The significance of draft angle in die casting is often underestimated, yet it plays a pivotal role in ensuring the quality and functionality of cast components. A well-considered draft angle enhances product quality, reduces manufacturing costs, and prolongs the lifespan of the dies.
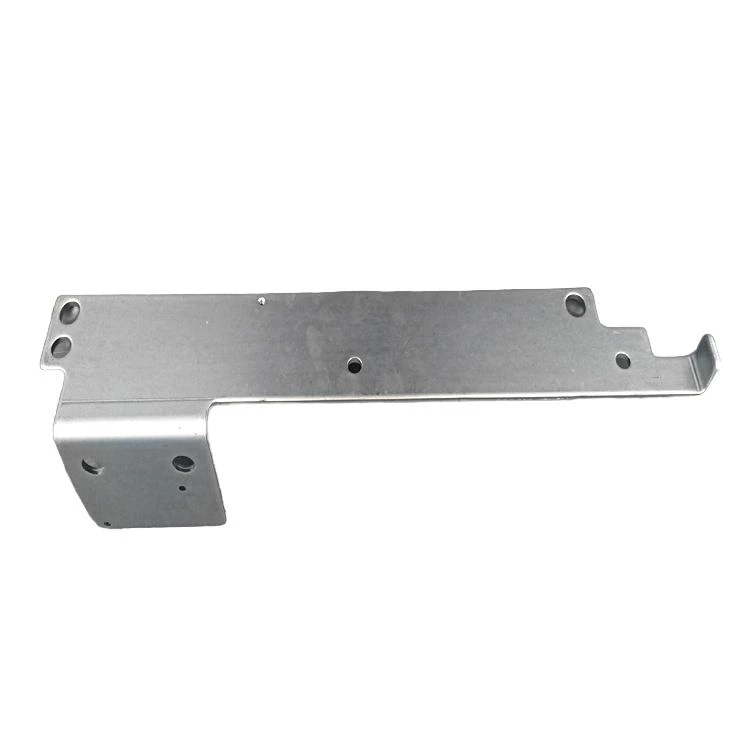
Draft angle refers to the taper applied to the vertical surfaces of the mold cavities in die casting. This taper, typically measured in degrees, facilitates the ejection of the part from the die without causing damage to the part or the mold. When a component lacks sufficient draft, it can lead to challenges such as part sticking, increased wear on the die, and surface defects in the final product.
From an expertise standpoint, the ideal draft angle largely depends on the complexity of the part design, the type of metal being cast, and the specific requirements of the product. Generally,
a draft angle of 1 to 3 degrees is recommended for most die-cast components. However, in high detail or deep cavity areas, angles might need to be adjusted to ensure smooth ejection and maintain part integrity.

Empirical experience demonstrates that optimizing draft angle can significantly enhance production efficiency. For instance, a company engaged in the production of aluminum automotive parts observed a 30% reduction in cycle time by adjusting their draft angles based on a comprehensive analysis of their die-wear patterns. This not only expedited their production line but also minimized the frequency of die maintenance and retooling.
draft angle for die casting
In terms of authoritativeness, design engineers and manufacturers should consult with material scientists and metallurgists to tailor the draft angles to the metal’s properties. Different alloys respond distinctively to casting processes, and as such, require specific draft angle considerations. Aluminum, for example, might demand different draft specifications compared to zinc or magnesium, owing to its thermal expansion characteristics and cooling behavior.
Trustworthiness in die casting is bolstered by adhering to established industry standards and protocols. Utilizing computer-aided design (CAD) software and simulation technologies, such as finite element analysis (FEA), can predict potential issues related to draft angles even before the die is created. This preemptive approach ensures that the design adheres to quality assurance parameters, thereby reducing the risk of defects and bolstering trust in the manufacturing process.
Moreover, consistent collaboration between die designers, product engineers, and quality control teams ensures that the draft angle is not only ideal for manufacturing efficiency but also meets the aesthetic and functional specifications of the product. This collaborative approach fosters a sense of reliability and trust as adjustments can be swiftly made to address any emerging issues observed in the initial production runs.
In conclusion, draft angle optimization is a cornerstone of efficient die casting, enhancing the overall quality and durability of manufactured parts. Professionals in the field must leverage their experience and expertise to define appropriate draft angles, supported by authoritative industry standards and practices. By doing so, they establish a trustworthy process that guarantees high-quality outcomes and satisfies the intricate demands of modern product designs.