OEM sand casting, a pivotal process in modern manufacturing, seamlessly combines time-honored techniques with cutting-edge technology, presenting a fascinating synthesis that caters to various industries. Emphasizing Experience, Expertise, Authoritativeness, and Trustworthiness, this article ventures into the intricacies and advantages of OEM sand casting, providing insights that align with Google’s SEO criteria.
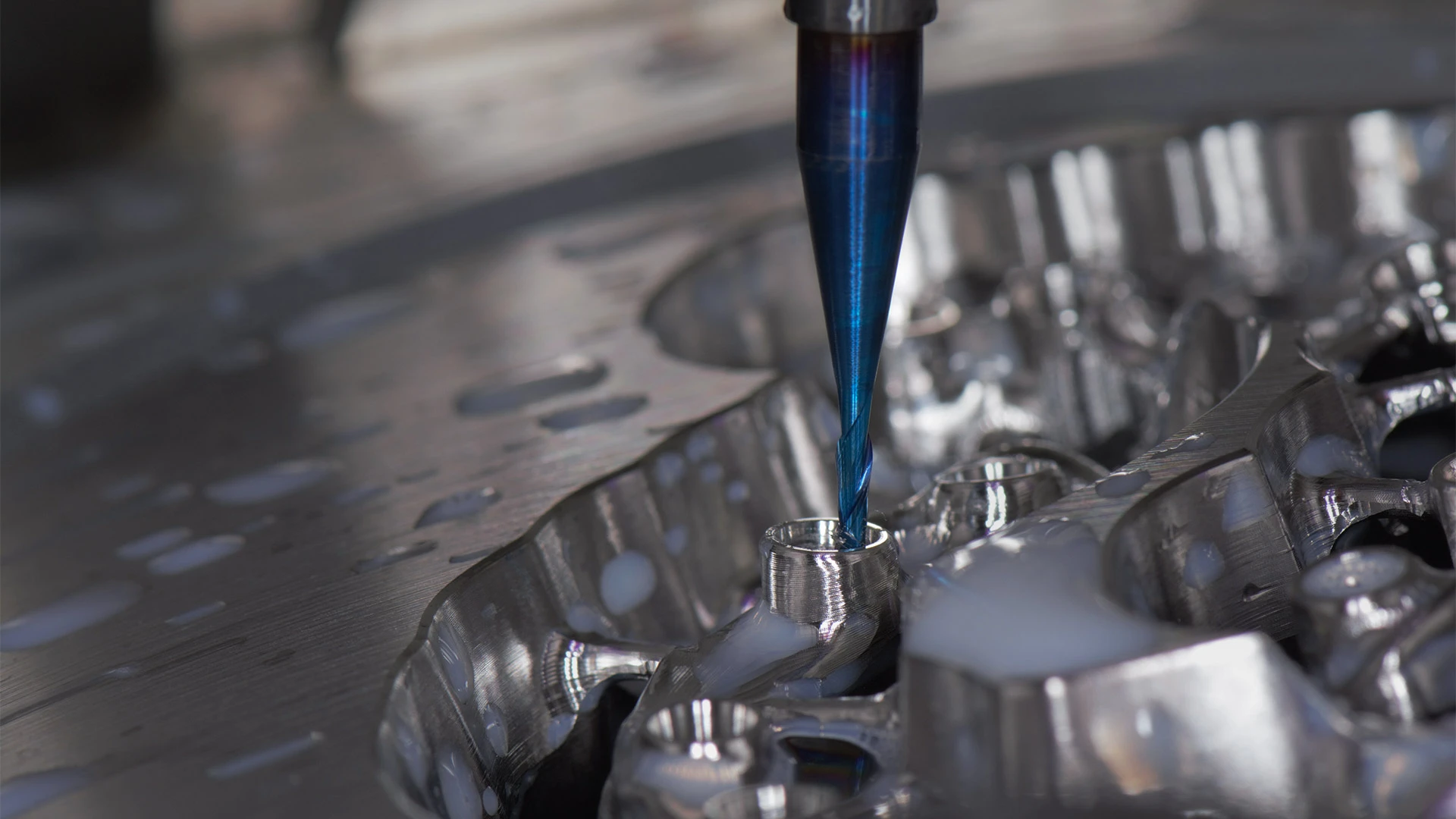
Sand casting, as a method, dates back centuries, showcasing its enduring importance. This casting process involves pouring molten metal into sand molds, making it especially suitable for creating intricate metal parts for diverse applications. Its versatility cannot be overstated; from automotive to aerospace, construction to marine industries, sand casting's capacity to produce complex hollow parts efficiently positions it as a preferred choice for manufacturers worldwide.
The expertise inherent in OEM sand casting is evident in its meticulous processes, which require detailed attention at every stage. Professionals in the field employ their extensive knowledge, ensuring each cast meets precise specifications. This expertise guarantees minimal material wastage, contributing to cost-effectiveness while maintaining high-quality standards. The process begins with pattern creation, followed by the formation of the mold, the careful choice of sand mix, and the controlled pouring of the molten metal. Each phase demands a thorough understanding to deliver products that surpass expectations.
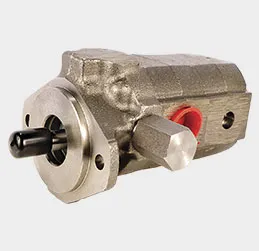
OEM sand casting holds authoritative standing owing to its adaptability in producing both small and large-scale runs. The technique supports a wide variety of metals, including aluminum, iron, steel, and bronze, offering manufacturers enormous flexibility in their production portfolios. This adaptability is a testament to the process's reliability, providing industries with robust and scalable solutions tailored to specific production needs.
oem sand casting
Trustworthiness in OEM sand casting hinges on quality control and consistent product performance. Foundries specializing in this process often operate under stringent quality management systems, ensuring every cast part adheres to international standards. Advanced technologies, such as computer-aided design (CAD) and computer-aided manufacturing (CAM), further bolster the trustworthiness of the products by enhancing precision and repeatability. These technologies also facilitate faster turnaround times, enabling manufacturers to meet market demands efficiently.
Furthermore, sustainability is an emerging focus within OEM sand casting, contributing to its growing appeal. The sand used in the casting process is often recyclable, reducing the environmental footprint associated with traditional manufacturing methods. This sustainable approach not only underscores the ecological responsibility embraced by the industry but also aligns with the increasing consumer demand for environmentally conscious production practices.
Manufacturers seeking to leverage OEM sand casting can enhance their operation's precision and efficiency by partnering with foundries that prioritize continuous improvement and innovation. This partnership allows them to remain competitive in a rapidly evolving market landscape, taking advantage of the latest advancements in casting technologies and methodologies.
In summary, OEM sand casting represents a cornerstone of modern manufacturing, offering unparalleled experience, unmatched expertise, inherent authority, and unwavering trust in its processes and outcomes. Its ability to blend traditional techniques with innovative solutions makes it indispensable for industries striving for excellence. By focusing on quality, sustainability, and technological advancement, OEM sand casting continues to evolve, promising to meet and exceed the complex requirements of contemporary manufacturing.