Die casting is a pivotal manufacturing process that requires precision and expertise to produce high-quality metal parts. Despite its complexity, following the right guidelines can optimize productivity and ensure superior results. Drawing from decades of industry experience, this article delves into essential die casting guidelines, reflecting a blend of expertise and authoritative knowledge that can be trusted by professionals seeking to hone their craft.
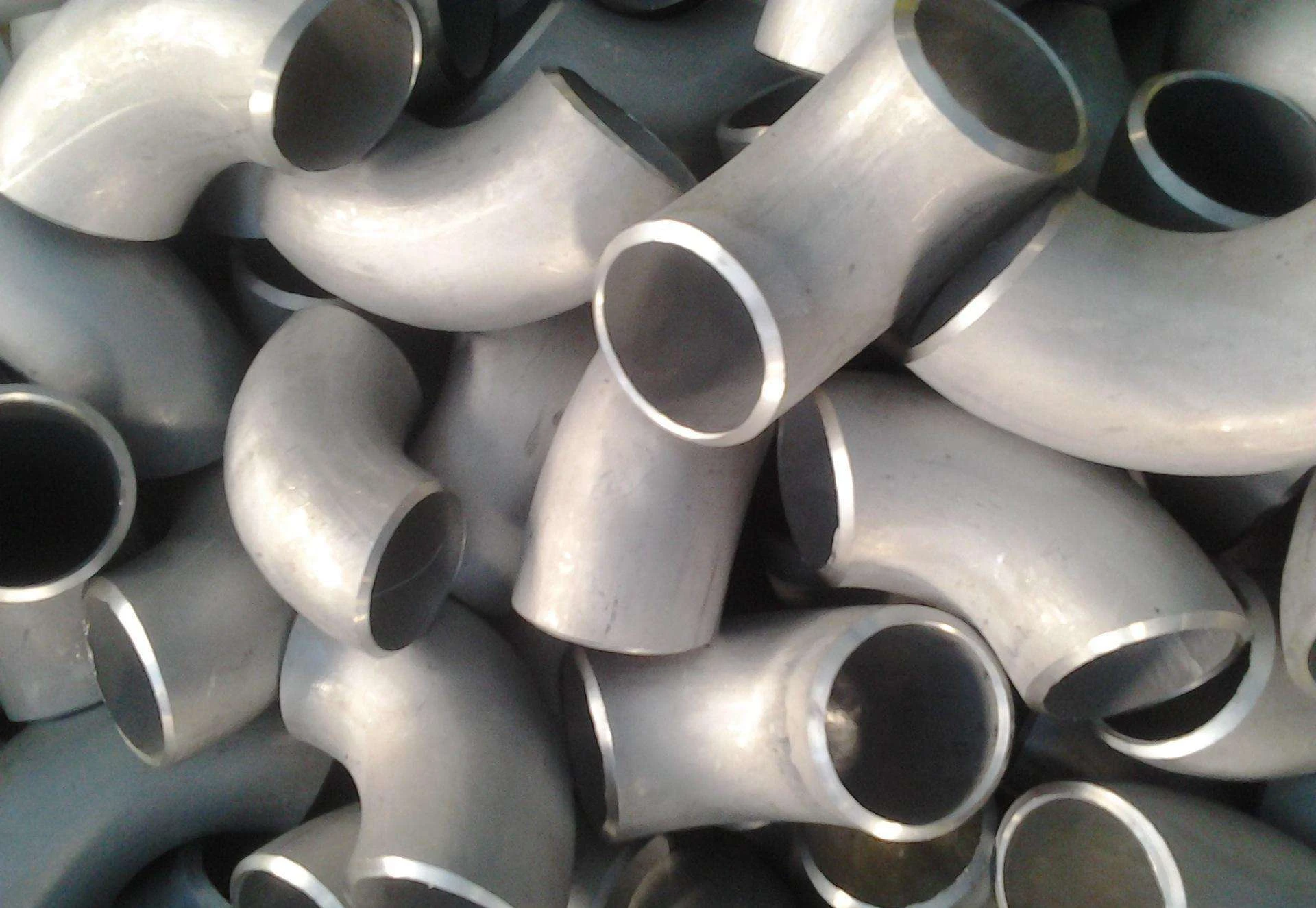
Central to the success of die casting operations is the selection of appropriate materials. It is imperative to select alloys tailored to the specific application needs. For instance, aluminum and magnesium are preferred for their lightweight characteristics and corrosion resistance, while zinc is chosen for its strength and ease of casting. Understanding the properties of each metal can significantly influence product performance and lifespan, thereby valuing expertise rooted in metallurgical science.
Equally important is the design of the die. The die must be crafted to accommodate shrinkage and thermal expansion, aspects inherent to metal solidification. An expertly designed die minimizes defects such as porosity and warping, ensuring that precision and consistency are maintained across production runs. Experience shows that employing computer-aided design (CAD) software facilitates the creation of detailed and accurate die designs, ultimately leading to improved uniformity in the final products.
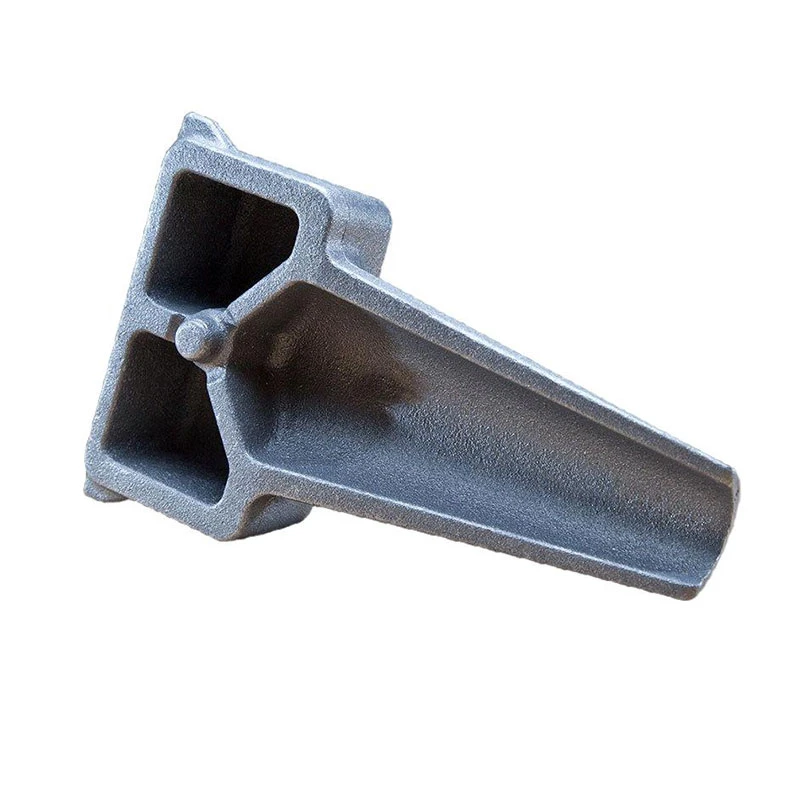
Process parameters, including temperature and pressure, are critical elements that demand precise control. Optimal temperatures for melting and injection must be maintained to ensure metal fluidity while preventing rapid cooling that could lead to defects. Pressure parameters must be calibrated to achieve complete die filling without causing flashing. Trustworthy processes often incorporate advanced control systems to monitor these parameters in real-time, thereby enhancing process reliability and product quality.
Furthermore, implementing a robust quality control regime is indispensable. Regular inspections and testing—such as X-ray radiography and surface integrity assessments—are essential to detect and address any inconsistencies early in the production cycle. These measures, grounded in authoritative industrial standards, not only uphold quality but also foster customer trust and satisfaction in the final product.
die casting guidelines
Post-casting treatment, including heat treatment and surface finishing, can further enhance the mechanical properties and aesthetic appeal of die-cast parts. Heat treatment can improve hardness and fatigue resistance, while surface treatments like anodizing can bolster corrosion resistance. These treatments are best prescribed based on the specific performance requirements of the product, underscoring the importance of expert recommendations in optimizing product function.
In addition, a keen focus on environmental and safety protocols cannot be overstated. Ensuring compliance with environmental regulations helps maintain ecological balance while simultaneously promoting a safe working environment. Implementing sustainable practices—such as recycling scrap metal and using eco-friendly lubricants—reflects a commitment to responsible manufacturing, thereby reinforcing corporate reputation and trustworthiness in the marketplace.
The role of continuous improvement cannot be ignored. Investing in ongoing training and staying abreast of technological advancements in die casting equipment can lead to enhancements in efficiency and product innovation. Fostering a culture of constant learning and adaptation keeps the operations at the forefront of industry breakthroughs.
In summation, mastering die casting is a journey requiring a careful balance of material selection, precise design, parameter control, quality assurance, and environmental stewardship. By adhering to these guidelines with diligence and integrity, manufacturers can produce parts that not only meet but exceed the expectations of quality and performance, positioning themselves as leaders in the field.