Gray iron sand casting is an essential process in the manufacturing landscape, offering unmatched benefits for producing robust and wear-resistant components. As one delves deeper into this intricate field, the fusion of historical craftsmanship with modern technology becomes evident, allowing industries to harness its full potential.

Gray iron, known for its graphite-rich composition, is traditionally favored for its excellent machinability and high damping capability. These graphite flakes give gray iron its characteristic appearance and endow it with superior thermal conductivity. This makes it an ideal choice for components subjected to dynamic loads or those requiring precision machining.
The sand casting process, a timeless method, is central to the production of gray iron components.
It begins with creating a mold from sand mixed with a binding agent. This mold is carefully shaped to the desired dimensions, ensuring accurate replication of intricate details and complex geometries. What sets sand casting apart is its versatility and cost-effectiveness, particularly suited for medium to large-scale productions.
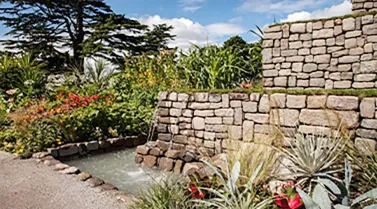
Experience in gray iron sand casting reveals that the choice of sand quality plays a pivotal role. High-quality sand ensures the mold's stability under the thermal and mechanical stresses of casting. Moreover, the expertise lies in selecting the appropriate sand particle size and composition, which directly impacts the surface finish of the final product. Seasoned foundries often have proprietary blends that enhance mold permeability and reduce casting defects.
Expertise in the field is illustrated by optimizing pouring temperature and time. Gray iron's unique properties demand precise control over the molten metal's temperature. Too hot, and it may lead to unwanted microstructural changes; too cold, and it risks incomplete mold filling. Professional foundries employ advanced thermal analysis and non-destructive testing techniques to refine this balancing act, ensuring that each casting meets stringent specifications.
gray iron sand casting
The authoritativeness of a manufacturer in gray iron sand casting is largely established through adherence to quality standards and continuous innovation. ISO certifications and compliance with international material specifications are non-negotiable for building trust with clients. Furthermore, the integration of Computer-Aided Design (CAD) and Computer-Aided Manufacturing (CAM) in designing molds represents a step towards future-ready practices, ensuring precision and adaptability to evolving customer demands.
Trustworthiness in this industry is built over time through consistent delivery of high-performance components. This reliability is often backed by detailed quality assurance processes, from raw material inspection to final product testing. Many industry leaders maintain an open line of communication with clients, providing transparency in production methods and enabling collaborative improvements.
In the competitive arena of manufacturing, gray iron sand casting holds its ground due to its balance of cost-effectiveness and quality. Industries like automotive, heavy machinery, and agriculture widely rely on this method for engine blocks, brake components, and structural supports. Each of these applications benefits from gray iron’s natural ability to absorb and dissipate vibrations, enhancing both longevity and performance.
The sustainability aspect of gray iron sand casting is also garnering attention. The process inherently supports recycling, with leftover molds and cores often reused in subsequent casts. Additionally, advancements in sand reclamation systems further reinforce the process’s eco-friendly stature, aligning with global trends toward sustainable industrial practices.
In conclusion, gray iron sand casting is a testament to the symbiotic relationship between material science and engineering innovation. Its enduring relevance in the modern manufacturing sector is attributed to a confluence of experience, expertise, authoritativeness, and trustworthiness. As companies seek to maximize efficiency and product quality, mastering the intricacies of this casting process is paramount. Future developments and technological integration promise even greater precision and reduced environmental impact, ensuring that gray iron sand casting remains a cornerstone of manufacturing excellence.