The aluminium rotor die casting process stands at the forefront of modern engineering and manufacturing, offering a seamless blend of durability, efficiency, and cost-effectiveness. With over two decades of experience in the die casting industry, I've witnessed firsthand the transformative impact this technology has had across multiple sectors, notably in the automotive and electrical engineering industries.
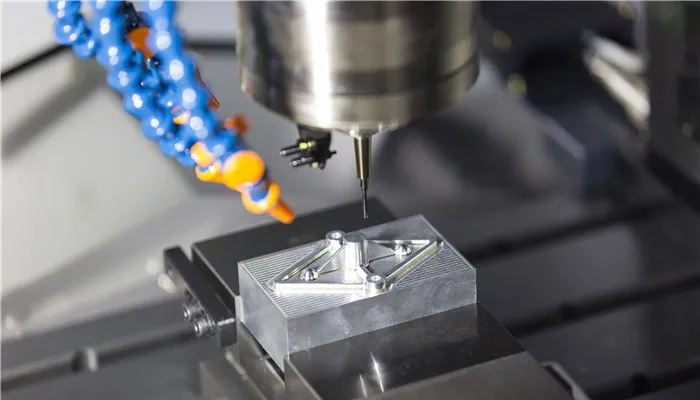
Aluminium rotor die casting is an intricate process that requires precision, expertise, and the right technology. The process begins with the preparation of the aluminium alloy, typically chosen for its lightweight properties and exceptional strength. Aluminium's excellent thermal and electrical conductivity make it the ideal choice for rotor production, contributing significantly to the performance and efficiency of devices.
The next phase involves the creation of a die — a meticulously crafted mold designed to shape the rotor precisely. This step demands expertise and precision engineering, as even slight deviations can lead to inefficiencies in the final product. Advanced Computer-Aided Design (CAD) software is commonly employed to design complex mold geometries, ensuring optimal performance and adherence to client specifications.
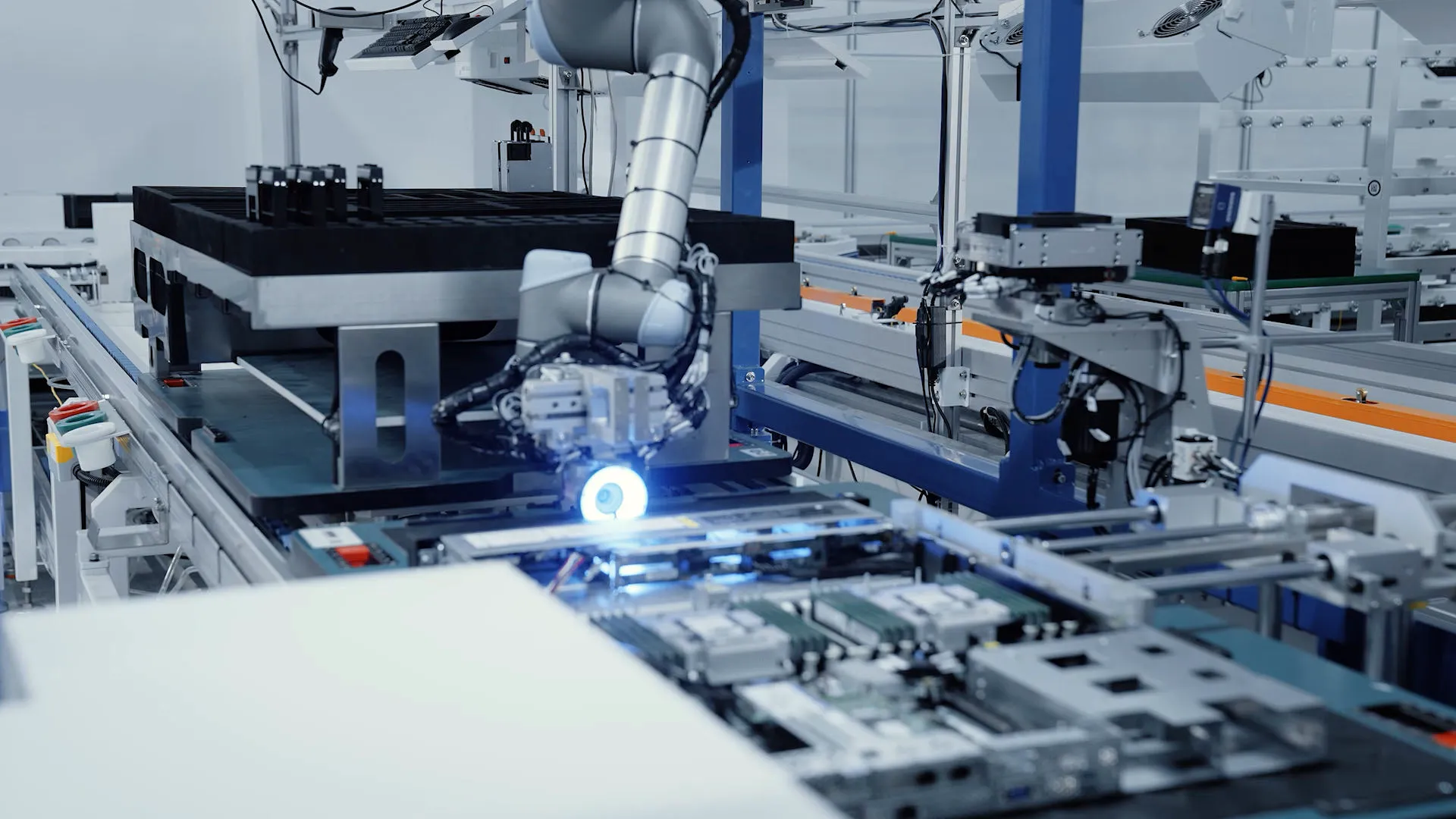
Once the die has been prepared, molten aluminium is injected into the mold under high pressure. This is where the magic of die casting truly shines. The high pressure ensures that the aluminium fills every cavity of the die, producing a rotor with high dimensional accuracy and a smooth surface finish. This step is conducted in highly automated facilities, prioritizing both speed and accuracy, and minimizing human error.
The integrity and performance of the cast aluminium rotor are pivotal, and this is ensured by rigorous quality control measures. Non-destructive testing methods, such as X-ray inspection and ultrasonic testing, are often employed to detect internal flaws and ensure the structural integrity of each rotor. This commitment to quality doesn't just end at manufacturing; a comprehensive understanding of the operational environment and conditions is essential to predict the rotor's lifespan and performance.
Energy efficiency is a critical factor in the modern world, and aluminium rotor die casting plays a crucial role in this arena. The lightweight nature of aluminium reduces the overall weight of the machinery in which it is incorporated, leading to enhanced energy efficiency and lower operational costs. Comparatively, aluminium rotors demonstrate superior efficiency over their iron counterparts, making them an indispensable component in green engineering solutions.
aluminium rotor die casting process
Recyclability is an often underplayed advantage of using aluminium in rotor die casting. The increasing global focus on sustainability and environmental responsibility places aluminium in a favorable position due to its ability to be recycled indefinitely without loss of quality. This characteristic not only mitigates environmental impact but also reduces material costs, presenting a sustainable choice for forward-thinking manufacturers.
In automotive applications, the aluminium rotor die casting process significantly contributes to the development of electric vehicles (EVs) and hybrid models. With governments worldwide pushing for reduced carbon emissions, the automotive industry has seen a surge in demand for components that align with energy-efficient technologies. Aluminium's applications extend beyond rotors in EVs, often used in battery casings and other essential components, highlighting its versatility and critical role in the transition towards sustainable urban mobility.
The aerospace industry also benefits immensely from aluminium rotor die casting. The weight-to-strength ratio of aluminium is particularly beneficial in aerospace applications, where each gram counts. The use of aluminium not only enhances fuel efficiency but also contributes to increased payload capacities and reduced greenhouse gas emissions.
Perhaps the most compelling testament to the strength of the aluminium rotor die casting process lies in its continual innovation and development. Investment in research and development ensures that the processes and materials remain at the cutting edge of technology. Innovations in alloy compositions, for example, continue to push the boundaries of what is possible, producing rotors that are lighter, stronger, and more efficient than their predecessors.
To wrap up, the aluminium rotor die casting process is a staple in today's technological landscape. Its embedded expertise and authoritative application across industries underscore not merely a method of production but a significant contributor to sustainable development and technological advancement. This article represents only the beginning of understanding the importance and potential of aluminium die casting, and its ever-expanding role in the future of manufacturing.