Die casting foundries serve as the cornerstone of manufacturing industries, providing crucial components known for their precision, durability, and cost-efficiency. As the demand for complex and intricate metal components continues to rise, these foundries have positioned themselves at the forefront of innovation. With unmatched expertise and cutting-edge technology, die casting foundries offer a myriad of benefits to today's fast-paced industrial landscape.
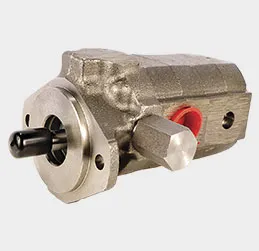
For industries that require high volumes of lightweight and durable metal parts, the expertise offered by die casting foundries is indispensable. These foundries utilize advanced die casting processes to produce components that meet, and often exceed, the rigorous standards set by industries such as automotive, aerospace, and consumer electronics. The use of non-ferrous metals, like aluminum, zinc, and magnesium, ensures that the parts are not only lightweight but also exhibit superior strength-to-weight ratios. This is particularly advantageous in automotive and aerospace sectors, where reducing the weight of components is pivotal for improving fuel efficiency and performance.
A core aspect that underscores the authority of die casting foundries is their commitment to precision engineering. Modern die casting foundries employ state-of-the-art Computer Numerical Control (CNC) machines and automated systems to achieve the highest levels of accuracy. This level of precision is critical for industries where parts need to fit seamlessly into larger mechanical systems. The resultant reduction in the need for post-production machining not only saves cost but also ensures that products are delivered faster, thus reducing time-to-market—a crucial factor in the competitive industrial sector.
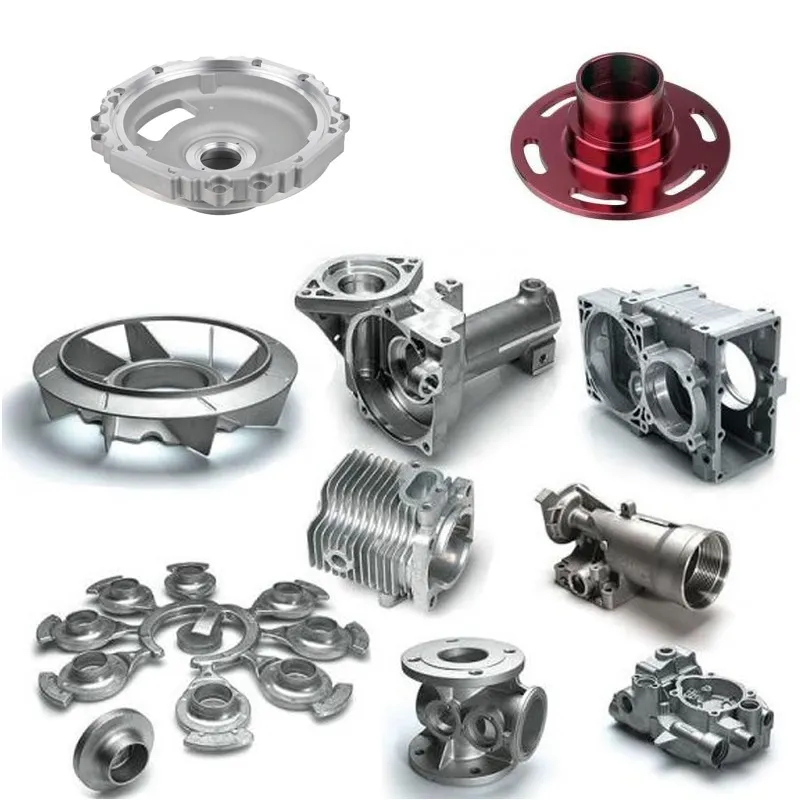
die casting foundry
Trustworthiness stems from a foundry's ability to consistently deliver quality products.
Reputable die casting foundries implement stringent quality control measures at every stage of the production process. From the initial mold design using sophisticated CAD software to the final inspection of cast components, each step is meticulously monitored. This rigorous oversight ensures that each component meets the intended specifications, significantly lowering the risk of defects. Such meticulous attention to detail builds lasting trust with clients, leading to long-term partnerships and repeat business.
Safety and environmental responsibility also play crucial roles in establishing the trustworthiness of a die casting foundry. By adopting eco-friendly practices such as recycling scrap metal and reducing emissions through advanced filtration systems, these foundries commit to sustainable manufacturing. Customers increasingly prefer to work with suppliers who demonstrate environmental stewardship, resulting in a win-win situation for the foundry and its clients.
In conclusion, the success of any industry relying on manufactured metal parts hinges significantly on the expertise and reliability of its die casting foundry. With a blend of innovation, precision, authority, and trust, die casting foundries stand as pivotal partners in the global supply chain. As technological advancements continue to evolve, these foundries are well-equipped to adapt, ensuring that they remain essential, reliable, and efficient sources of high-quality components.