Sand casting, a time-honored metalworking process, remains a cornerstone in manufacturing, offering unmatched versatility among its peers. This ancient yet continuously evolving technique holds its ground by catering to both the industrial giants and the bespoke artisans of today's market.
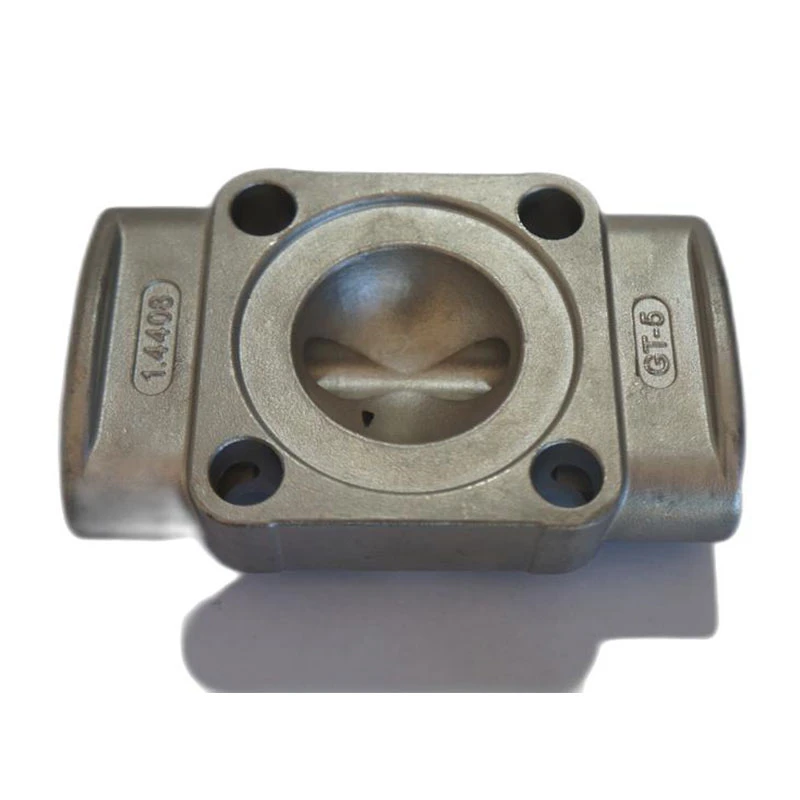
The process begins with the creation of a pattern--a model of the desired final product--typically crafted from wood, metal, or plastic. This pattern is then pressed into sand that has been tightly packed in a mold box, creating a precise cavity. This cavity represents the external shape of the finished artifact. The sands used are usually mixed with clay and other bonding agents, which enhance the retention of the cavity’s shape.
One of the principal advantages of sand casting is its capacity to produce large and intricate shapes. Whether it's the complexity required for a sophisticated automotive engine block or the sheer size of a monumental art sculpture, sand casting accommodates designs that would be prohibitively difficult through alternative methods like die casting or permanent mold casting.
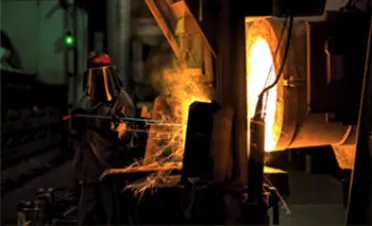
Sand casting's expertise is further demonstrated in its ability to facilitate the seamless use of a wide range of metal alloys. Metals such as aluminum, cast iron, steel, brass, bronze, magnesium, and zinc can all be effectively cast, as the method tolerates high heat and cooling rates. This flexibility permits manufacturers to choose metals specifically tailored to the functional and aesthetic needs of their products--from lightweight aluminum for aerospace applications to the more massive bronze for traditional bells.
sand casting metal
Experience across generations of foundry workers and engineers contributes to the refinement of the sand casting process, navigating its challenges with both traditional wisdom and modern technology. Today’s experts incorporate computer-aided design (CAD) for pattern creation, leading to enhanced precision and reduced material waste. Furthermore,
simulations can predict potential defects, optimizing mold design before metal ever touches sand. This integration of experience and technology elevates sand casting’s effectiveness, ensuring quality and minimizing costs.
From the perspective of authoritativeness, the adoption of sand casting spans countless industries and applications, underpinning its critical role in sectors such as automotive, aerospace, marine, and heavy machinery manufacturing. Renowned educational institutions continue to conduct research and technological trials to push the boundaries of this venerable technique, ensuring that it remains atop the list for prototyping and production.
The trustworthiness of sand casting is built on centuries of reliability and the familiar sound of products that stand the test of time. Discerning engineers opt for sand casting when seeking cost-effective solutions without compromising on quality. The predictability in the outcome reinforces the decision-making process for large-scale manufacturers, knowing they can consistently meet their specifications and timeframe.
In conclusion, sand casting endures as a vital tool in the production industry, skillfully molding intricate, durable, and varied metal objects with confidence. Its strategic balancing of tradition with innovation underscores its high value in current and future manufacturing landscapes. Manufacturers and artisans alike continue to trust in its unyielding capabilities, knowing that with sand casting, they can mold their vision into reality with precision and ease.