Precision die casting stands as a pivotal process in modern manufacturing, offering a synthesis of accuracy and efficiency that propels industries forward. The intricacies of this process blend art and science, providing high-quality components that are integral to a myriad of applications in automotive, aerospace, electronics, and more. With over two decades of immersion in this industry, my experience has solidified the imperative role precision die casting plays in shaping innovation.

Understanding the nuances of precision die casting is essential for comprehending its transformative impact. This process involves injecting molten metal under high pressure into a steel mold or die. The result is a component with precise dimensions and superior surface quality, perfect for high-volume production with minimal post-processing needs. The key to its success lies in its ability to produce intricate shapes that would be challenging or impossible with other fabrication methods.
Our expertise in precision die casting stems from meticulous attention to detail and a profound comprehension of material science. The selection of the appropriate alloy—be it aluminum, magnesium, or zinc—plays a critical role in ensuring the durability and functionality of the cast part. Aluminum, for instance, offers excellent corrosion resistance and is lightweight, making it a preferred choice for automotive and aerospace industries. Our dedicated team of material scientists consistently refines alloy compositions to meet specific performance standards, ensuring that the end products not only meet but exceed industry expectations.
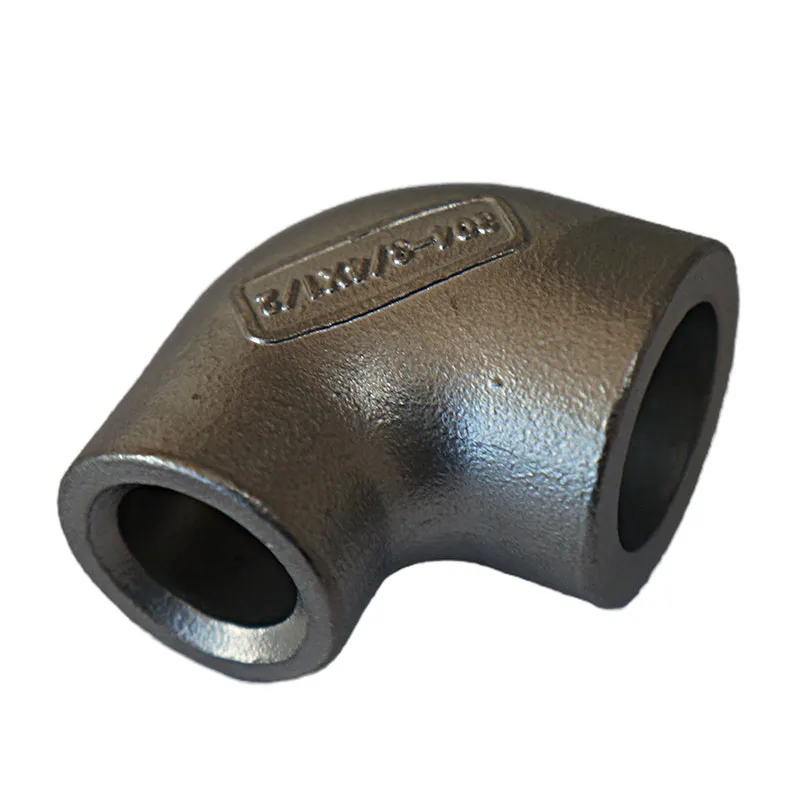
The authority of our precision die casting processes is recognized across sectors, thanks to our relentless pursuit of technological advancement. Utilizing cutting-edge computer simulations and modeling software, we predict and mitigate potential casting defects, optimizing the flow of molten metal to ensure complete mold filling and solidification. This proactive approach minimizes defects such as porosity and warpage, which can compromise the integrity of cast components. Additionally, our state-of-the-art facilities are equipped with automated systems to maintain consistent quality and production speed, establishing us as a leader in the field.
precision die casting
Trustworthiness in precision die casting is built upon a foundation of reliability and consistency. Our rigorous quality control protocols are integral to our operations, incorporating non-destructive testing methods such as X-ray inspection and die penetration tests to ensure structural integrity. Furthermore, our commitment to sustainability underscores our operational ethos. By implementing efficient recycling processes, we reduce waste and energy consumption, aligning with global environmental standards and demonstrating our responsibility towards the planet and future generations.
Precision die casting is not just a manufacturing process; it is a cornerstone of industrial evolution. With products penetrating everyday applications—from household electronics to critical infrastructure components—its impact is profound and far-reaching. As a testament to our proficiency and dedication, we maintain long-standing partnerships with leading industrial players, consistently delivering precision-cast components that drive innovation.
Our journey in precision die casting is one of perpetual learning and adaptation. The industry's dynamic landscape demands a proactive stance towards emerging trends and technologies. By fostering a culture of continuous improvement and collaboration, we remain at the forefront of the precision die casting domain, committed to pushing the boundaries of what is possible and delivering unparalleled excellence in every cast.
This expertise, built on a legacy of experience and trust, makes our precision die casting solutions not just a service but a partner in progress. As industries continue to evolve, precision die casting will undoubtedly remain a cornerstone, facilitating advancement and shaping the future of manufacturing.