Navigating the world of manufacturing, sand casting foundries have long stood as indispensable pillars in the production of metal components. These specialized facilities blend traditional methodologies with cutting-edge innovations, ensuring precise and reliable production. Offering a unique blend of cost-efficiency and versatility, sand casting foundries accommodate a wide range of industries from automotive to aerospace and beyond.
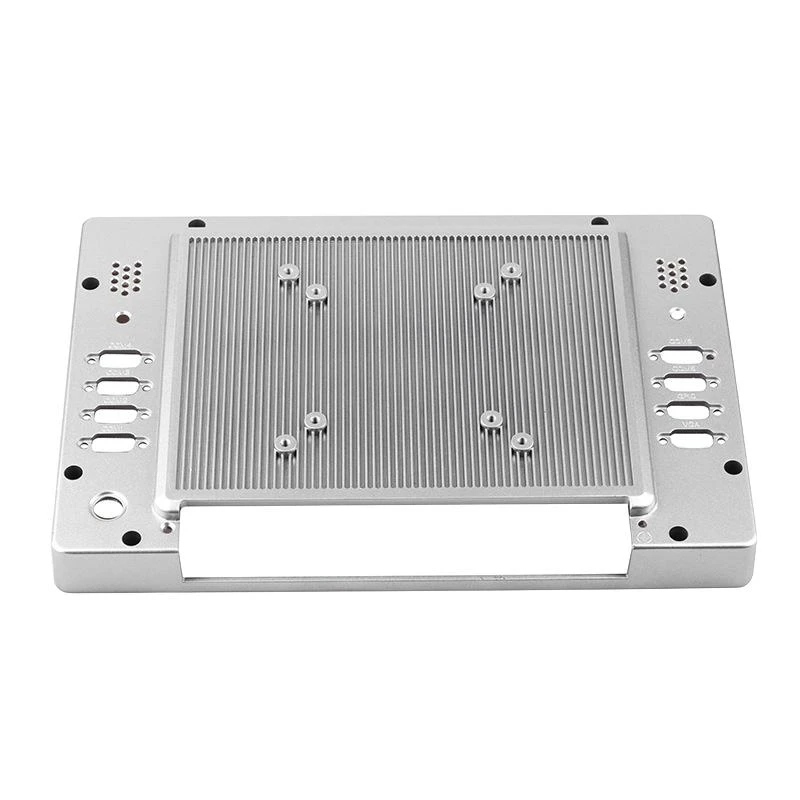
In the heart of every sand casting foundry lies the art of creating molds with sand. This practice capitalizes on the material's remarkable properties—its ability to withstand high temperatures and its ease of shaping. Specialists in these foundries employ various types of sand, including green sand, dry sand, and resin-bonded sands, each chosen for specific benefits such as strength, permeability, and surface finish quality.
The expertise found within a sand casting foundry is unparalleled. Foundry engineers meticulously plan each project, choosing the appropriate type of sand, metal alloy, and casting method tailored to the client's unique needs. This attention to detail ensures that each cast component meets exact specifications and quality standards. Their work encompasses the design of patterns and cores, essential elements that define each casting's shape and features. Expertise in these areas is backed by years of practical experience and a deep understanding of materials science.
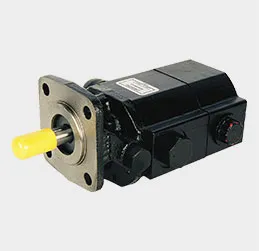
A cornerstone of authority within the industry, reputable sand casting foundries invest heavily in their workforce and technologies. Mastery of melting technologies is crucial, with induction furnaces and other modern melting apparatus ensuring that metals are properly liquified and handled. This not only influences the quality of the finished product but also guarantees safety and efficiency in the manufacturing process.
sand casting foundry
Trustworthiness in sand casting operations extends beyond the finished product to encompass sustainable practices and environmental responsibility. Many foundries are adopting advanced solutions for waste management and emissions reduction, recognizing the global call for eco-conscious manufacturing. By recycling sand and reducing waste, these foundries significantly lower their environmental footprint, underscoring their commitment to sustainability.
In product manufacturing, precision is paramount, and sand casting foundries excel in this area by harnessing innovative technologies. The integration of Computer-Aided Design (CAD) and Computer-Aided Manufacturing (CAM) systems enhances accuracy and consistency in the manufacturing process. Coupled with state-of-the-art quality control measures, from x-ray diagnostics to 3D scanning, foundries deliver components that meet stringent industry standards.
Collaborating with a trusted sand casting foundry offers several advantages to manufacturers. These foundries serve as strategic partners, providing solutions from initial design consultation to final product delivery. Clients benefit from the foundries' vast capabilities in producing intricate designs, custom alloys, and cost-effective large-scale production runs. This partnership allows businesses to focus on their core competencies while leaving the intricacies of metal casting to experts.
In conclusion, sand casting foundries provide the industry with a unique blend of artisanal skill and modern technology. Their commitment to quality, sustainability, and customer satisfaction makes them an invaluable partner in the manufacturing landscape. As industries continue to evolve, these foundries are poised to lead the way in producing innovative and reliable metal components that drive technological advancement.