Green sand metal casting stands as a cornerstone of modern manufacturing processes, offering unparalleled efficiency and versatility across myriad applications. Rooted deeply in tradition yet continually evolving through technological advancements, this process harmonizes time-honored techniques with state-of-the-art innovations to create superior metal components that power industries worldwide.
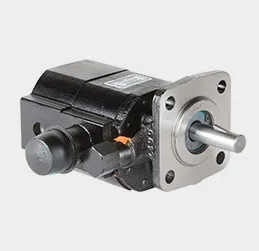
Green sand casting predominantly utilizes silica sand, clay, water, and other additives to form a pliable, yet stable mold known as 'green' because of its ungelled, or uncured, form. Despite the simplicity of its basic materials, the sophistication of the process lies in the meticulous control of every variable, from sand grain size to moisture content. The balance achieved in this matrix directly influences the quality and precision of the metal cast, requiring skilled expertise to maintain optimal conditions.
In the sphere of metallurgy, the expertise involved in green sand casting extends beyond simple mold preparation to encompass the entire lifecycle of the casting operation. An experienced foundry engineer will understand the intricacies of thermal dynamics as they guide the molten metal into the mold cavity. The choice of pouring temperature is critical; too high, and the risks of sand burn-on or excessive mold wear increase; too low, and incomplete filling or cold shuts may occur, both compromising the structural integrity of the final product.
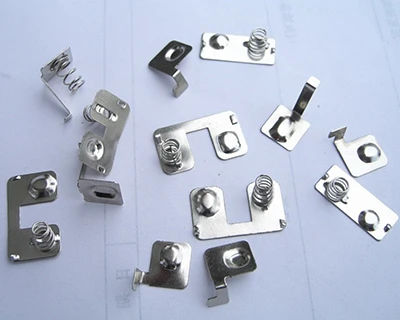
Industries spanning automotive, aerospace, and heavy machinery sectors frequently rely on green sand casting due to its cost-effectiveness and adaptability. Its authoritative presence in manufacturing is further bolstered by the broad range of metals and alloys it accommodates, from ferrous alloys like iron and steel to non-ferrous materials such as aluminum and brass. This versatility ensures that green sand casting remains a trusted process, even as it adapts to the demands of hybrid and lightweight metal projects.
green sand metal casting
Trustworthiness in green sand casting comes from a combination of rigorous quality control and consistent performance. Foundries employ advanced simulation software to predict mold behavior, thermal exchange, and metal flow, reducing the incidence of defects before the first pour even occurs. Moreover, exhaustive testing protocols, including dimensional inspections and x-ray analyses, are implemented post-casting to verify the material properties and compliance with specifications. These practices build confidence among manufacturers and end-users, underscoring the reliability of components produced via green sand casting.
Yet,
the evolutionary path of green sand casting is not without its challenges. Environmental considerations and sustainability are becoming increasingly important in its application. Innovations such as organic binders and sand reclamation systems are being integrated to reduce ecological footprints and improve recyclability. Expertise in these areas is critical, as the successful implementation of greener techniques requires a robust understanding of material science and environmental engineering.
As a process steeped in both historical significance and modern innovation, green sand metal casting's continued relevance depends on its ability to merge tradition with newfound approaches. The authoritative role it plays within the production landscape underscores its adaptability and enduring value. Manufacturers seeking robust, reliable solutions for metal casting should look no further than this proven technique, trusting in its established methodologies and expert-led advancements to meet their transformative goals.
In conclusion, the depth of experience, expertise, and trust that green sand metal casting offers makes it an indispensable tool in the production arsenal. Its authoritative technique guarantees that regardless of industry shifts or technological progress, green sand casting remains at the forefront of innovation, reinforcing its standing as a premier choice for crafting durable, high-performance metal components.