitive market.