Aluminium die casting is a paramount manufacturing process in the modern industrial age, serving a wide spectrum of applications where precision and durability are critical. Proper understanding and implementation of aluminium die casting tolerance standards can significantly influence the quality and functionality of the final product. Few manufacturers grasp the intricate relationship among tooling, process parameters, and material properties required to achieve stringent standards. Here's a dive into the nuances of aluminium die casting tolerances, underpinned by extensive experience and dedicated to providing expert insights.
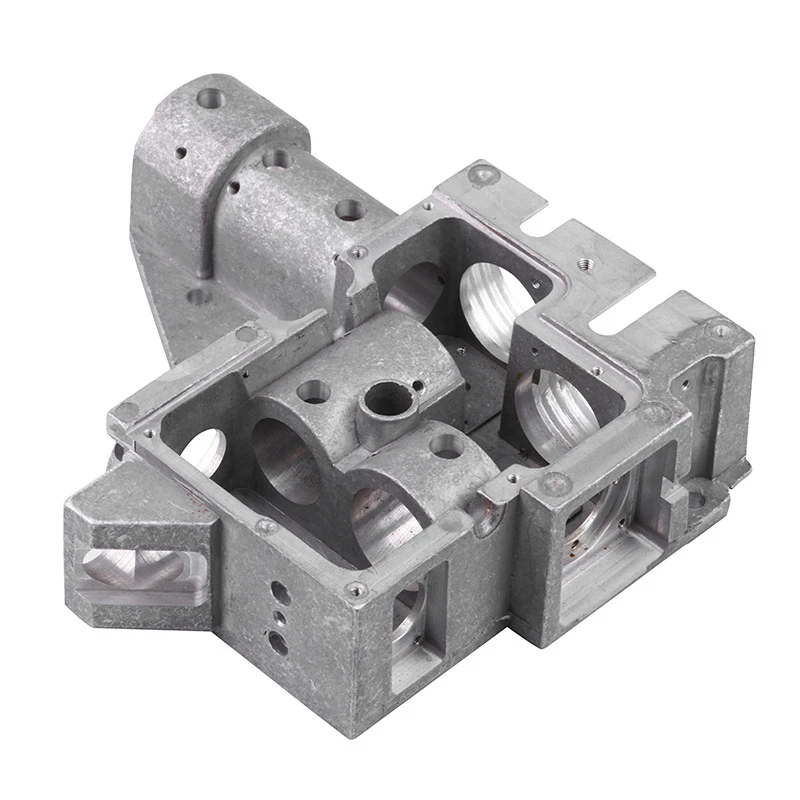
In the world of aluminium die casting, achieving the desired tolerance is a combination of art and science. Experienced manufacturers know that achieving a balance between the design requirements and the manufacturing capabilities is essential. Aluminium die casting utilizes a mold cavity to shape molten aluminium into the desired form. Due to aluminium's relatively low melting point and high fluidity, intricate shapes with tight tolerances can be achieved, but this requires sophisticated tooling and precision control of the casting process from start to finish.
The standard tolerances for aluminium die casting are a reflection of both the material's characteristics and the precision of the casting process itself. Typically, general tolerance levels are classified into several grades, which may range from high precision to more general applications. Each tolerance grade corresponds to a different level of accuracy and is influenced by factors like part size, geometry, and function.
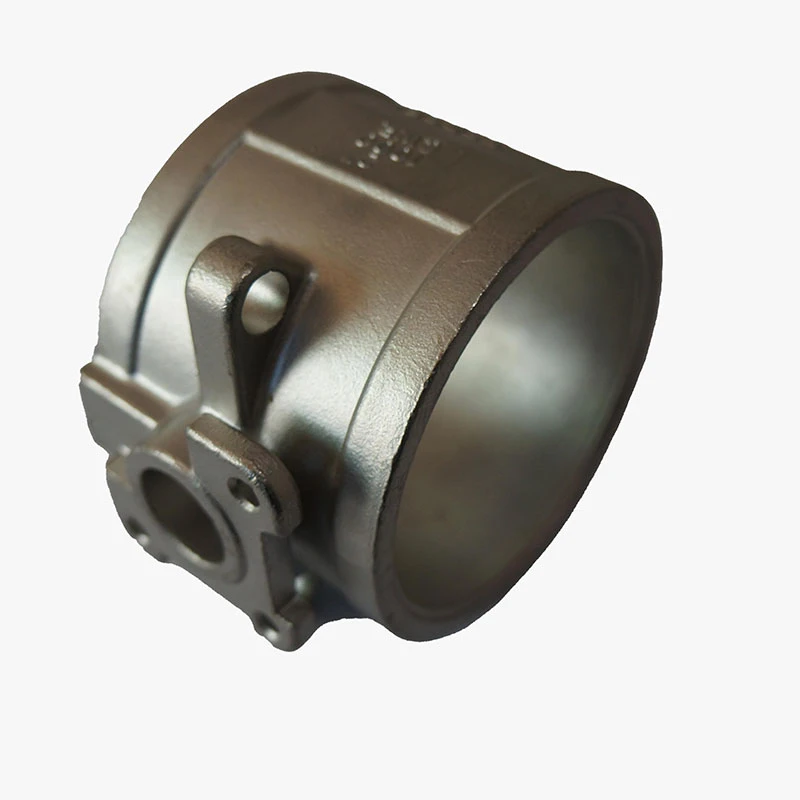
Tooling plays a crucial role in achieving optimal tolerances. The design of the mold must account for the thermal expansion and contraction of both the aluminium material and the steel mold itself. An in-depth understanding of thermal dynamics and material science becomes imperative for minimizing dimensional variances. Furthermore, the use of Computer-Aided Design (CAD) and Computer-Aided Manufacturing (CAM) systems has streamlined mold design, allowing for enhanced precision that aligns with tight tolerance requirements.
Another influential factor is the quality control process implemented during and after casting. With advancements in technology, real-time monitoring systems can detect and correct deviations from optimal temperatures, pressures, or cooling rates, thereby mitigating issues that could lead to tolerance failures. Furthermore, post-casting evaluations, including Coordinate Measuring Machines (CMM) inspections and metallurgical analyses, add layers of reliability by verifying that each part conforms to the specified standards.
aluminium die casting tolerance standard
Material selection is equally influential. Aluminium alloys vary greatly in terms of mechanical properties and workability. Selecting the suitable alloy should be guided by the specific application requirements and the dimensional precision desired. Experienced professionals often recommend alloys that offer a harmonious balance of strength, ductility, and corrosion resistance while maintaining tight tolerances during the casting process.
Engaging the expertise of a seasoned aluminium die casting supplier is indispensable. A supplier with an established track record brings a knowledge base that even state-of-the-art equipment cannot compensate for. Their expertise ensures that all phases of die casting production—from initial concept to final production—adhere strictly to the required standards. They can anticipate potential issues based on historical data and industry trends, providing proactive solutions that maintain product integrity and functionality.
Finally, transparency and documentation are core components of building trust in the aluminium die casting process. Allowing clients access to detailed production reports, tolerance verification documents, and strategic project management insights instills confidence. When a manufacturer openly shares its operations and evaluation methods, it not only underscored its capability to meet standards but also enhances trustworthiness in the client-manufacturer relationship.
In conclusion, aluminium die casting tolerance standards are the culmination of detailed engineering, cutting-edge technology, and dedicated craftsmanship. As demand for high-quality and precise aluminium components grows, emphasis on adhering to, and even exceeding, these standards becomes the yardstick by which reliability and excellence are measured. Manufacturers that prioritize expertise, transparency, and continued innovation solidify their status as leaders in this pivotal field.