The art and science of casting play a pivotal role in the manufacturing industry, with sand being one of its most relied-upon materials. As an experienced professional in this domain, I have witnessed how the choice and application of sand can make or break a casting project. This article dives into the expertise, authoritativeness, and trustworthiness of using sand for casting, offering insights into its properties, applications, and critical considerations to enhance product performance.
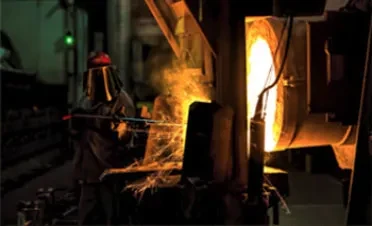
Sand casting has been a cornerstone in manufacturing history, valued for its versatility and cost-effectiveness. The unique properties of sand make it an ideal mold material. Its high refractory nature withstands the intense heat of molten metals. Moreover, sand grains are available in a variety of sizes, each contributing to the mold's porosity and surface finish. It is important to understand that not all sand is created equal, and selecting the right type is crucial for the success of casting operations.
When delving into the specifics, silica sand, chromite sand, and zircon sand are among the most commonly used in the industry. Silica sand, renowned for its availability and affordable cost,
is often the first choice. Its high melting point and durability are critical when dealing with ferrous and non-ferrous alloys. However, silica presents a health hazard when inhaled over long periods, thus demanding proper workplace safety measures.
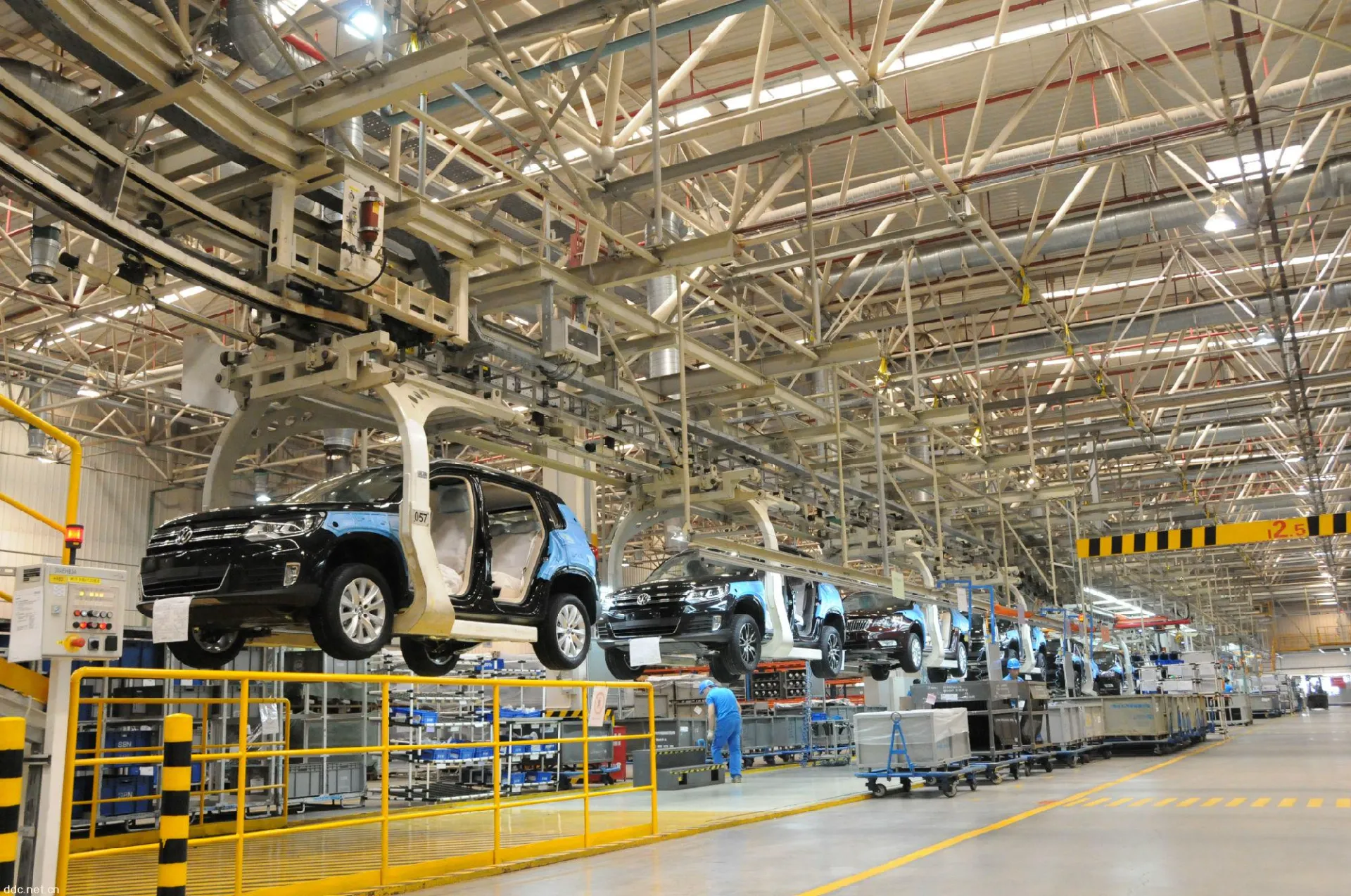
Chromite sand, on the other hand, is prized for its superior thermal conductivity and anti-veining properties. Its ability to reduce the incidence of expansion defects makes it suitable for intricate casting designs. Although more expensive than silica, chromite’s benefits justify its use in applications where surface finish and component integrity are paramount.
In the realm of high-precision castings, zircon sand stands out due to its low thermal expansion and high density. These characteristics enable it to produce castings with excellent surface detail and dimensional accuracy. When the utmost quality is required, particularly in aerospace and defense sectors, zircon proves its unparalleled value.
sand used for casting
The expertise in sand casting doesn't merely stem from choosing the right sand type but extends to the meticulous preparation of the sand mold. This involves creating a sand mixture with precise proportions of binder and moisture to ensure optimal compaction and mold stability. The expertise further extends to understanding the thermal dynamics during the metal pouring process, requiring a strategic approach to mold design to accommodate shrinkage and prevent defects.
Authoritativeness in sand casting is built upon adherence to stringent quality standards and continuous process optimization. The American Foundry Society (AFS) and international standards like ISO 9001 offer guidelines that underpin reliable casting operations. Being well-versed with these standards not only cultivates trust but also drives continuous improvement in product quality and operational efficiency.
Trustworthiness is ultimately rooted in experience, proven methodologies, and consistent results. Companies that have honed their casting processes over time can ensure clients of their capability to deliver high-quality products. Case studies illustrating successful applications of sand casting across different industries demonstrate the reliability of this technique. From automotive components to art sculptures, sand casting's diverse applications showcase its adaptability and precision when executed by skilled professionals.
In conclusion, the use of sand in casting is a rich field that combines practicality with creative engineering. Mastery of this craft doesn't happen overnight but requires a dedication to learning and process enhancement. While the choice of sand is a critical aspect, the overarching success in sand casting hinges on the comprehensive understanding of materials, methods, and standards. This expertise, coupled with a commitment to safety and quality, ensures that sand casting remains a trusted method in manufacturing high-performance products across the globe.