High precision investment casting stands at the forefront of modern manufacturing, providing solutions that meet the most stringent specifications in a myriad of industries. This sophisticated technique, known for producing high-quality metal components, is revered for its ability to execute complex geometries with exceptional accuracy and surface finish. Over the years, businesses across aerospace, medical, automotive, and defense sectors have increasingly turned to high precision investment casting to fulfill their demanding requirements.
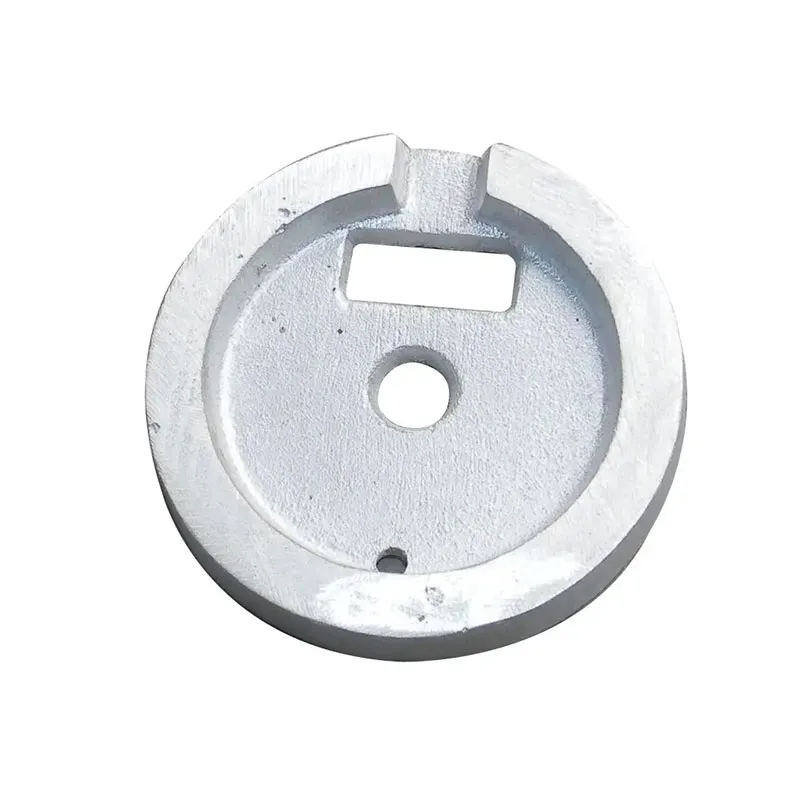
Investment casting, also renowned for its preeminent reliability, leverages a wax pattern to create a custom mold. This wax pattern is crafted with meticulous attention to detail, reflecting the exact dimensional requirements of the intended metal component. Through a process known as lost-wax casting, the investment casting process achieves unparalleled precision by investing this wax pattern in a ceramic shell. Once the ceramic has set, the wax is melted away, leaving a cavity that is subsequently filled with molten metal. The result is a cast metal part that captures every intricacy and nuance of the original design.
From an experiential standpoint, the high precision investment casting process offers flexibility in material selection. Metals and alloys such as stainless steels, carbon steels, aluminum, bronze, and superalloys are commonly used. This diverse range allows engineers and designers to choose materials based on specific mechanical properties, corrosion resistance, and thermal stability required for their application. The adaptability of the process accommodates both ferrous and non-ferrous metals, thus addressing a wide array of engineering challenges.

The expertise invested in high precision investment casting becomes apparent in its capacity to handle near net shape production. Traditional manufacturing techniques like machining often result in substantial material waste; however, investment casting minimizes excess material usage, leading to significant cost savings. By achieving dimensional accuracy and excellent surface finishes directly out of the mold, the need for secondary machining or extensive finishing operations is drastically reduced. This efficient use of materials not only contributes to economic viability but also supports sustainable manufacturing practices.
As industries push the boundaries of technological advancements, the authoritativeness of high precision investment casting becomes particularly prominent. In aerospace applications, where safety and performance are non-negotiable, the method is indispensable. Components such as turbine blades, structural airframe parts, and engine shells benefit from the stringent tolerances achievable through investment casting. Similarly, the medical sector demands components with flawless precision, such as orthopedic implants and surgical instruments, where even minute discrepancies can affect functionality and patient outcomes.
high precision investment casting
Building trustworthiness within high precision investment casting entails establishing rigorous quality assurance protocols. Leading foundries employ state-of-the-art testing and inspection methods to ensure that each component meets the highest standards. Techniques such as non-destructive testing (NDT), X-ray analysis, and 3D scanning are routinely used to verify the integrity and dimensional accuracy of castings. Comprehensive traceability from raw material procurement to final inspection adds another layer of dependability, ensuring that every component delivered is consistent and dependable.
Furthermore, collaboration between investment casting experts and design engineers can yield enhanced outcomes through design for manufacturability (DFM) practices. Understanding the nuances of casting production allows for optimization in component design, reducing potential risks during the casting process and improving the overall success of the project. By working closely in the early stages of design, manufacturers can circumvent potential issues and streamline the journey from concept to final product.
Sustainable innovation remains a cornerstone of high precision investment casting. The ongoing development of more efficient kiln processes, reusable wax patterns, and refined ceramic materials continues to push the boundaries of this esteemed manufacturing technique. As industry standards evolve, investment casting remains committed to reducing environmental impact while simultaneously enhancing the capabilities and characteristics of its output.
In conclusion, high precision investment casting stands as a beacon of sophistication in manufacturing. Its unparalleled ability to produce intricate, high-quality components with precise tolerances and excellent surface finishes is unmatched by other methods. By combining experiential insights, technical expertise, industry authority, and steadfast trustworthiness, investment casting not only meets but often exceeds the expectations of demanding industries. Its future-oriented innovations and environmentally-conscious practices ensure it will remain a vital component of modern engineering for years to come.