Investment casting sand, often heralded as a pivotal component in the precision casting industry, is more than just a granular material—it's the cornerstone that supports the entire casting process. This article delves into the nuanced intricacies of investment casting sand, drawing from extensive industry expertise to underscore its indispensable role.
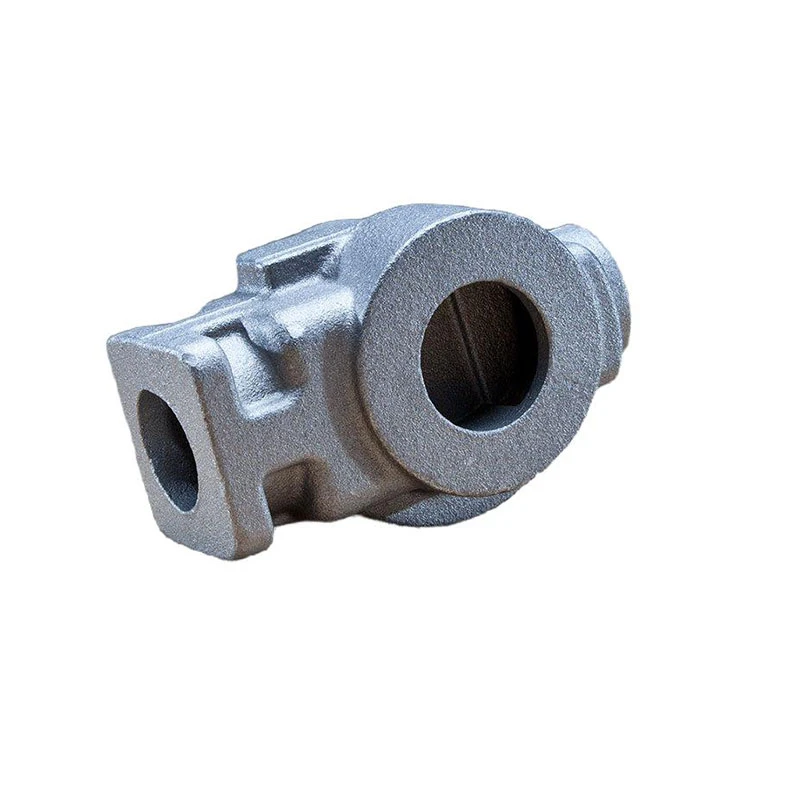
At its core, investment casting sand is employed in the creation of molds that can withstand high temperatures while ensuring exact replicas of intricate designs. This capability is crucial in industries where precision is paramount, such as aerospace, automotive, and medical devices manufacturing. The quality of the sand directly influences the surface finish, tolerance, and even the internal integrity of the final product.
Manufacturers who prioritize high-quality investment casting sand often enjoy a competitive edge.
The reason is simple superior sand leads to superior casts. When discussing the characteristics that define top-tier investment casting sand, grain size and thermal stability emerge as critical factors. Uniform grain size ensures a smooth surface finish, reducing the need for further machining and finishing processes. Furthermore, thermal stability is essential to prevent the sand from breaking down or altering its properties at high temperatures, which can compromise the casting's dimensional accuracy.
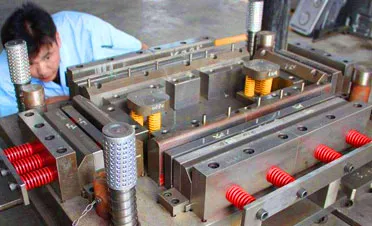
The origin of the sand cannot be overlooked. Silica-based sands have been traditionally favored due to their abundance and cost-effectiveness. However, innovations in the field have led to the exploration of alternative materials such as zircon and chromite sands. These alternatives boast higher refractory capabilities, making them suitable for casting high-melting-point alloys which are increasingly common in modern applications. Decision-makers in the field must weigh the cost implications against the potential for improved performance and reduced defects.
In practice, selection and testing of investment casting sand are areas where expertise and experience significantly impact outcomes. Documented case studies reveal instances where minute deviations in sand properties have led to significant quality issues in final products. Thus, investing in state-of-the-art testing facilities and hiring experienced materials engineers can be a game-changer for casting operations. Conducting thorough assessments of sand’s chemical composition, grain fineness, and moisture content before usage is not just recommended—it's imperative.
investment casting sand
Furthermore, environmental considerations are gaining prominence in the discussion of investment casting sand. The industry is under increasing pressure to manage waste and optimize the lifecycle of consumption. Innovations are underway to recycle spent sand, reducing environmental impact and offering potential cost savings. Collaborative research with academic institutions has been instrumental in advancing sustainable practices, developing new binders, and regenerating used sand to near-new quality.
Networking across industry forums and engaging with developments in standards and regulations also foster deeper trust with clients and stakeholders. For instance, adherence to ISO standards in sand selection and process control distinguishes a casting operation as authoritative and trustworthy.
Those who attend to these myriad factors find themselves not only adept at navigating challenges but poised to leverage opportunities unique to investment casting sand. Continual learning, embracing new technologies, and fostering partnerships with suppliers who demonstrate consistent quality and reliability are strategic imperatives. Planting the seeds of innovation within the foundry itself can often yield the highest dividends automated systems for sand handling and conditioning can reduce labor costs and increase process reliability.
Ultimately, mastering the complexities of investment casting sand is tantamount to mastering the casting process itself. It ensures the creation of high-quality components that meet rigorous specifications—a mission-critical goal for manufacturers aspiring to lead in precision-driven sectors. Through meticulous selection, ongoing education, and strategic foresight, businesses can transform this foundational material into an asset that drives success and reinforces industry leadership.