Low pressure aluminum casting has gained significant traction in the manufacturing sector, primarily due to its efficiency and cost-effectiveness in producing high-quality, complex components. This method utilizes gravity-fed systems to fill molds with molten aluminum at relatively low pressures, allowing for the production of intricate parts with remarkable accuracy and smooth surface finishes. Here, we delve into the intricacies of low pressure aluminum casting, highlighting its advantages, applications, and the expertise required to optimize its processes.
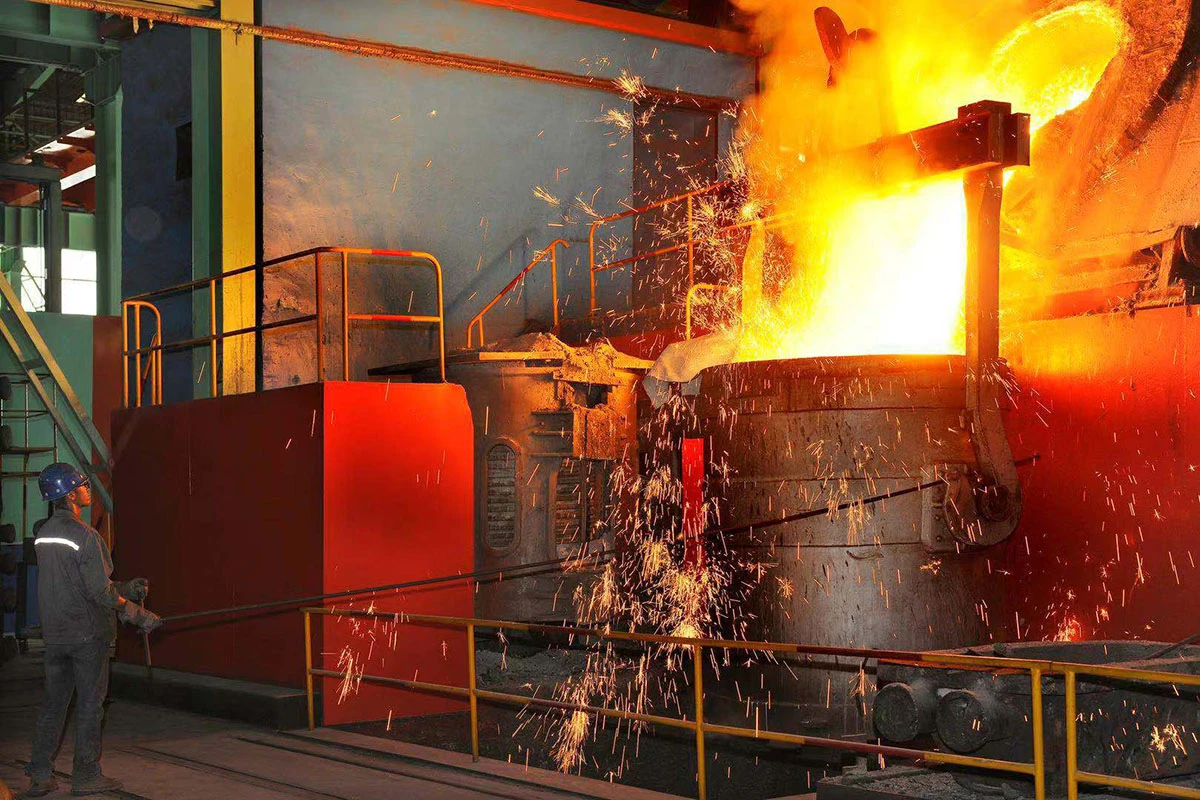
The technique revolves around the use of a sealed chamber where molten aluminum is incrementally pushed upwards into a mold by the application of low pressure, typically facilitated by controlled air pressure. This controlled filling process reduces turbulence and minimizes the risk of air entrapment, which is a common issue in traditional gravity casting methods. The result is a denser, higher integrity part with excellent mechanical properties.
An essential factor contributing to the success of low pressure aluminum casting is the material properties of aluminum itself. Aluminum is prized for its lightweight yet robust characteristics, high thermal and electrical conductivity, corrosion resistance, and recyclability. These properties make it indispensable in various sectors, including automotive, aerospace, and consumer electronics, where durability and performance are paramount.
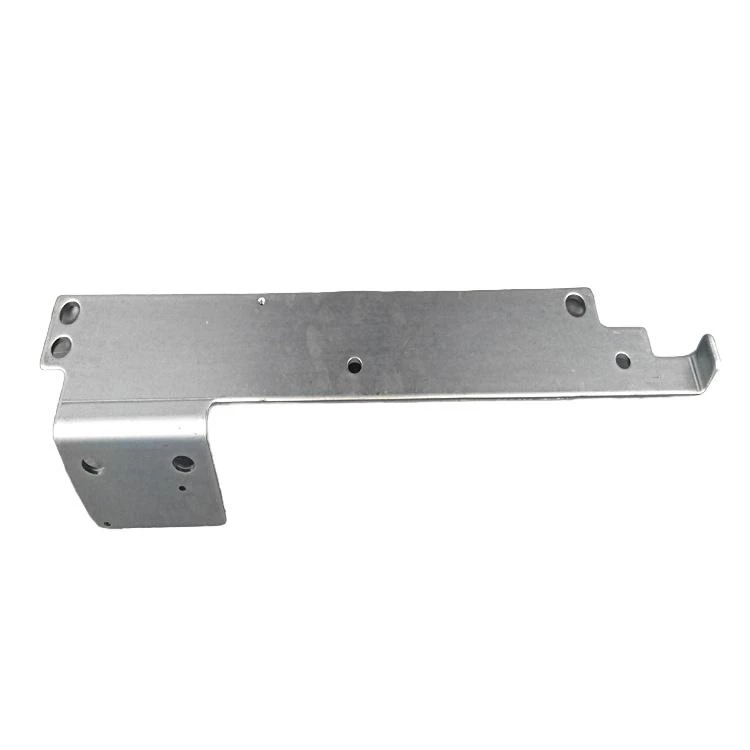
The automotive industry, in particular, benefits hugely from this casting method.
Low pressure aluminum casting facilitates the production of complex engine components, gearbox housings, and chassis parts. The precision offered ensures that manufacturers can meet stringent automotive standards and contribute to the industry's broader goals of reducing vehicle weight and improving fuel efficiency.
Aerospace applications also capitalize on the advantages of this technique. The need for precision and reliability cannot be understated in this field, where the slightest defect in a component can result in catastrophic outcomes. Low pressure casting serves to meet these high standards by producing components with superior structural integrity and dimensional accuracy.
low pressure aluminum casting
For businesses seeking to implement low pressure aluminum casting, understanding the importance of a meticulously controlled casting environment is crucial. Key expertise involves the meticulous monitoring and regulation of temperature and pressure throughout the process. A variance in these parameters can lead to defects such as incomplete fills or deformations. Additionally, knowledge of mold design and the thermal properties of aluminum alloys used can significantly impact the quality and performance of the final product.
One must approach the adoption of this technique with a comprehensive understanding of its environmental and economic advantages. Unlike other casting methods, low pressure aluminum casting generates minimal waste, and the leftover aluminum can be easily recycled. This not only reduces material costs but also aligns with sustainable manufacturing practices, a growing priority for industries worldwide.
Establishing trustworthiness and authority in the domain of low pressure aluminum casting involves continually investing in advanced technology and skilled personnel. The incorporation of automated systems and real-time monitoring tools can enhance process control, reduce human error, and improve the overall efficiency of the casting process. Additionally, continuous training and development programs for staff ensure a high level of expertise within the organization.
Professionals in the field recommend building strong relationships with raw material suppliers and investing in research and development. Staying abreast of the latest aluminum alloy developments and casting technologies can vastly improve output quality and provide a competitive edge.
Low pressure aluminum casting, with its myriad benefits and applications, stands as a testament to technological progress in the manufacturing industry. It offers a blend of precision, efficiency, and sustainability that is pertinent to the demands of modern engineering. By harnessing the knowledge and expertise required to master this technique, organizations can not only meet current market demands but can also set new standards for quality and innovation in the casting industry.