Aluminum sand casting is an indispensable method in the manufacturing industry, revered for its versatility and cost-effectiveness when producing complex metal parts. This process uses non-reusable sand molds to form aluminum, an approach that supports a wide range of design capabilities. However, understanding and adhering to specific tolerances in aluminum sand casting is crucial to ensure both functionality and quality.
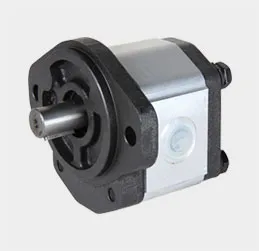
The term “tolerances” in sand casting refers to the permissible limits within which a dimension of a part or mold is allowed to vary. Tolerances are vital as they directly affect the performance, assembly, and interchangeability of parts. Several factors influence these tolerances, necessitating deep expertise and experience to manage them effectively.
The complexity of aluminum sand casting tolerances begins with the choice of sand.
Different types of sand can impact the surface finish and dimensional accuracy. Fine sand might offer excellent surface finishes but may restrict permeability and the easy release of gases, potentially causing defects. Coarser sand may benefit permeability but at the expense of finish detail. Thus, the selected sand type should align with the part's critical tolerances and intended application.
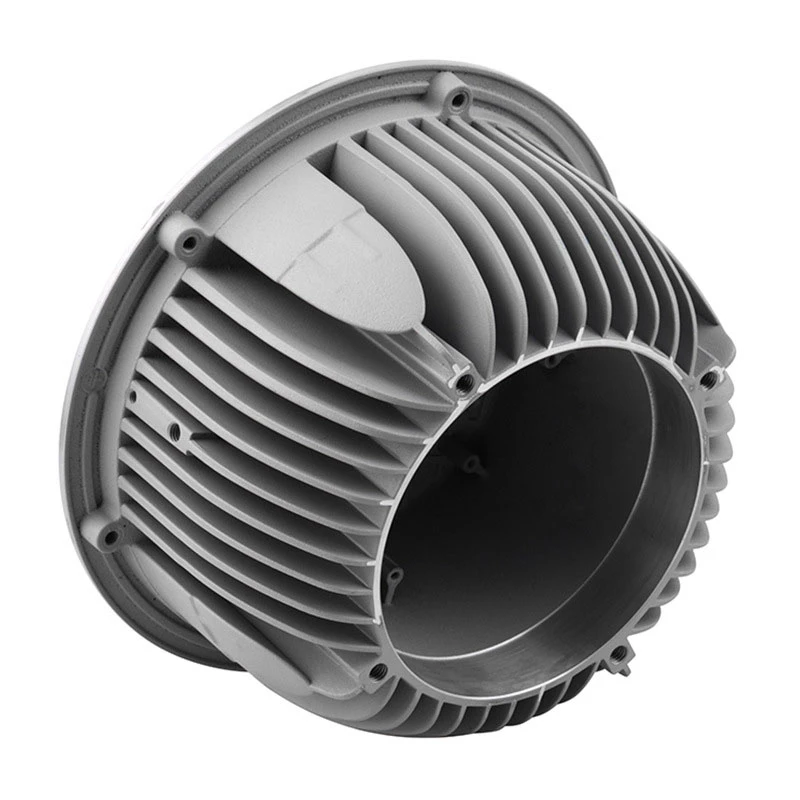
Another critical factor affecting tolerances is the thermal expansion of aluminum during the casting process. As aluminum heats and cools down, it expands and contracts — a phenomenon that must be accommodated in the mold design phase. Experienced professionals use specialized software to simulate thermal effects, ensuring that final part dimensions closely match the design specifications. This thermal consideration is particularly crucial in maintaining uniform wall thickness and preventing warping or distortion.
Precision in tool design also plays a significant role in managing aluminum sand casting tolerances. Tools must be designed to withstand the abrasive nature of sand while maintaining dimensions throughout repeated cycles. These tools include patterns, core boxes, and molds, all crafted with precision engineering to support tight tolerances. Advanced digital modeling and CNC machining are often employed to ensure these tools meet the demanding standards of modern castings.
With regard to gating systems, the layout and design must be carefully orchestrated to ensure proper metal flow and solidification. Poorly designed gating can lead to turbulence, incomplete fills, or shrinkage defects, all influencing dimensional accuracy. Therefore, precise calculations and flow simulations are essential in optimizing gating designs for achieving the desired tolerances.
aluminum sand casting tolerances
Equally important is the expertise in post-casting processes, such as machining, heat treatment, and finishing. These stages can help attain precise tolerances by addressing any deviations experienced during casting. Post-machining, for example, can correct minor dimensional inaccuracies, while heat treating can bolster mechanical properties and relieve internal stresses, improving the structural integrity of the casting.
Furthermore, implementing rigorous inspection and quality control protocols ensures that aluminum sand castings maintain specification adherence. Techniques like coordinate measuring machines (CMM), 3D scanning, and non-destructive testing provide detailed insights into the dimensional conformance and overall quality of the cast piece. These advanced inspection methodologies are critical in identifying and rectifying deviations early in the manufacturing process.
Moreover, the collaboration between design engineers and foundry technicians is paramount to achieving optimal tolerances in aluminum sand casting. Such collaboration fosters the exchange of critical information regarding design intents, casting limitations, and expected performance, ensuring alignment across all production stages.
Finally, maintaining an authoritative stance in aluminum sand casting involves continuous learning and adaptation to new technologies and methods. The integration of AI and IoT devices in monitoring casting conditions and automating adjustments has been instrumental in refining tolerances further. These innovations exemplify the synthesis of traditional craftsmanship with modern technology, enhancing both efficiency and accuracy in sand casting.
In summary, achieving tight aluminum sand casting tolerances demands a holistic understanding of material science, precision engineering, and advanced technology. This multifaceted approach guarantees the production of high-quality components that meet stringent industrial standards, underscoring the relevance and reliability of aluminum sand casting in today's manufacturing landscape.