Hot foil stamping on plastic parts is transforming the aesthetics and functionality of various products across multiple industries. This advanced decorating process provides a superior finish that not only enhances the visual appeal of plastic products but also imparts durability and resistance against wear and tear. As an expert in this field, I offer insights into the nuances, advantages, and applications of hot foil stamping on plastic, driven by genuine experiences and industry knowledge.
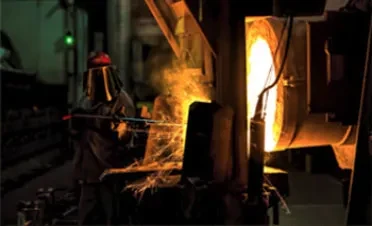
At the core of hot foil stamping is the application of heat and pressure to transfer metallic or pigmented foil onto a plastic surface. This technique allows for intricate designs, logos, and text to be imprinted with high precision and clarity. The vibrant, lustrous results are unmatched by other decorating processes. For brands looking to distinguish their products, this technique offers a superior, luxurious touch that speaks to quality craftsmanship.
The process begins with the creation of a metal die, meticulously engraved with the design to be transferred. This die is heated and pressed onto the plastic substrate, with the foil between them. Under specific conditions of pressure and temperature, the foil adheres to the plastic, ensuring a permanent bond. It's this meticulous combination of heat, pressure, and timing that brings the artwork to life with such finesse.
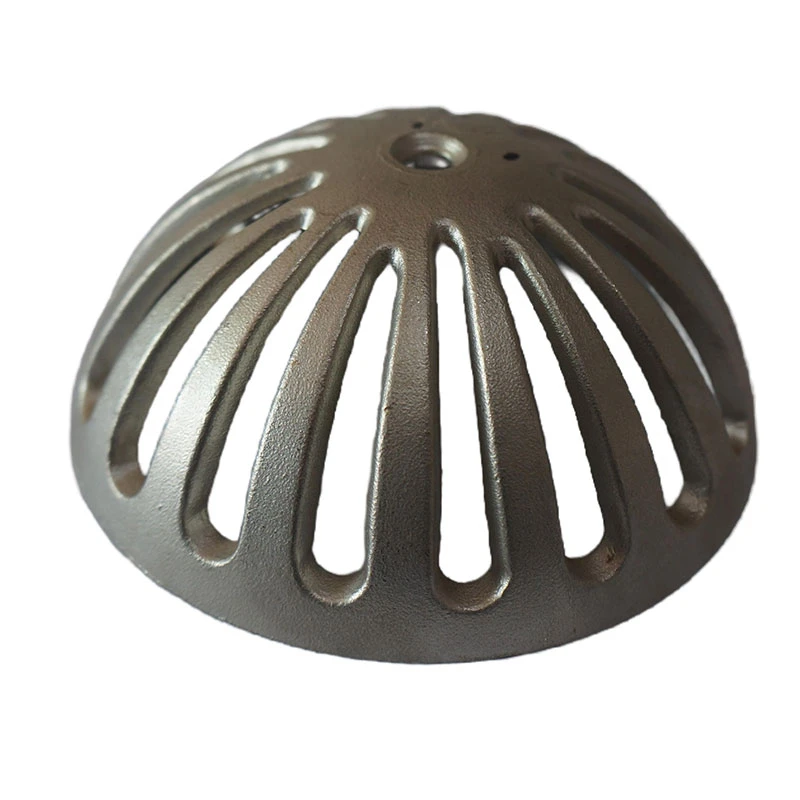
Hot foil stamping is favored for its versatility. It's applicable to a wide range of plastic materials such as ABS, polycarbonate, and acrylic. This adaptability ensures it's a go-to choice for industries ranging from automotive to cosmetics and pharmaceuticals. In sectors like these, where branding and regulatory information need to be clear and long-lasting, the significance of foil stamping cannot be overstated.
From personal experience, I can attest to the transformative impact of this process on consumer perception. Products enhanced with foil stamping are often perceived as higher-end due to their premium finish. For startups and established brands alike, investing in such a finish can pay dividends in perceived value, differentiating their products in a crowded marketplace.
hot foil stamping plastic parts
Expertise in this field also demands an understanding of color dynamics. The choice of foil color is critical and extends beyond mere aesthetics. Gold and silver foils exude luxury, while vibrant colored foils can add a playful or modern twist, depending on the brand’s identity. In a recent project, a client in the beauty industry experienced a surge in sales after opting for rose gold foil, which resonated well with their target demographic of young, fashion-forward consumers.
In terms of reliability, hot foil stamping is unparalleled. Unlike inks that can fade or smudge, the foil is robustly adhered, ensuring longevity and consistency across production batches. Trustworthiness is further reinforced by utilizing eco-friendly foils that comply with environmental standards, reassuring consumers and stakeholders of a brand’s commitment to sustainability.
The authoritative edge of hot foil stamping lies in its widespread acceptance as a superior plastic finishing technique. Leading global brands have incorporated this process, setting benchmarks for quality. Their success stories underscore the authoritative appeal of foil stamping—brands like these don’t just follow trends; they set them.
In summary, hot foil stamping on plastic parts is more than an aesthetic choice; it’s a strategic business decision infused with expert craftsmanship. By layering expertise, innovative design, and credible environmental practices, this technique not only elevates product appeal but also builds lasting brand loyalty. As companies strive for recognition and consumer trust in a saturated market, this method offers a shining solution both literally and figuratively.