Injection die casting represents a pinnacle evolution in the manufacturing processes, combining the precision of injection molding with the robustness of die casting. It has carved a niche in the production of high-integrity components used in diverse industries such as automotive, aerospace, electronics, and consumer goods. Its perfect amalgamation of technology, efficiency, and scale makes it indispensable.
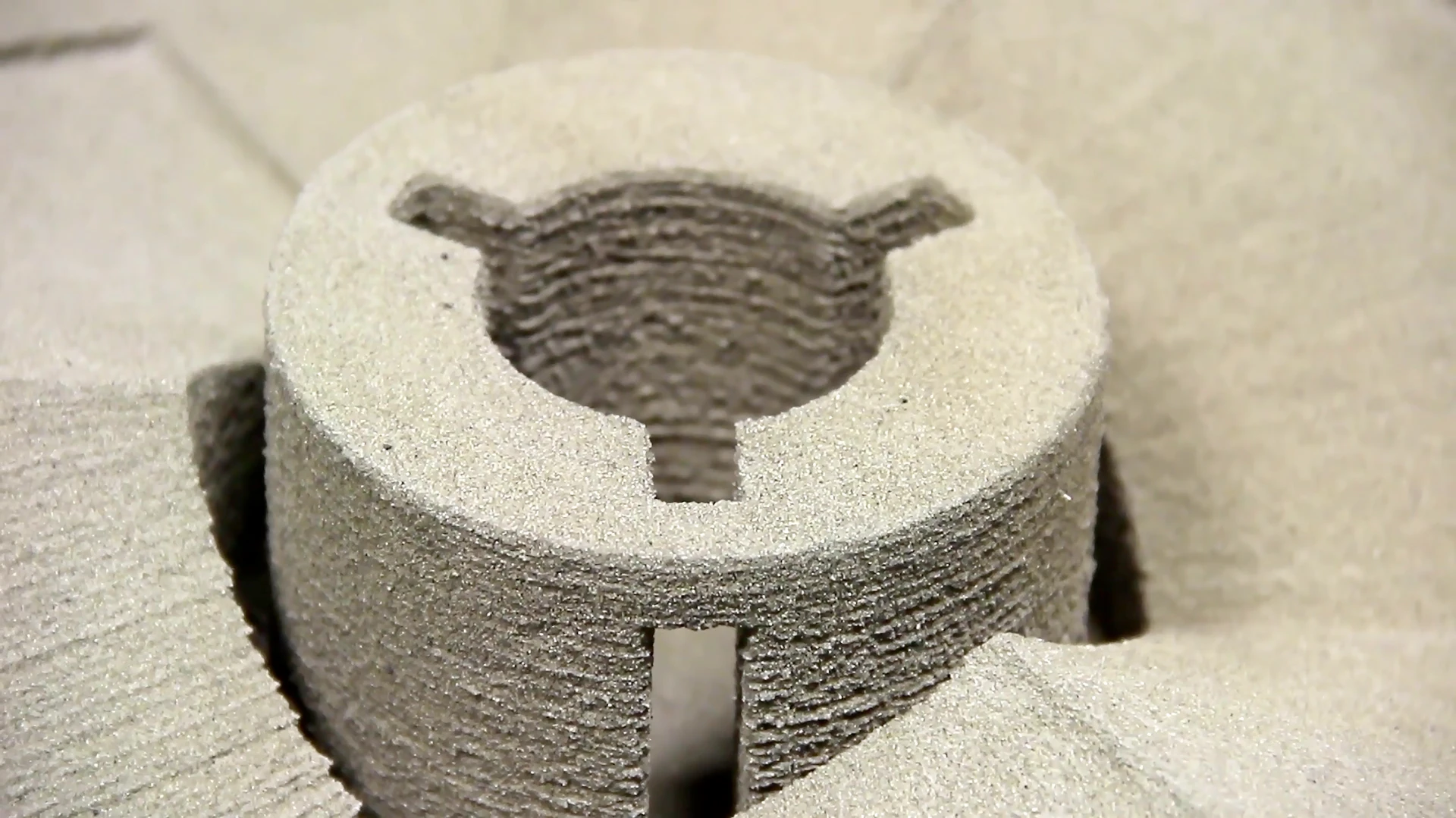
The core of injection die casting lies in its ability to produce high-tolerance components with complex geometries at a rapid pace. This process is meticulously designed to optimize both speed and accuracy, thus allowing manufacturers to produce superior quality parts at reduced costs. By using non-ferrous metals, typically aluminum, zinc, and magnesium, it ensures lightweight yet strong components, essential for modern applications where efficiency in material use is pivotal.
From an expertise standpoint, the process of injection die casting demands a profound understanding of material science and thermodynamics. The dynamics within the die determine the final properties of the product, making temperature control and pressure settings crucial. Professionals in this field must possess a deep knowledge of these aspects to manipulate the molten metal optimally, ensuring that the metal fills the mold perfectly without leaving any voids that could compromise structural integrity.
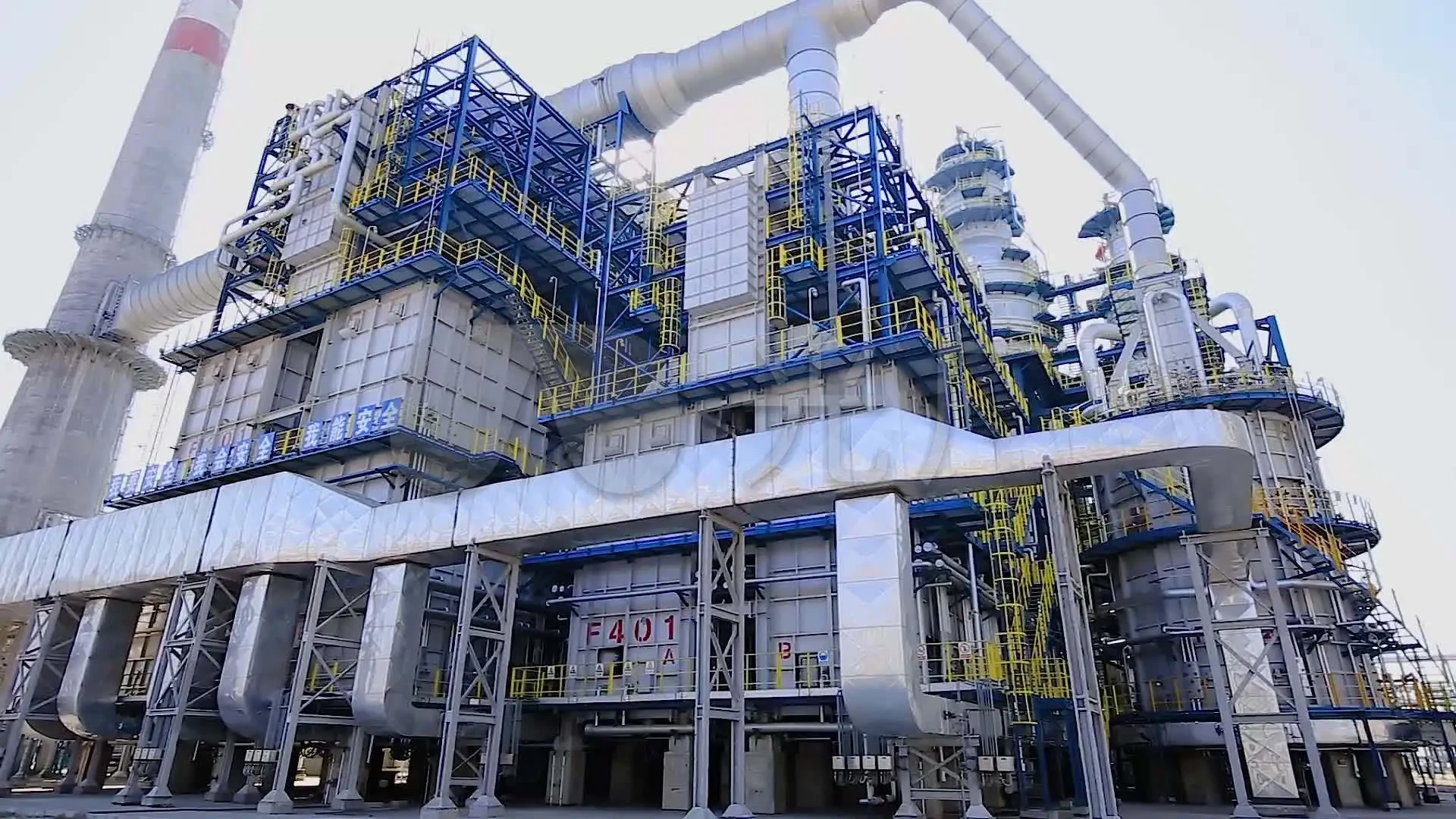
Authoritativeness in injection die casting is often showcased by the standards and certifications these processes adhere to. Highly regulated sectors like aerospace and automotive industries demand rigorous testing and validation of the components crafted through this method. As such, manufacturers need to comply with ISO standards and other industry-specific certifications to assure clients of the reliability and durability of their products. This adherence not only guarantees product efficacy but also builds a strong foundation of trust with end clients.
injection die casting
The trustworthiness of parts produced through injection die casting is further cemented by the technological advancements integrated into the process. Modern die casting machines now utilize real-time data analytics and process monitoring systems that ensure minimal deviation from specified tolerances. What's more, these systems allow for continuous improvement of processes, reducing waste and increasing yield, which in turn enhances both environmental sustainability and economic viability.
Real-world experience from leading firms utilizing injection die casting exhibits trends towards innovation and customization. For instance, the automotive industry calls for components that not only provide strength but also appeal aesthetically to consumers.
Injection die casting supports this by offering surface finishing options that enhance the aesthetic of parts while maintaining functional properties. Similarly, in the electronics sector, miniaturization of components is key, and the precision offered by this process satisfies the industry's quest for smaller, yet more powerful parts.
In conclusion, injection die casting stands as a testament to the synergy of human expertise, technological innovation, and rigorous quality assurance. Industries worldwide continue to endorse this process not only for its proven efficiency and cost-effectiveness but also for its ability to meet the demanding standards of today’s hyper-competitive markets. As technology advances, it is anticipated that injection die casting will further evolve, providing even greater opportunities for innovation and excellence in product manufacturing.