Die casting technology has emerged as a cornerstone in the manufacturing world, particularly for products that require precision, durability, and high production efficiency. This advanced method of shaping metal involves forcing molten metal into a mold cavity under high pressure. Its prominence in industries such as automotive, aerospace, and consumer electronics underscores its supremacy. Exploring the nuances of die casting can significantly enhance product quality and market competitiveness.

A key advantage of die casting technology is its unparalleled precision. The process produces components with exceptional detail and a high degree of consistency, making it an ideal choice for industries that demand intricate designs and tight tolerances. For instance, in the automotive sector, die-cast parts such as engine blocks, transmission cases, and structural components benefit from these properties, ensuring optimal performance and reliability in demanding environments. Such precision not only elevates product quality but also reduces the need for further machining, thereby minimizing costs and production time.
In terms of expertise, companies specializing in die casting technology invest heavily in research and innovation to stay ahead. The expertise involves understanding the complex dynamics of metal flow, cooling rates, and material properties. Advanced computational simulations and process modeling have been incorporated to predict and optimize outcomes. The deployment of cutting-edge technology, such as real-time monitoring and automated systems, further enhances the efficiency and quality of the die casting process. Collaborations with material scientists and engineers lead to the development of new alloys and methods, broadening the possibilities of die casting applications.
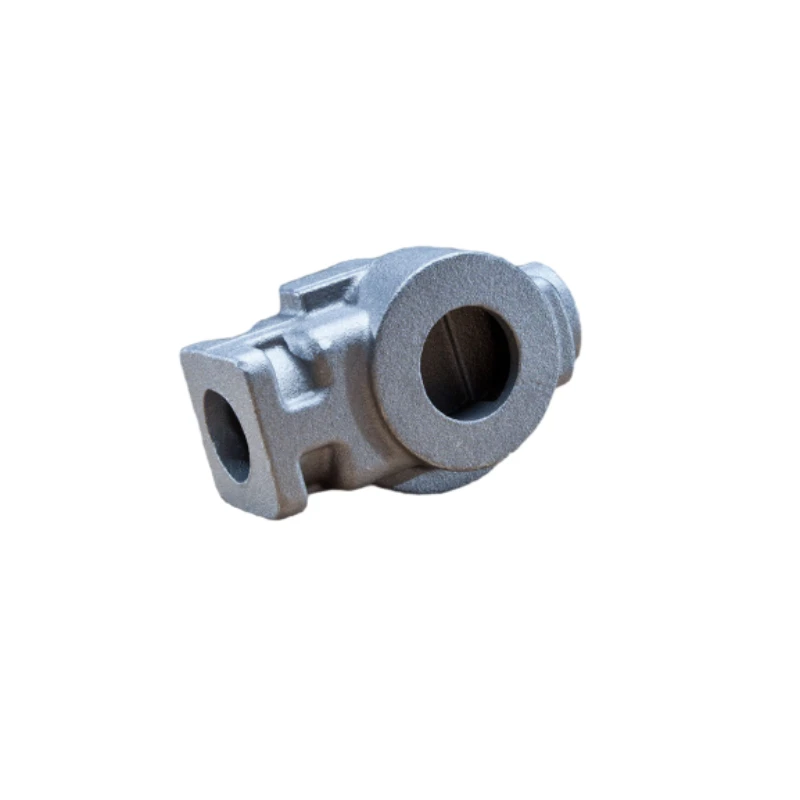
From an authority perspective, die casting is often endorsed by leading industry groups and standards organizations. Associations such as the North American Die Casting Association and the European Die Casting Association provide rigorous guidelines and certifications that manufacturers must adhere to. These standards ensure that products not only meet but exceed industry expectations for safety, durability, and environmental impact. Such endorsements reinforce the credibility of die-cast products in the global market, making them a trusted choice for critical applications.
Trustworthiness in die casting technology is underscored by the long-term reliability of its products. The durability of die-cast components is widely recognized, with many items exhibiting excellent wear resistance and strength. This durability translates to a longer lifespan, less frequent maintenance, and reduced total ownership costs for end-users. Industries reliant on die casting can confidently deploy these components, knowing they meet stringent performance requirements over extended periods. The inherent recyclability of die-cast metals also contributes to sustainability efforts, adding an additional layer of trust in environmentally conscious markets.
die casting technology
Practical experience with die casting technology underscores its transformative impact on product development cycles. By reducing lead times and enabling rapid prototyping, die casting allows for quick iterations and adaptations to market demands. This agility is a critical factor in today’s competitive landscape, especially for consumer electronics, where time-to-market can determine a product’s success or failure. Manufacturers adept in die casting can swiftly respond to design changes or unforeseen issues, maintaining a competitive edge.
Optimizing products through die casting involves strategic considerations of the entire production process. Selection of the appropriate alloy is crucial, as it influences the mechanical properties and cost-effectiveness of the final product. Commonly used alloys include aluminum, magnesium, and zinc, each offering unique benefits. Aluminum, known for its lightweight yet robust characteristics, is preferred in applications where weight reduction is essential. Magnesium alloys are lauded for their excellent strength-to-weight ratio, ideal for aerospace purposes, while zinc offers superior ductility and impact strength, suitable for complex, smaller components.
Manufacturers must also tailor their die casting techniques to suit specific product requirements. Hot chamber and cold chamber die casting methods each have distinct advantages depending on the material and design complexity. Understanding these techniques enables manufacturers to optimize production efficiency and component performance, further establishing their expertise in the field.
In conclusion, die casting technology stands as a pillar of modern manufacturing, meriting recognition for its precision, expertise, authority, and trustworthiness. Products fashioned through die casting exhibit exceptional quality and reliability, while the technology itself continues to evolve, driven by innovation and industry collaboration. For stakeholders across various sectors, investing in die casting translates to superior products, enhanced market reputation, and sustainable growth in an increasingly competitive global marketplace.